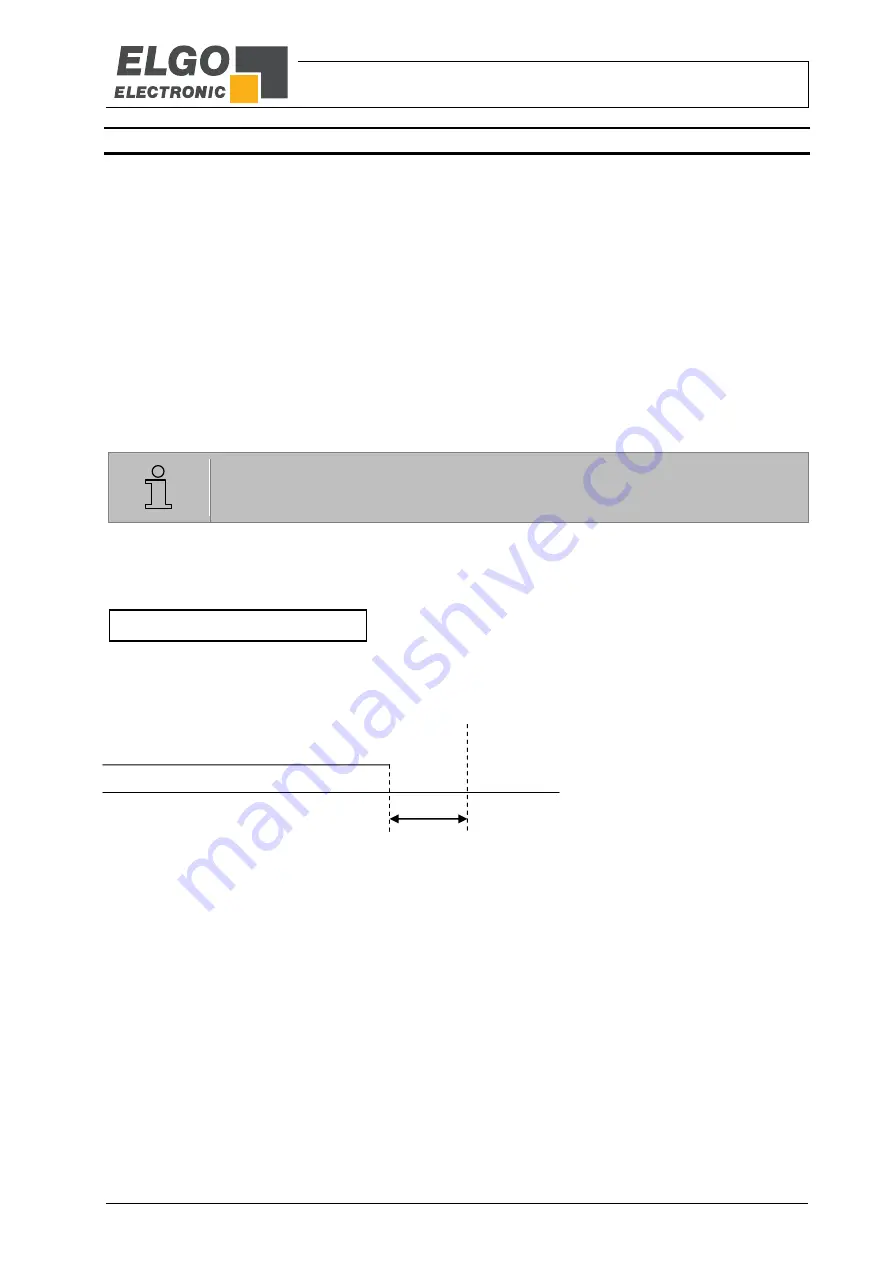
Service Mode / Parameter Level
- 33 -
11.5.1
Creep Speed / Correction Stop
Creep speed (forward / backward) = slow speed
Distance to the target position at which the controller switches from slow speed to creep speed. The output slow
speed will be switched off.
Correction Stop (forward) / Correction Stop (backward)
This parameter serves to compensate the overrun distance from the switch-off point of the motor to standstill.
Example: The target position is overrun by 0.2 mm constantly. The data entry has to be 2.
The stop command is thus moved forward by 0.2 mm.
During first start-up, the stop offset is set first to "0" in order to be able to calibrate the overrun accurately.
For an exact positioning the stop offset should be as small as possible (0.0 … 0.2 mm) i.e. the mechanical
friction should be steady over the entire retract distance and the slow speed and/or creep speed must be
accordingly small adjusted. The value in register slow speed must be larger than in creep speed.
REMARK!
When positioning with PID, the correction stop serves as a tolerance window.
Example: Positioning with 1 speed
In principle, the following applies when setting the speeds:
Creep speed = Correction stop
Figure 24: Creep speed (1 speed)
Target: 100.0 mm
Correction stop
Creep speed
Creep speed: 1.0 mm
Correction:
1.0 mm
99.0 mm
Summary of Contents for P40T-002 Series
Page 49: ...Service Mode Parameter Level 49 11 11Sub Menu Times System Figure 33 System Times ...
Page 83: ... 83 Notes ...
Page 84: ... 84 Notes ...
Page 85: ... 85 Notes ...