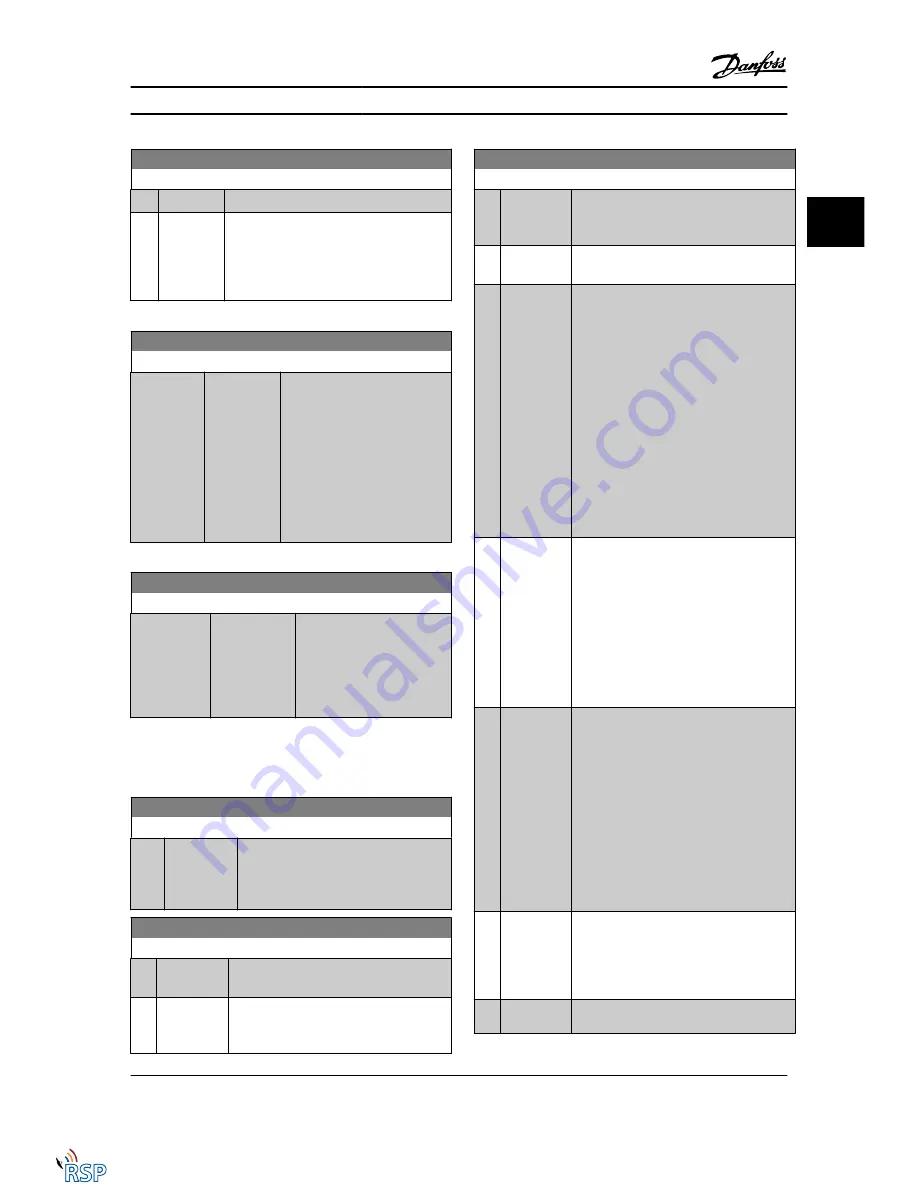
1-67 Load Type
Option:
Function:
[0]
*
Passive load For conveyers, fan and pump applications.
[1]
Active load
For hoisting applications, used in slip
compensation at low speed. When
Active Load
[1] is selected, set
1-66 Min. Current at Low
Speed
to a level which corresponds to
maximum torque.
FC 302 only.
1-68 Minimum Inertia
Range:
Function:
Application
dependent
*
[Application
dependant]
Needed for average inertia
calculation. Enter the minimum
moment of inertia of the
mechanical system.
1-68 Minimum
Inertia
and
1-69 Maximum Inertia
are used for pre-adjustment of
the Proportional Gain in the
speed control, see
30-83 Speed PID
Proportional Gain
.
FC 302 only.
This parameter cannot be adjusted while motor is running.
1-69 Maximum Inertia
Range:
Function:
Application
dependent
*
[Application
dependant]
Active in flux open-loop only.
Used to compute the
acceleration torque at low
speed. Used in the torque limit
controller.
FC 302 only.
This parameter cannot be adjusted while motor is running.
3.3.7 1-7* Start Adjustments
1-71 Start Delay
Range:
Function:
0.0 s
*
[0.0 - 25.5 s] This parameter refers to the start function
selected in
1-72 Start Function
.
Enter the time delay required before
commencing acceleration.
1-72 Start Function
Option:
Function:
Select the start function during start delay.
This parameter is linked to
1-71 Start Delay
.
[0]
DC Hold/
delay time
Energizes motor with a DC holding current
(
2-00 DC Hold Current
) during the start delay
time.
1-72 Start Function
Option:
Function:
[1]
DC Brake/
delay time
Energizes motor with a DC braking current
(
2-01 DC Brake Current
) during the start delay
time.
[2]
*
Coast/delay
time
Motor coasted during the start delay time
(inverter off).
[3]
Start speed
cw
Only possible with VVC
plus
.
Connect the function described in
1-74 Start
Speed [RPM]
and
1-76 Start Current
in the
start delay time.
Regardless of the value applied by the
reference signal, the output speed applies
the setting of the start speed in
1-74 Start
Speed [RPM]
or
1-75 Start Speed [Hz]
and the
output current corresponds to the setting of
the start current in
1-76 Start Current
. This
function is typically used in hoisting
applications without counterweight, and
especially in applications with a cone motor
where the start is clockwise, followed by
rotation in the reference direction.
[4]
Horizontal
operation
Only possible with VVC
plus
.
For obtaining the function described in
1-74 Start Speed [RPM]
and
1-76 Start Current
during the start delay time. The motor
rotates in the reference direction. If the
reference signal equals zero (0),
1-74 Start
Speed [RPM]
is ignored and the output speed
equals zero (0). The output current
corresponds to the setting of the start
current in
1-76 Start Current
.
[5]
VVC+/Flux
clockwise
for the function described in
1-74 Start Speed
[RPM]
only. The start current is calculated
automatically. This function uses the start
speed in the start delay time only. Regardless
of the value set by the reference signal, the
output speed equals the setting of the start
speed in
1-74 Start Speed [RPM]
.
Start speed/
current clockwise
[3] and
VVC
plus
/Flux clockwise
[5] are typically used in hoisting applications.
Start speed/current in reference direction
[4] is
particularly used in applications with counter-
weight and horizontal movement.
[6]
Hoist Mech.
Brake Rel
For utilizing mechanical brake control
functions,
2-24 Stop Delay
to
2-28 Gain Boost
Factor
. This parameter is only active when
1-01 Motor Control Principle
is set to [3]
Flux
w/ motor feedback (FC 302 only)
.
[7]
VVC+/Flux
counter-cw
Parameter Descriptions
FC 300 Programming Guide
MG33MD22 - VLT
®
is a registered Danfoss trademark
3-21
3
3
Remote Site Products - 1-888-532-2706 - www.remotesiteproducts.com
http://www.remotesiteproducts.com/p-20872-Danfoss-131H4490-VLT-Automation-VT-Drive-VFD-FC302-460V-25-HP.aspx