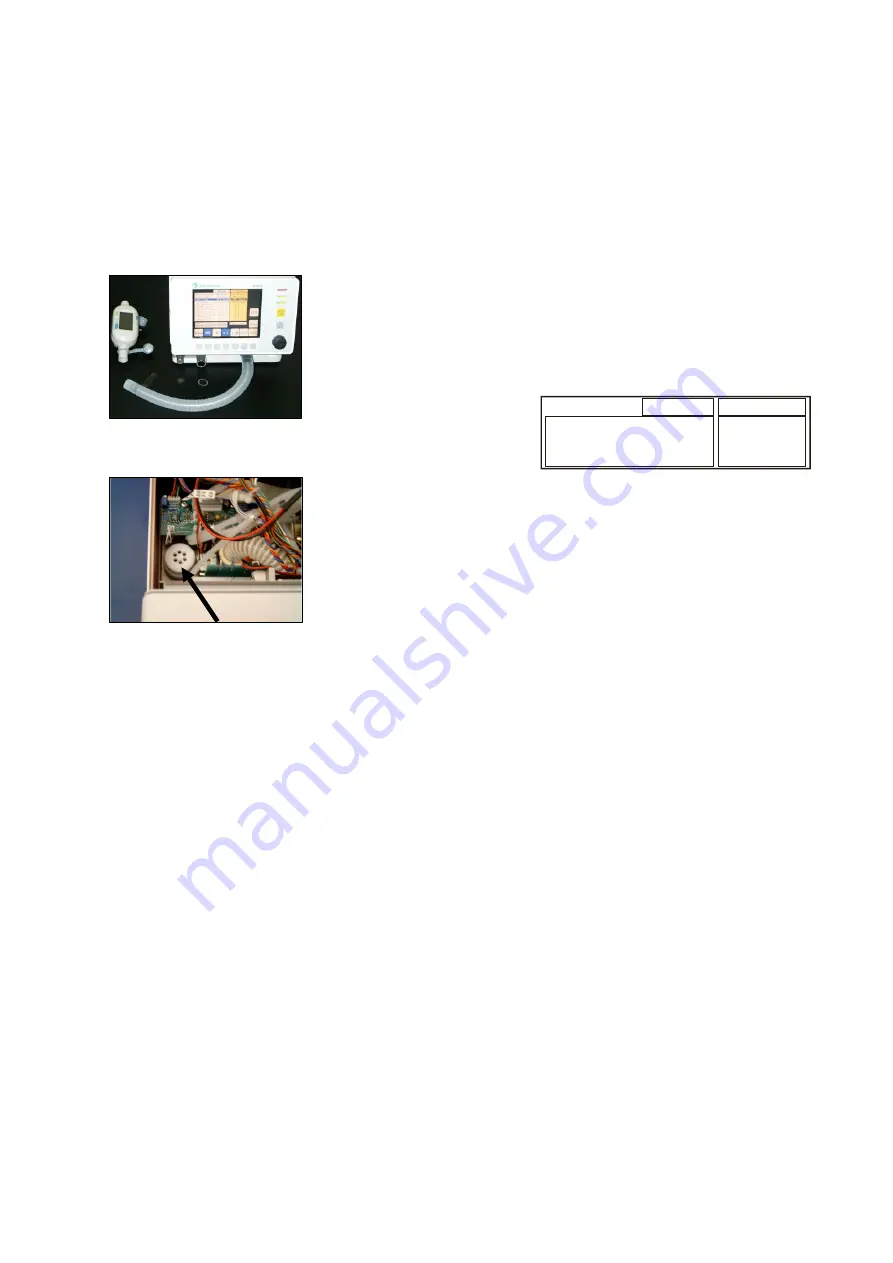
4 Test and calibration
TRM, Centiva/5 Plus, M1047448/CM-922026, rev. 3.50.a of 11/05
4-30
RATED
ACTUAL
92 mbar
500 Digit
20 l/min
250 Digit
75,2 mbar
510 Digit
530 Digit
251 Digit
Pat.Pressure
Exp.flow
AIR flow ON
O2 flow ON
4.7.7 Overpressure
relief valve calibration
The overpressure relief valve calibration is performed with the use of the service
mode.
To calibrate the overpressure relief valve:
1.
Ensure that the system is turned OFF and line power is disconnected.
2.
Open main engine according to section 7.2.4.
3.
Re-insert exp. valve assembly.
4.
Connect line power and gas supply and turn ON the system.
5.
Verify that the system performs the power-up test.
6.
Start the service mode according to section 4.3.
7.
Connect one tube to the
inspiratory port.
8.
Seal the open end of the tube
with a 22 mm stopper plug
(e.g. P/N 2900-0001-000).
9.
Select the “Air” and “x 1” button.
10.
Use the ComWheel to increase the AIR flow to read 20 L/Min. Note: Increase
flow slowly by small steps to avoid oscillation of the over pressure relief
valve.
11.
Watch the “Pat.Pressure” increase and stabilize at a certain pressure level.
12.
Check the “Pat.pressure” “Actual” to be at 75
±
2 mbar.
13.
If not, readjust the overpressure relief valve by turning the valve cap until
“Pat.pressure” “Actual“ reads 75
±
2 mbar.
Turning clockwise increases pressure, counterclockwise lowers pressure.
Summary of Contents for Centiva/5 Plus
Page 1: ...GE Healthcare Centiva 5 Plus Technical Reference Manual ...
Page 14: ...1 Introduction TRM Centiva 5 Plus M1047448 CM 922026 rev 3 50 a of 11 05 1 8 Notes ...
Page 20: ...2 Theory of operation TRM Centiva 5 Plus M1047448 CM 922026 rev 3 50 a of 11 05 2 6 ...
Page 27: ...2 Theory of operation TRM Centiva 5 Plus M1047448 CM 922026 rev 3 50 a of 11 05 2 13 ...
Page 30: ...2 Theory of operation TRM Centiva 5 Plus M1047448 CM 922026 rev 3 50 a of 11 05 2 16 Notes ...
Page 34: ...3 Post service check out TRM Centiva 5 Plus M1047448 CM 922026 rev 3 50 a of 11 05 3 4 Notes ...
Page 70: ...4 Test and calibration TRM Centiva 5 Plus M1047448 CM 922026 rev 3 50 a of 11 05 4 36 Notes ...
Page 154: ...7 Repair procedures TRM Centiva 5 Plus M1047448 CM 922026 rev 3 50 a 7 48 Notes ...
Page 181: ...9 Schematics and Diagrams TRM Centiva 5 Plus M1047448 CM 922026 rev 3 50 a of 11 05 9 5 ...
Page 212: ...11 Optional accessories TRM Centiva 5 Plus M1047448 CM 922026 rev 3 50 a of 11 05 11 6 Notes ...
Page 213: ...TRM Centiva 5 Plus M1047448 CM 922026 rev 3 50 a of 11 05 Notes ...