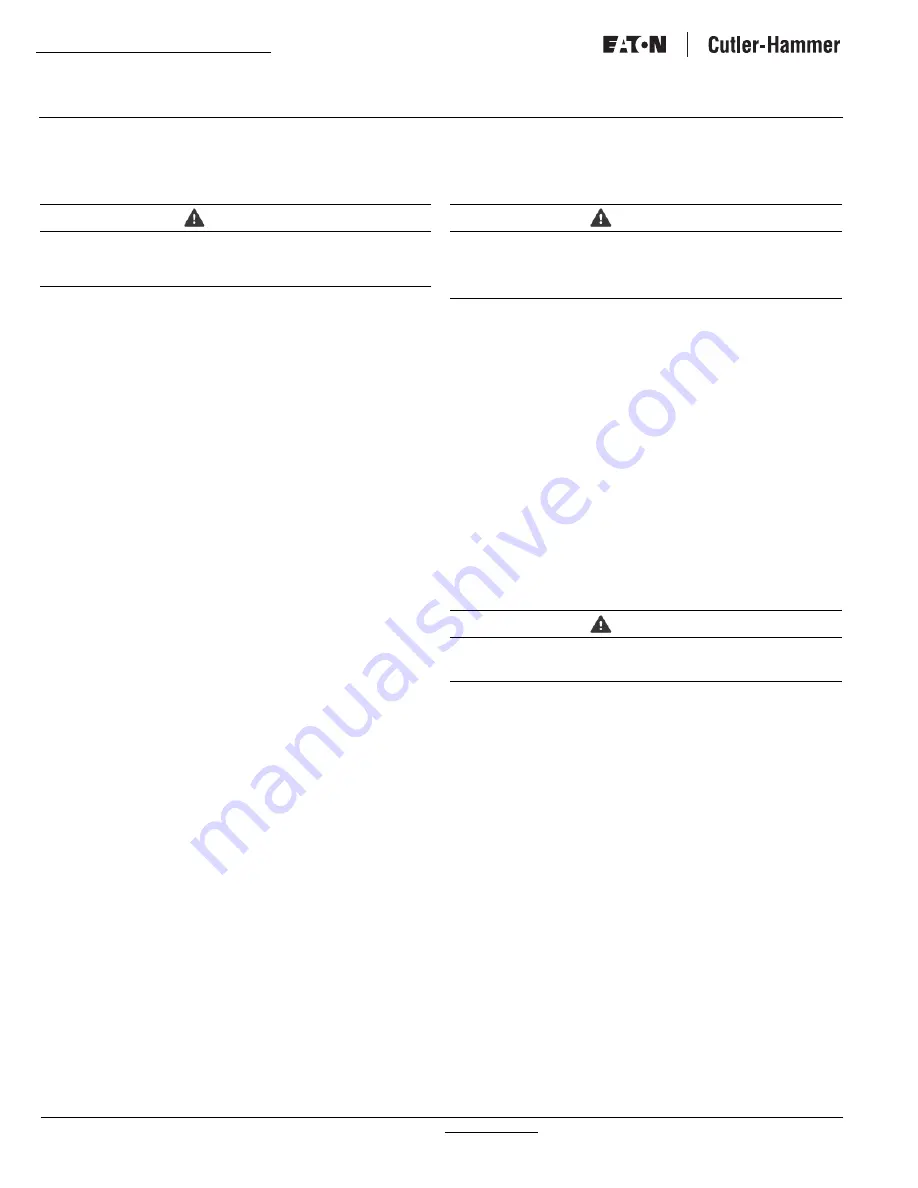
Instructional Literature
Page
146
Effective: May 2008
Instructions for the FP-6000 Protective Relay
For more information visit: www.eaton.com
IB02602004E
•
If the setpoint status is not as desired then it can be initialized
to the default by navigating to the status/control mode,
-> Control, ->Default Settings and then select “Load Default
Values.”
•
The real time clock should be set. It can be viewed under
monitor/load and page up. If it needs to be adjusted then
navigate to the Setting mode/Clock menu and adjust.
•
The history, trip, and data logs should be cleared. Navigate to
the reset mode and select the appropriate function to clear.
•
The functioning of the Contact Inputs should be verified. The
functioning of the inputs can be verified.
–
Verify that there is ~ 40 Vdc between the Contact Input
source TB 205 or 210 and open Contact Inputs 1 – 8
(TB201-204 and 206-209).
–
For applications where the initial state is to have the Con-
tact Inputs off they can be forced on. With a wire strap
attached to either TB205 or 210, touch each of the Contact
inputs 1 – 8 in order while monitoring the status. Navigate
to Status/Control - >Status -> Input Status ->Input Status
-> view Cin1 – Cin8.
–
If the default contact input configuration is used, then the
state of the 52a and 52b inputs should be confirmed. The
Breaker Open LED should be on. If not or if the Breaker
Closed LED is on while the breaker is open, a wiring error
has occurred. To make sure that the 52a and 52b contact
inputs are not in the same state, examine breaker status
flags in the status/control mode and make sure that the
“Bkr State Alarm” is off.
•
If the Zone Interlock In is connected, ensure that the input is
off. Navigate to Status/Control -> Status, -> Input Status,
-> Zone Int In: to check the state.
•
Any Trip or Alarm indications should be investigated and
eliminated before continuing.
•
Verify that the Relay output contacts are in the expected state.
An ohm meter can be used to determine if they are open =
high impedance ( > 1Meg ohm) or closed = low impedance,
(< ~ 1 ohm). In the case of the Trip Relay contacts, the open
circuit impedance is equal to the monitor circuit impedance of
~ 44K-ohm.
•
If the status is what is expected, secure all power sources and
reconnect the wiring to the contact inputs. Otherwise trouble-
shoot the FP-6000 wiring.
•
Turn the relay power source(s) back on.
•
Verify the Trip Monitor status. Navigate to Status/Control ->
Status, -> Input Status, -> Trip 1(2) Monitor: to check status.
See Section 11.2.3.4 Testing Trip Monitors.
– If there is adequate voltage across trip relay 1 or 2 and the
relay is open then the status should read “On.” A voltmeter
across the relay contacts can be used to verify if the source
and load are properly connected and the source energized.
Note: The trip monitor circuit requires at least 38 Vdc to
detect the presence of a source. ac detection operates well
below 55 Vac.
– If the relay is closed or if the control power source and or
wiring is compromised then the status should read “Off.”
•
Verify that the healthy relay is in the energized state. Removing
power to the FP-6000 power supply should disengage the
healthy relay, closing the NC contacts TB105 which should
drive an Alarm indicator.
•
Verify the functioning of the INCOM PowerNet
communications if used:
– Make sure that the FP-6000 INCOM slave address is unique
and matches the system drawings. The programmed
address can be checked under the “View Setting” mode and
modified under the “Setting” mode.
– Verify that the FP-6000 is communicating over the INCOM
network by getting confirmation of the device at the master
polling device. Visit the PowerNet or other INCOM master
client and check the monitoring displays for the particular
FP-6000. Confirm that you are viewing displays for the cor-
rect relay. Disconnecting and reconnecting the network
connector is a simple way to check this.
– The INCOM PN Transmit LED, viewed through the back
chassis TB3, will light if a response is sent by the FP-6000 to
a valid INCOM command reception.
•
Testing of Relay circuits – each relay 1 – 6 can be forced in test
mode to operate and can be opened under the reset mode and
the associated circuitry evaluated.
7.4 Voltage Checks
The voltage inputs should be checked prior to closing the
breaker. The voltage inputs should be confirmed by looking at
either the phasor voltage angles or looking at the voltage
sequential components to make sure that the phase rotation and
polarity is being measured properly.
7.5 Draw-Out Checks
The drawout design consists of an “outer chassis,” which is
mounted into the distribution gear or control panel and then
wired into the system. The operational electronic hardware is
assembled into a separable “inner chassis,” which may be
inserted or withdrawn for quick replacement. The inner chassis
makes electrical contact with the wired outer chassis by means of
engaging contacts in the back of the case. The contacts providing
the current transformer signals short upon withdrawal of the
chassis (make-before-break). The remaining contacts remain or
become open.
The outer chassis frame has provisions for a wire seal loop that
must be cleared for extraction of the inner chassis. Once this
impediment is removed, the top and bottom handles must be
depressed simultaneously to release internal latches and pull out
the inner chassis. It is suggested that an individual’s thumbs be
placed against the outer chassis frame while the fingers grasp the
front overlay bezel using the finger hold space provided by the
release depression. Hot removal and replacement of the inner
CAUTION
DO NOT ATTEMPT TO ENTER SETTING VALUES WITHOUT USING
THE APPROPRIATE SET POINT RECORD SHEET.
IMPROPER OPERATION AND/OR PERSONAL INJURY COULD
RESULT IF THIS PROCEDURE IS NOT FOLLOWED.
WARNING
IT IS VERY IMPORTANT THAT AN ALARM ANNUNCIATION IS
DRIVEN FROM THE FP-6000 HEALTHY RELAY THAT REQUIRES
IMMEDIATE ATTENTION WHEN TRIPPED, SINCE THIS MEANS THAT
THE FP-6000 IS NO LONGER PROTECTING THE CIRCUIT AND THE
SYSTEM SHOULD BE SERVICED.
WARNING
OPERATING THE CONTROL RELAYS MANUALLY SHOULD ONLY BE
DONE IF THE RESULT OF ENGAGING EACH CIRCUIT LOAD CAN BE
DONE SAFELY.