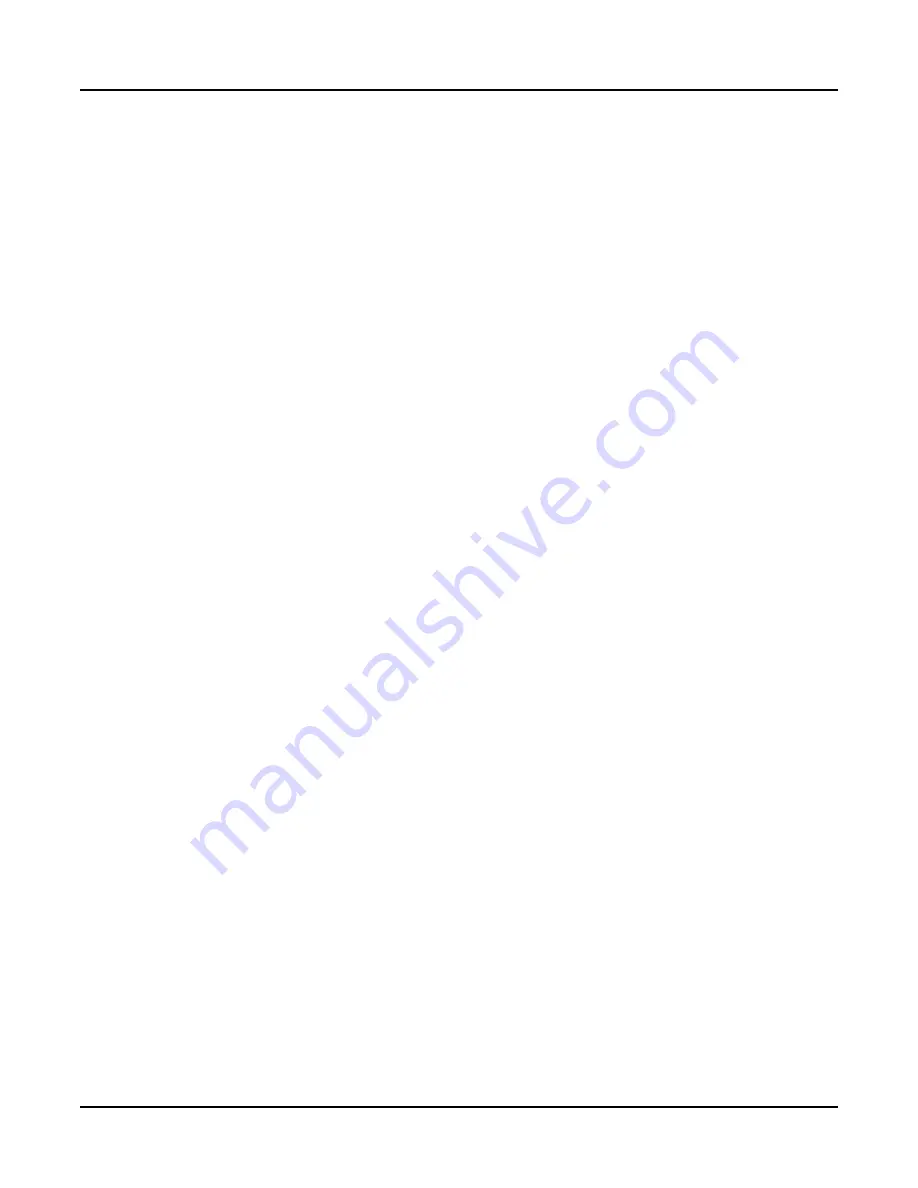
Chapter 5 — Starting and Operating Instructions
5-4
Part No. 750-184
Note: The settings of all the above controls may require some
readjustment after the boiler is started and running for a short
period. The scale settings on the controls are relatively
accurate, but are principally for use as guides. Final
adjustment should be based on and agree with the reading of
the steam pressure gauge or the water temperature
thermometer.
Inspect the
Low-water Cutoff
and
Pump Control
as well as the
Auxiliary Low-water Cutoff
(if equipped with this optional device).
Check for freedom of float movement. Float movement can be
verified by observing the level of water in the gauge glass when the
water supply has been cut off either by the stopping of the feed
pump or by the closing of a valve, and the restarting of the pump or
opening of the valve when water is drained from the pressure vessel.
The importance of proper functioning of low-water controls cannot
be over-emphasized. Be sure that the control and the piping is level.
The settings of controls relating to fuel, either oil or gas, are covered
in subsequent sections.
In the event the boiler is equipped with optional control devices not
listed here, be certain to ascertain that their settings are correct. If
additional information is required, see your local Cleaver-Brooks
authorized representative or contact Cleaver-Brooks.
On initial start-up or whenever the boiler is placed into operation
from a “cold” start, the
Manual-automatic Selector Switch
should
be set at “manual” and the
Manual Flame Control
set at “close.”
After the boiler is in operation and thoroughly warmed, the selector
switch should be turned to “automatic,” so that the burner firing
rate may be controlled by the
Modulating Control
in accordance
with load demands.
Close all power entrance switches (supplied by others).
C. GAS PILOT
The gas pilot should be checked for satisfactory performance prior
to initial firing. Follow the pilot flame adjustment instructions given
in Chapter 6.
On initial starting attempts, several efforts might be required to fully
bleed the pilot line. While checking pilot adjustment, observe
whether the pilot flame is extinguished promptly when the burner
switch is opened. A lingering flame indicates a leaking gas pilot
valve, which is a condition requiring correction before proceeding.
D. ATOMIZING AIR
The supply and pressure of the atomizing air on an oil-fired burner
should be checked. Before starting, inspect the oil pump lube oil
level. Add oil if necessary to bring the level to the mid-point or
slightly higher of the sight glass. Use SAE 20 detergent oil of a grade
mentioned in Chapter 8 and fill in accordance with instructions
given there.
Summary of Contents for CB Ohio Special 100 HP
Page 2: ...ii ...
Page 8: ...viii ...
Page 42: ...Chapter 2 Burner Operation and Control 2 22 Part No 750 184 ...
Page 116: ...Chapter 6 Adjustment Procedures 6 28 Part No 750 184 ...
Page 126: ...Chapter 8 Inspection and Maintenance 8 6 Part No 750 184 ...
Page 153: ...Chapter 9 Parts Part No 750 184 9 3 Insulated Front Head Model CB LE ...
Page 154: ...Chapter 9 Parts 9 4 Part No 750 184 Insulated Front Head Interior Model CB LE ...
Page 155: ...Chapter 9 Parts Part No 750 184 9 5 Insulated Inner Door Model CB OS ...
Page 156: ...Chapter 9 Parts 9 6 Part No 750 184 Insulated Rear Head CB LE ...
Page 157: ...Chapter 9 Parts Part No 750 184 9 7 Insulated Rear Head CB LE ...
Page 158: ...Chapter 9 Parts 9 8 Part No 750 184 Insulated Rear Head CB OS ...
Page 159: ...Chapter 9 Parts Part No 750 184 9 9 Dry Oven Model CB LE ...
Page 161: ...Chapter 9 Parts Part No 750 184 9 11 Motor Impeller Model CB LE ...
Page 162: ...Chapter 9 Parts 9 12 Part No 750 184 Front Head Linkage ...
Page 170: ...Chapter 9 Parts 9 20 Part No 750 184 Control Cabinet Hawk ICS ...
Page 171: ...Chapter 9 Parts Part No 750 184 9 21 Control Panel Standard ...
Page 172: ...Chapter 9 Parts 9 22 Part No 750 184 Entrance Box ...
Page 173: ...Chapter 9 Parts Part No 750 184 9 23 Front Head Electrical CB LE ...
Page 174: ...Chapter 9 Parts 9 24 Part No 750 184 Front Head Electrical CB LE ...
Page 175: ...Chapter 9 Parts Part No 750 184 9 25 Front Head Electrical CB OS ...
Page 176: ...Chapter 9 Parts 9 26 Part No 750 184 Front Head Electrical CB OS ...
Page 179: ...Chapter 9 Parts Part No 750 184 9 29 Heavy Oil Piping 60 Steam CB LE ...
Page 180: ...Chapter 9 Parts 9 30 Part No 750 184 Heavy Oil Piping 60 Steam CB LE SEE TABLE NEXT PAGE ...
Page 181: ...Chapter 9 Parts Part No 750 184 9 31 Common Oil Parts Heavy Oil ...
Page 182: ...Chapter 9 Parts 9 32 Part No 750 184 Side Mounted Air Compressor Piping ...
Page 183: ...Chapter 9 Parts Part No 750 184 9 33 Air Compressor Piping CB OS ...
Page 185: ...Chapter 9 Parts Part No 750 184 9 35 Light Oil Piping ...
Page 186: ...Chapter 9 Parts 9 36 Part No 750 184 Light Oil Air Piping Front Head ...
Page 187: ...Chapter 9 Parts Part No 750 184 9 37 Light Oil Air Piping Front Head PAGE 9 31 ...
Page 191: ...Chapter 9 Parts Part No 750 184 9 41 Gas Train 125 150 HP ...
Page 193: ...Chapter 9 Parts Part No 750 184 9 43 Gas Train 200 HP ...
Page 195: ...Chapter 9 Parts Part No 750 184 9 45 Steam Pressure Controls ...
Page 196: ...Chapter 9 Parts 9 46 Part No 750 184 Hot Water Temperature Controls ...
Page 197: ...Chapter 9 Parts Part No 750 184 9 47 Water Column ...
Page 198: ...Chapter 9 Parts 9 48 Part No 750 184 Water Column ...
Page 199: ...Chapter 9 Parts Part No 750 184 9 49 Fireside Gaskets CB LE ...
Page 200: ...Chapter 9 Parts 9 50 Part No 750 184 Fireside Gaskets CB OS ...