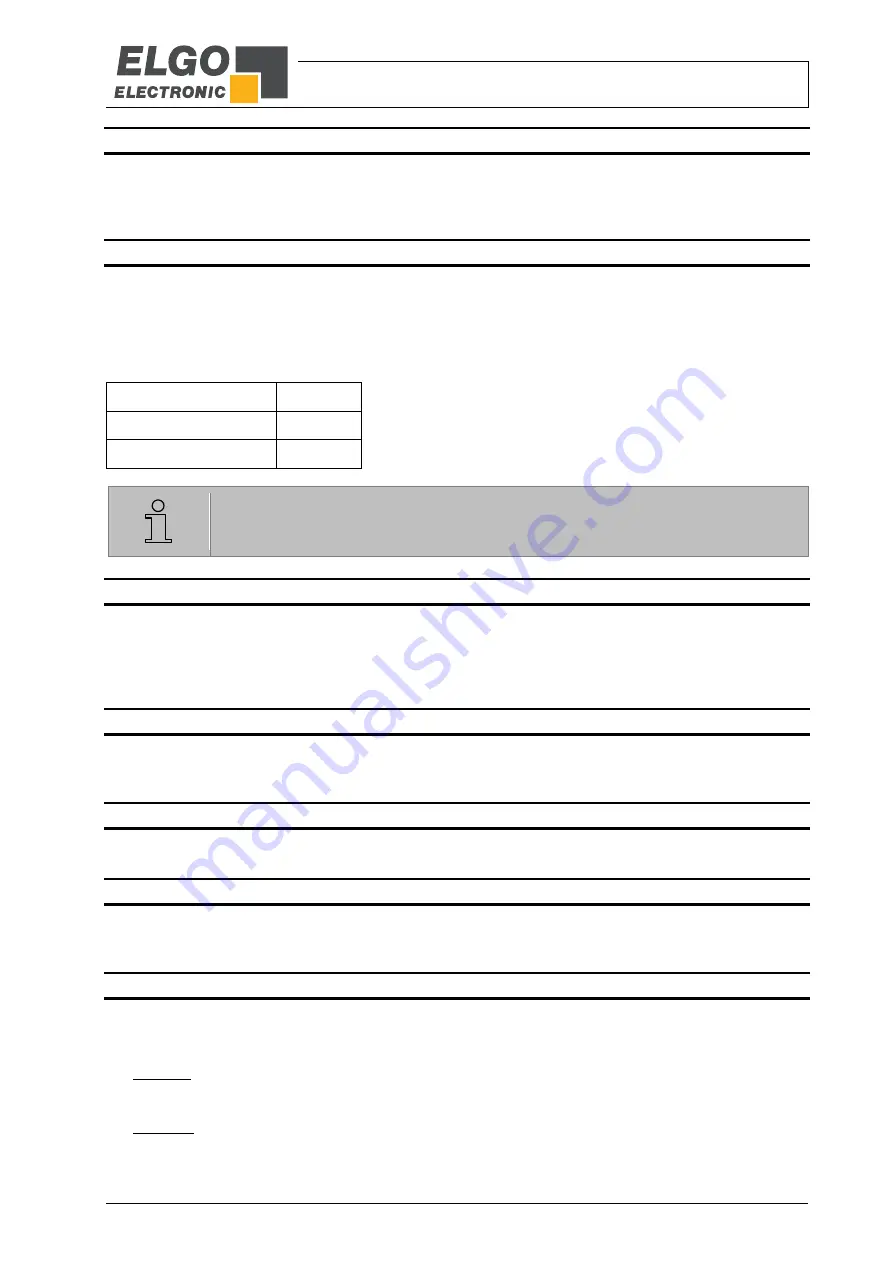
Service Mode / Parameter Level
- 35 -
11.5.2
Tolerance Window
The tolerance window is reached when the actual value is equal to the target value ± parameter "Tolerance
Window". If an axis is within the tolerance window, it is not moved when a new start command is issued. The
respective “Tolerance Zone” output of the axis is also set when the tolerance window is reached.
11.5.3
Manipulation
The manipulation window is used to adjust the actual value. If the actual value is within the target value ± pa-
rameter "Manipulation", the actual value is equated with the target value. The real target value remains stored in
the background, because only the display is manipulated (thus no positioning errors will add up).
Example: Entered Value = 0.2 mm (i.e. Tolerance Window ± 0.2 mm)
Target value: 100,0 mm
Internal actual value: 99,8 mm
Displayed actual value: 100,0 mm
REMARK!
The tolerance window should be set to zero before starting to operate.
11.5.4
Spindle Compensation
To compensate for spindle tolerances, the target position must always be approached from the same direction,
i.e. in one direction the target position is exceeded by the value set here. After expiration of the backlash dwell
time that was entered in register
Menu
Times
Spindle Compensation
, the axis moves back to the target
position.
11.5.5
Forced Loop
If during absolute positioning the target value is within the range ± value of the “forced loop” window, a forced
loop is run.
11.5.6
Reference Value
A reference value resp. reference position can be specified here.
11.5.7
Retract Length
Depending on the selected retract mode, the axis is moved by the value "Retract Length".
The retract function is controlled by the internal automatic cutting machine.
11.5.8
End Position Min/ Max
These two values can be used if there are no mechanical limit switches available or in addition to existing me-
chanical limit switches.
The minimum software end position should be between the smallest length/position to be machined and 0
(or shortly before the mechanical limit switch).
The maximum software end position should be between the largest length/position to be machined and the
maximum length (or shortly before the mechanical limit switch).
If one of these two values is reached, the positioning procedure is interrupted.
Summary of Contents for P40T-002 Series
Page 49: ...Service Mode Parameter Level 49 11 11Sub Menu Times System Figure 33 System Times ...
Page 83: ... 83 Notes ...
Page 84: ... 84 Notes ...
Page 85: ... 85 Notes ...