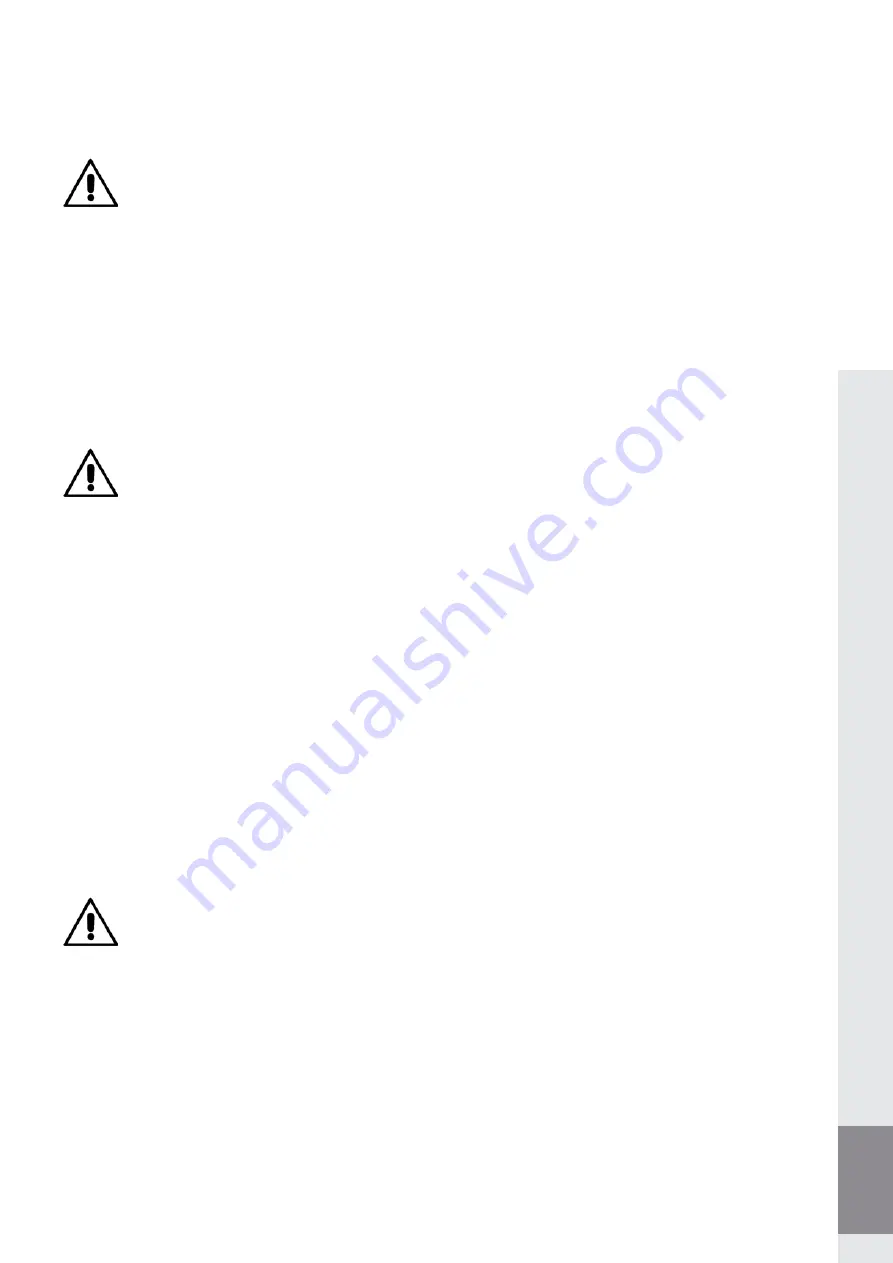
25
4.4.4 CONNECTIONS TO THE ELECTRIC POWER NETWORK
4.4.4.1 ELECTRIC MOTOR CONNECTION
Open the electric motor housing, feed the electric cable from column P1 through the cable gland, and connect the cable terminals ends as shown in the
diagram in Fig. 4.
CAUTION:
• Lift electrical panel hook-up voltage shall correspond to the voltage value indicated on the electrical board.
• The electrical board shall already be connected to a main switch manufactured and installed in compliance with the National prevailing standards.
• Connect the power cable coming out of P1 column top, to the electric power network in compliance with the prevailing national regulations.
• The system delivering power to the lift control panel shall be in compliance with the prevailing national standards.
• Min. needed power is 5 kW.
• The minimum permissible cross section of the wiring used for the power circuit is 4 mm
2
.
4.4.5 SAFETY DEVICES SETUP AND ADJUSTMENT
1) Power on the line and check that the Emergency Switch/Disconnector (19, Fig. 1) is in the ON (1) position.
2) Press the UP push-button (19, Fig. 1). If the motor does not run, check that the mechanism (1, Fig. 15) is in the correct position. If necessary, centre
the mechanism correctly and retighten the clamp (5, Fig. 13).
3) Press the UP push-button (19, Fig. 1). The carriages (5, Fig. 1) should rise. Should this not be the case, cut off power from the electric network, and
reverse the two phases on the electrical plug of the power cable.
WARNING: Do not invert motor connections. This would affect limit switch operation.
5) Press the DOWN push-button (18, Fig. 1) and bring the carriages fully down. Check that the lower limit switch (6, Fig. 13) stops the motor before the
lower edge of P1 carriage touches the floor.
6) Press the UP push-button (19, Fig. 1) and raise the carriages completely. Check that the upper limit switch (7, Fig. 13) stops the motor when the
carriages are approximately 50 mm away from the upper end panel of the column.
7) Fit the column covers (12 Fig.1).
4.4.6 ARMS INSTALLATION
1) Check that the Emergency Switch/Disconnector (17, Fig. 1) is in the ON (1) position and turn it if necessary.
2) Press the UP push-button (19, Fig. 1) and bring the carriages (4, Fig. 1) to a height of approximately 50 cm.
3) Set the arms (1 and 2, Fig. 14) near the carriages (3, Fig. 14), so that the foot guards are facing to the outside of the lift. Please note that the posi-
tions of the short and long arms mounted on the carriage of each column can be reversed, provided that the other column features the same reverse
positioning and that the foot guards are pointing to the outside of the vehicle lift.
4) Mount the arms to the carriages using the pin (5, Fig. 14), and lock it at its ends with two snap rings (6, Fig. 14). During assembly, be sure to observe
the correct positioning of the arm anti-rotation safety devices (7, Fig. 14); otherwise pull them up to facilitate arm installation.
5) Press the DOWN push-button (18, Fig. 1) until both carriages reach the minimum height. Check that both arms are free to turn without hitting the
floor. If necessary, adjust the lower column limit switch (6, Fig. 13).
6) NEVER remove the lift arm lock device (Fig. 6A) for any reason. This device is necessary for compliance with regulation 1493:2010. If the lock device
is removed, the manufacturer can no longer be held responsible for any civil or penal liability in the event of damage or injury.
WARNING
The limit switch must stop the motor before the arms touch the floor and without activating the safety limit switch. The carriage alignment microswitch
must activate when carriage misalignment exceeds 5 mm.
Summary of Contents for ERCO 3222N CEL
Page 2: ......
Page 8: ...8 1 2 DIMENSIONI INGOMBRO 2585 85 130 6 0 0 9 4 0 1250 850 1870 1915 2570 3230 2480...
Page 12: ...12 POSIZIONE OPERATORE 1 6 ZONE A RISCHIO Fig 7 700 700 5000...
Page 16: ...16 Fig 16 5 6 7 2 4 3...
Page 31: ...31 9 0 SCHEMA ELETTRICO...
Page 32: ...32...
Page 33: ...33 FU1 FU3 KM1 KM2 KM3 KM4 FU2 TC1 CB2C NT...
Page 36: ......
Page 42: ...8 1 2 OVERALL DIMENSIONS 2585 85 130 6 0 0 9 4 0 1250 850 1870 1915 2570 3230 2480...
Page 46: ...12 700 700 5000 POSITION OPERATOR 1 6 HAZARDOUS AREAS Fig 7...
Page 50: ...16 Fig 16 5 6 7 2 4 3...
Page 65: ...31 9 0 ELECTRONIC CIRCUIT BOARD DIAGRAM...
Page 66: ...32...
Page 67: ...33 FU1 FU3 KM1 KM2 KM3 KM4 FU2 TC1 CB2C NT...
Page 70: ......
Page 76: ...8 1 2 DIMENSIONS D ENCOMBREMENT 2585 85 130 6 0 0 9 4 0 1250 850 1870 1915 2570 3230 2480...
Page 80: ...12 700 700 5000 POSITION OPERATEUR 1 6 ZONES A RISQUE Fig 7...
Page 84: ...16 Fig 16 5 6 7 2 4 3...
Page 99: ...31 9 1 SCHEMA CARTE ELECTRONIQUE...
Page 100: ...32...
Page 101: ...33 FU1 FU3 KM1 KM2 KM3 KM4 FU2 TC1 CB2C NT...
Page 104: ......
Page 110: ...8 1 2 ABMESSUNGEN 2585 85 130 6 0 0 9 4 0 1250 850 1870 1915 2570 3230 2480...
Page 114: ...12 700 700 5000 POSITION BEDIENER 1 6 GEFAHRENBEREICHE Abb 7...
Page 118: ...16 Abb 16 5 6 7 2 4 3...
Page 133: ...31 9 1 SCHEMA DER PLATINE...
Page 134: ...32...
Page 135: ...33 FU1 FU3 KM1 KM2 KM3 KM4 FU2 TC1 CB2C NT...
Page 138: ......
Page 144: ...8 1 2 DIMENSIONES TOTALES 2585 85 130 6 0 0 9 4 0 1250 850 1870 1915 2570 3230 2480...
Page 148: ...12 700 700 5000 POSICI N OPERADOR 1 6 ZONAS EN RIESGO Fig 7...
Page 152: ...16 5 6 7 2 4 3 Fig 16...
Page 167: ...31 9 1 ESQUEMA TARJETA ELECTR NICA...
Page 168: ...32...
Page 169: ...33 FU1 FU3 KM1 KM2 KM3 KM4 FU2 TC1 CB2C NT...
Page 172: ......
Page 173: ......