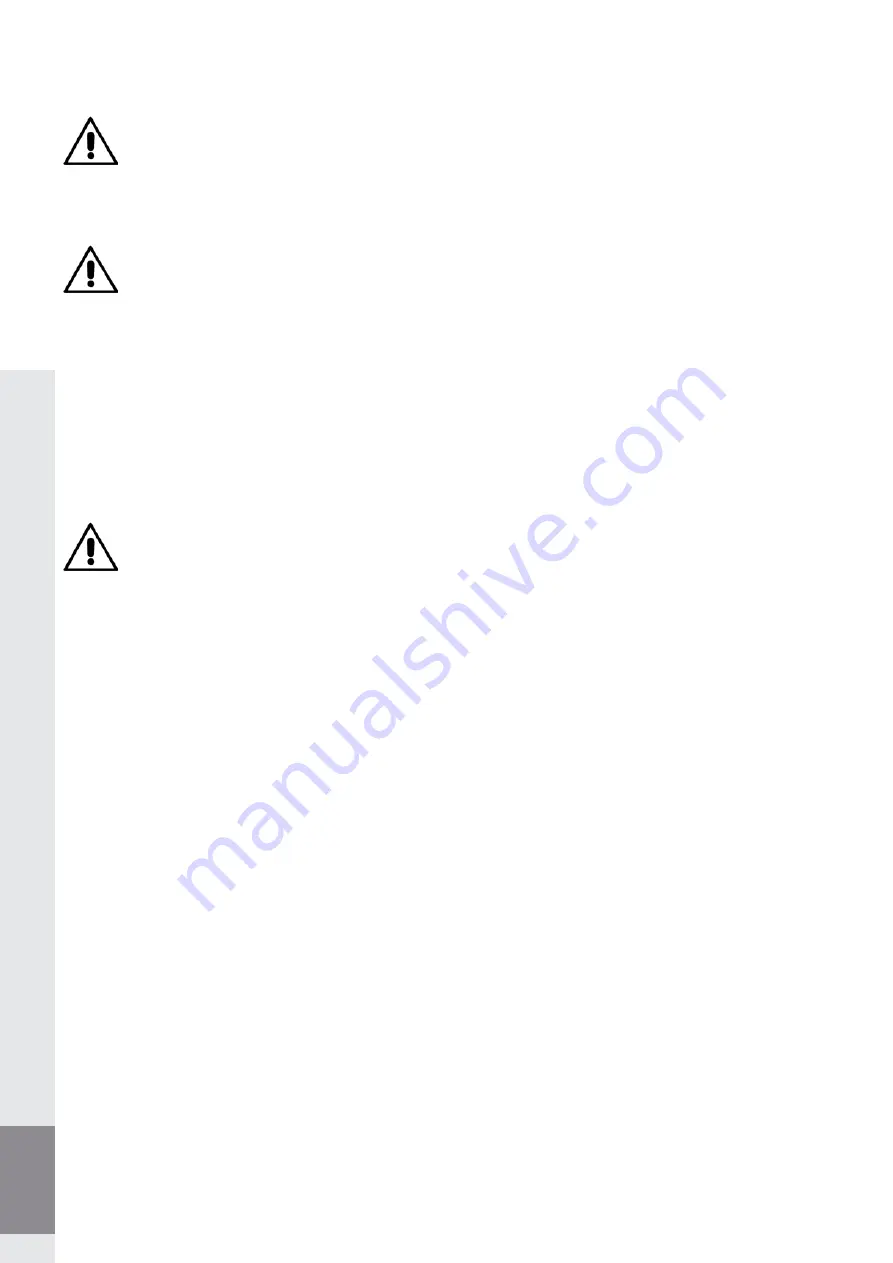
28
6.0 MAINTENANCE
Maintenance operations are listed hereinafter. A lower running cost and a longer machine life depend, among other things, on the constant execution of
these operations.
CAUTION: The listed time schedule is given for information, and relates to standard operating conditions. It is susceptible of
changes based on the type of service, level of environmental dusts, frequency of usage, etc...
In case of heavier conditions, maintenance operations shall be carried out more frequently.
6.1 SAFETY DEVICES CHECK (INSTALLER'S RESPONSIBILITY, BEFORE FIRST START-UP)
WARNING: The following operations should be carried out with unladen lift.
6.1.1 EMERGENCY SWITCH / DISCONNECTOR
1) Check that the Emergency Switch/Disconnector (17, Fig. 1) is set to 1 (ON) and turn it if necessary.
2) Press the UP/DOWN push-button.
3) At the same time, turn the Emergency Switch/Disconnector (17, Fig. 1) to 0 (OFF) and the lifting arms should stop.
6.1.2 CHECKING THE SPLIT NUTS FOR WEAR
1) Bring the carriages at mid height along the columns.
2) Remove the column casings (12, Fig. 1). Check that the distance between the upper load-bearing lead screw (1, Fig.15A) and the lower safety load-
bearing lead screw (2, Fig.15A) on both columns is between 23 and 24mm.
3) To check that the installation is correct, refer to the level of the plate (A Fig. 19). If the installation is correct, the top of the lower safety lead screw (2
Fig.19) must be at level A.
WARNING
When reference B is flush with the top face of the back-up split nut (2, Fig.15), it is necessary to replace the main split nut (1, Fig. 19).
6.1.3 MIN AND MAX HEIGHT LIMIT SWITCH CHECK
1) Press the DOWN push-button (18, Fig. 1) and bring the carriages fully down. Check that the lower limit switch (6, Fig. 13) stops the motor when the
carriages are approximately 15 mm away from the base.
2) Press the UP push-button (19, Fig. 1) and bring the carriages fully up. Check that the upper limit switch (7, Fig. 13) stops the motor when the carria-
ges are approximately 50 mm away from the top column closure.
3) If the carriages stop at any other position, adjust the position of the affected limit switch.
6.1.4 RUBBER-COATED PADS
Check their conditions. If worn-out or broken, change them.
Summary of Contents for ERCO 3222N CEL
Page 2: ......
Page 8: ...8 1 2 DIMENSIONI INGOMBRO 2585 85 130 6 0 0 9 4 0 1250 850 1870 1915 2570 3230 2480...
Page 12: ...12 POSIZIONE OPERATORE 1 6 ZONE A RISCHIO Fig 7 700 700 5000...
Page 16: ...16 Fig 16 5 6 7 2 4 3...
Page 31: ...31 9 0 SCHEMA ELETTRICO...
Page 32: ...32...
Page 33: ...33 FU1 FU3 KM1 KM2 KM3 KM4 FU2 TC1 CB2C NT...
Page 36: ......
Page 42: ...8 1 2 OVERALL DIMENSIONS 2585 85 130 6 0 0 9 4 0 1250 850 1870 1915 2570 3230 2480...
Page 46: ...12 700 700 5000 POSITION OPERATOR 1 6 HAZARDOUS AREAS Fig 7...
Page 50: ...16 Fig 16 5 6 7 2 4 3...
Page 65: ...31 9 0 ELECTRONIC CIRCUIT BOARD DIAGRAM...
Page 66: ...32...
Page 67: ...33 FU1 FU3 KM1 KM2 KM3 KM4 FU2 TC1 CB2C NT...
Page 70: ......
Page 76: ...8 1 2 DIMENSIONS D ENCOMBREMENT 2585 85 130 6 0 0 9 4 0 1250 850 1870 1915 2570 3230 2480...
Page 80: ...12 700 700 5000 POSITION OPERATEUR 1 6 ZONES A RISQUE Fig 7...
Page 84: ...16 Fig 16 5 6 7 2 4 3...
Page 99: ...31 9 1 SCHEMA CARTE ELECTRONIQUE...
Page 100: ...32...
Page 101: ...33 FU1 FU3 KM1 KM2 KM3 KM4 FU2 TC1 CB2C NT...
Page 104: ......
Page 110: ...8 1 2 ABMESSUNGEN 2585 85 130 6 0 0 9 4 0 1250 850 1870 1915 2570 3230 2480...
Page 114: ...12 700 700 5000 POSITION BEDIENER 1 6 GEFAHRENBEREICHE Abb 7...
Page 118: ...16 Abb 16 5 6 7 2 4 3...
Page 133: ...31 9 1 SCHEMA DER PLATINE...
Page 134: ...32...
Page 135: ...33 FU1 FU3 KM1 KM2 KM3 KM4 FU2 TC1 CB2C NT...
Page 138: ......
Page 144: ...8 1 2 DIMENSIONES TOTALES 2585 85 130 6 0 0 9 4 0 1250 850 1870 1915 2570 3230 2480...
Page 148: ...12 700 700 5000 POSICI N OPERADOR 1 6 ZONAS EN RIESGO Fig 7...
Page 152: ...16 5 6 7 2 4 3 Fig 16...
Page 167: ...31 9 1 ESQUEMA TARJETA ELECTR NICA...
Page 168: ...32...
Page 169: ...33 FU1 FU3 KM1 KM2 KM3 KM4 FU2 TC1 CB2C NT...
Page 172: ......
Page 173: ......