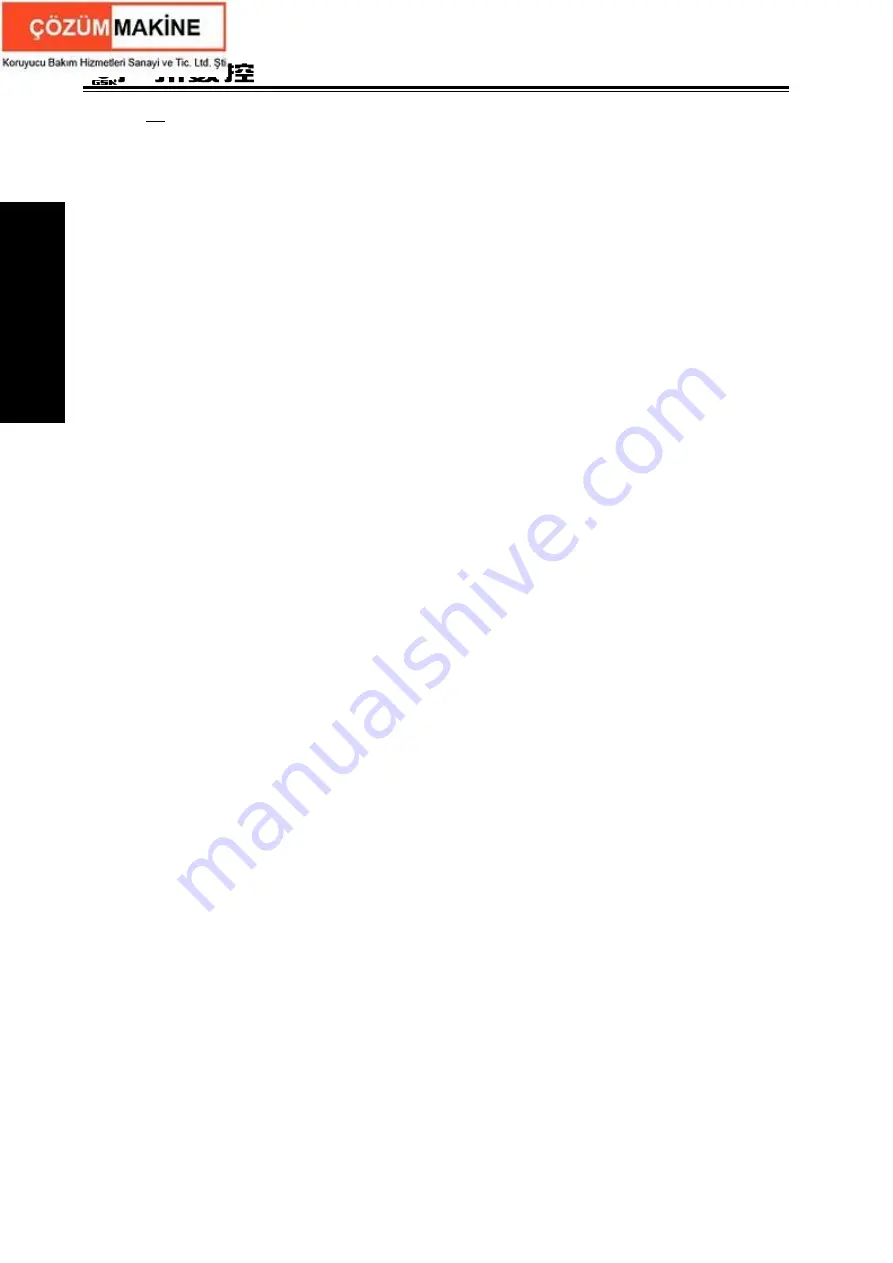
GSK980TDc Turning CNC System User Manual
100
Ⅰ
Progra
mming
Δ
d is reserved and the data value is switched to the corresponding value to save to No.051
after W(
Δ
d) is executed. The value of system parameter No.051 is regarded as the tool
infeed clearance when R(e) is not input.
e: it is Z tool retraction clearance in roughing, its value: 0~99.999(unit: mm) without sign
symbol, and the direction of tool retraction is opposite to that of tool infeed, the specified
value e is reserved and the data value is switched to the corresponding value to save to
No.052 after R(e) is executed. The value of system parameter No.052 is regarded as the
tool retraction clearance when R(e) is not input.
ns: Block number of the first block of finishing path.
nf: Block number of the last block of finishing path.
Δ
u
:
it is X finishing allowance in roughing, its range: ±99999999×least input increment(X
coordinate offset of roughing contour corresponding to the finishing path, i.e. X absolute
coordinate difference between A’ and A.(diameter, unit: mm/inch, with sign symbol).
Δ
w
:
it is Z finishing allowance in roughing, its range: ±99999999×least input increment(Z
coordinate offset of roughing contour corresponding to the finishing path, i.e. Z absolute
coordinate difference between A’ and A.(diameter, unit: mm/inch, with sign symbol).
F: Cutting feedrate; S: Spindle speed; T: Tool number, tool offset number.
M, S, T, F: They can be specified in the first G72 or the second ones or program ns
~
nf. M, S, T,
F functions of M, S, T, F blocks are invalid in G72, and they are valid in G70 finishing blocks.
Execution process:
Fig. 3-28
①
X rapidly traverses to A’ from A point, X travel is
Δ
u, and Z travel is
Δ
w;
②
X moves from A’ is
Δ
d( tool infeed), ns block is for tool infeed at rapid traverse speed
with G0, is for tool infeed at G72 feedrate F in G1, and its direction of tool infeed is
that of A
→
B point;
③
X executes the cutting feeds to the roughing path, and its direction is the same that of
X coordinate B
→
C point;
④
X, Z execute the tool retraction e (45°straight line)at feedrate, the directions of tool
retraction is opposite to that of tool infeed ;
⑤
X rapidly retracts at rapid traverse speed to the position which is the same that of Z
coordinate;
⑥
After Z tool infeed (
Δ
d+e)again is executed, the end point of traversing tool is still on
the middle point of straight line between A’ and B’(the tool does not reach or exceed
B’), and after Z executes the tool infeed (
Δ
d+e)again, is executed;
③
after the tool
infeed (
Δ
d+e) is executed again, the end point of tool traversing reaches B’ point or
exceeds the straight line between A’
→
B’ point and Z executes the tool infeed to B’
point, and then the next step is executed;
⑦
Cutting feed from B’ to C’ point along the roughing path;
⑧
Rapidly traverse to A from C’ point and the program jumps to the next clock following
nf block after G71 cycle is completed.
Summary of Contents for GSK980TDc
Page 17: ...I Programming ...
Page 18: ...GSK980TDc Turning CNC System User Manual ...
Page 190: ...GSK980TDc Turning CNC System User Manual 172 Ⅰ Programming ...
Page 191: ...Ⅱ Operation Ⅱ Operation ...
Page 192: ...GSK980TDc Turning CNC System User Manua Ⅱ Operation ...
Page 326: ...GSK980TDc Turning CNC System User Manual 306 Ⅱ Operation ...
Page 327: ...Ⅲ Connection Ⅲ Connection ...
Page 328: ...GSK980TDc Turning CNC System User Manual Ⅲ Connection ...
Page 470: ...GSK980TDc Turning CNC System User Manual 448 Ⅲ Connection ...