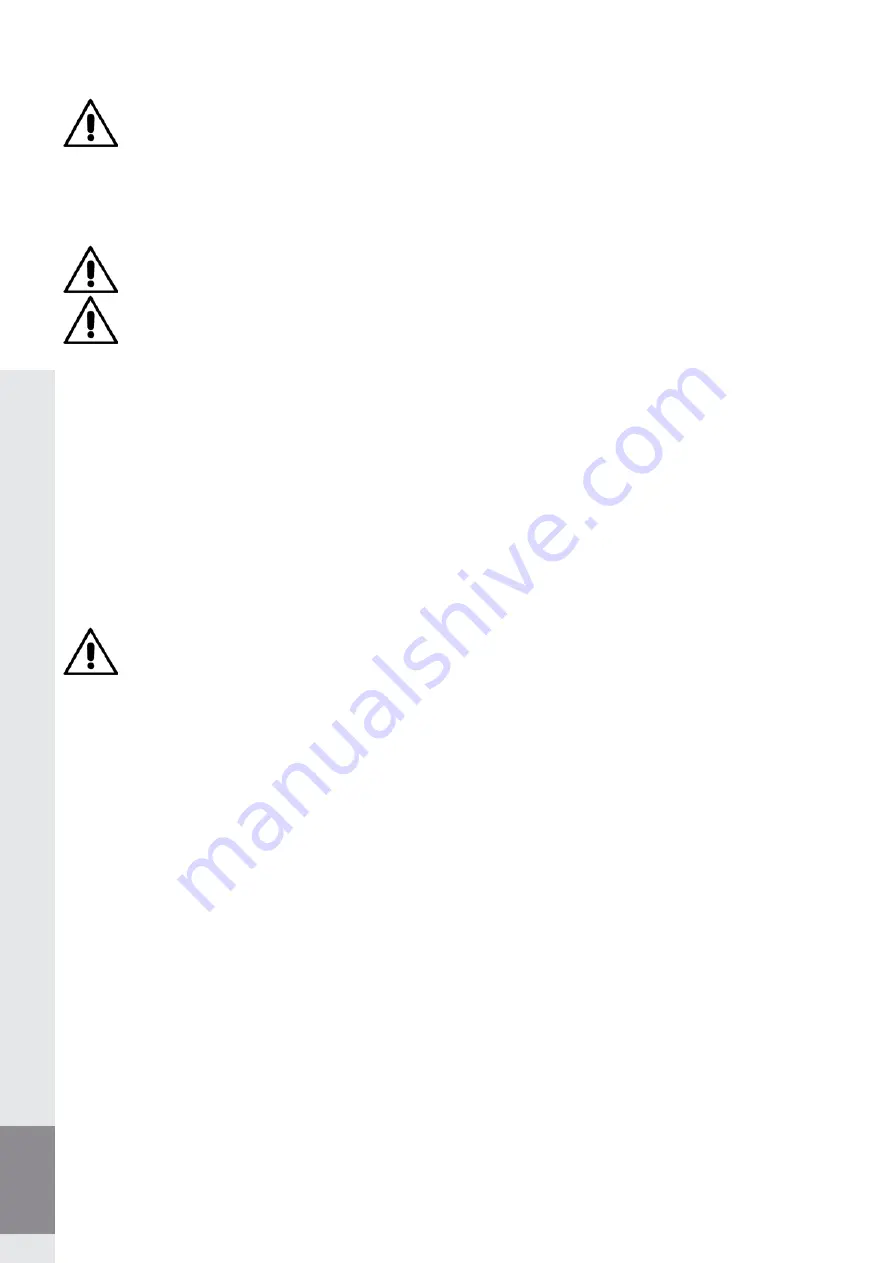
26
4.4.7 DECALS AND PICTOGRAMS APPLICATION
1) Attach the decals supplied with this manual to the lift at the positions shown in the diagram in Figure 6.
WARNING: Failure to attach the decals will make the warranty null and void and the manufacturer shall not be liable for any damage
resulting from lift operation.
In the event one or more decals of the lift are damaged, or so deteriorated as to become illegible or are lost, contact the seller with the position
number shown in the diagram 8.0 to obtain new decals. Attach the new decals at the correct positions on the lift as soon as possible.
5.0 INSTRUCTIONS FOR USE
WARNING: Do not invert motor connections. This would affect limit switch operation.
WARNING: Before carrying out any operation using the control panel, make sure that nobody is close to the lift.
5.1 CONTROL PANEL
All lift functions require the presence of an operator. Correct operator position is shown in Figure 7.
The operations to be carried out using the control panel are:
5.1.1 EMERGENCY SWITCH / DISCONNECTOR/OFF
• Turning Emergency Switch/Disconnector (17, Fig. 1) to 0 (OFF), lift will stop working completely.
• This operation shall always be carried out before accessing the working area under the lift.
• Lift functions are enabled by turning Emergency Switch/Disconnector back to 1 (ON).
Any failure or defect in one of more lift parts, or any power supply circuit failure or malfunction will not result in hazardous situations, as the LIFT features
a power disconnector for machine insulation. Up and down commands, in addition, are of the "deadman" type (hand-held). So, in case of power supply
circuit failure, neither the accidental operation nor the stop prevention, and neither the load fall nor the safety devices inefficiency will be possible if the
command has already been sent through the disconnector.
During raising or lowering, lift moving parts are thus always stopped in case of power supply circuit failure. No hazardous situations will occur upon
power supply circuit restore, as the operator will have to manually enable each single Lift movement using the hand-held control switch.
WARNING: Before accessing the working area under the lift, the emergency switch/disconnector (17, Fig. 1) shall compulsorily be
turned to 0 (OFF).
5.1.3 UP PUSH-BUTTON
• See also "5.2 LIFTING PROCEDURE".
• Check that the Emergency Switch/Disconnector (17, Fig. 1) is set to 1 (ON) and turn it if necessary.
• Press the UP push-button (19, Fig. 1) until the desired height is reached.
5.1.4 DOWN PUSH-BUTTON
• See also "5.3 LOWERING PROCEDURE"
• Press the DOWN push-button (18, Fig. 1) until the desired height is reached.
5.2 LIFTING PROCEDURE
• It is forbidden to overload the lift. The lift may be used only for lifting loads within the load capacity given in the "LOAD DISTRIBUTION" table (Fig. 3),
while compulsorily placing the vehicles on the lift in compliance with the following rules set forth in the EN 1493:1998+A1:2008 European Standard.
1) The weight of the vehicle to be lifted, represented by the sum of the two loads Q1 and Q2 (see symbols in Fig. 3), shall not exceed maximum lift
capacity (Qmax);
• (Q1+Q2) ≤ Qmax (3200 Kg)
2) Maximum load Q1 (Q1max) placed on the pair of short or long arms shall not exceed:
• 1920 Kg (Q1max ≤ 1920 Kg) as shown in Fig. 3
Summary of Contents for ERCO 3222N CEL
Page 2: ......
Page 8: ...8 1 2 DIMENSIONI INGOMBRO 2585 85 130 6 0 0 9 4 0 1250 850 1870 1915 2570 3230 2480...
Page 12: ...12 POSIZIONE OPERATORE 1 6 ZONE A RISCHIO Fig 7 700 700 5000...
Page 16: ...16 Fig 16 5 6 7 2 4 3...
Page 31: ...31 9 0 SCHEMA ELETTRICO...
Page 32: ...32...
Page 33: ...33 FU1 FU3 KM1 KM2 KM3 KM4 FU2 TC1 CB2C NT...
Page 36: ......
Page 42: ...8 1 2 OVERALL DIMENSIONS 2585 85 130 6 0 0 9 4 0 1250 850 1870 1915 2570 3230 2480...
Page 46: ...12 700 700 5000 POSITION OPERATOR 1 6 HAZARDOUS AREAS Fig 7...
Page 50: ...16 Fig 16 5 6 7 2 4 3...
Page 65: ...31 9 0 ELECTRONIC CIRCUIT BOARD DIAGRAM...
Page 66: ...32...
Page 67: ...33 FU1 FU3 KM1 KM2 KM3 KM4 FU2 TC1 CB2C NT...
Page 70: ......
Page 76: ...8 1 2 DIMENSIONS D ENCOMBREMENT 2585 85 130 6 0 0 9 4 0 1250 850 1870 1915 2570 3230 2480...
Page 80: ...12 700 700 5000 POSITION OPERATEUR 1 6 ZONES A RISQUE Fig 7...
Page 84: ...16 Fig 16 5 6 7 2 4 3...
Page 99: ...31 9 1 SCHEMA CARTE ELECTRONIQUE...
Page 100: ...32...
Page 101: ...33 FU1 FU3 KM1 KM2 KM3 KM4 FU2 TC1 CB2C NT...
Page 104: ......
Page 110: ...8 1 2 ABMESSUNGEN 2585 85 130 6 0 0 9 4 0 1250 850 1870 1915 2570 3230 2480...
Page 114: ...12 700 700 5000 POSITION BEDIENER 1 6 GEFAHRENBEREICHE Abb 7...
Page 118: ...16 Abb 16 5 6 7 2 4 3...
Page 133: ...31 9 1 SCHEMA DER PLATINE...
Page 134: ...32...
Page 135: ...33 FU1 FU3 KM1 KM2 KM3 KM4 FU2 TC1 CB2C NT...
Page 138: ......
Page 144: ...8 1 2 DIMENSIONES TOTALES 2585 85 130 6 0 0 9 4 0 1250 850 1870 1915 2570 3230 2480...
Page 148: ...12 700 700 5000 POSICI N OPERADOR 1 6 ZONAS EN RIESGO Fig 7...
Page 152: ...16 5 6 7 2 4 3 Fig 16...
Page 167: ...31 9 1 ESQUEMA TARJETA ELECTR NICA...
Page 168: ...32...
Page 169: ...33 FU1 FU3 KM1 KM2 KM3 KM4 FU2 TC1 CB2C NT...
Page 172: ......
Page 173: ......