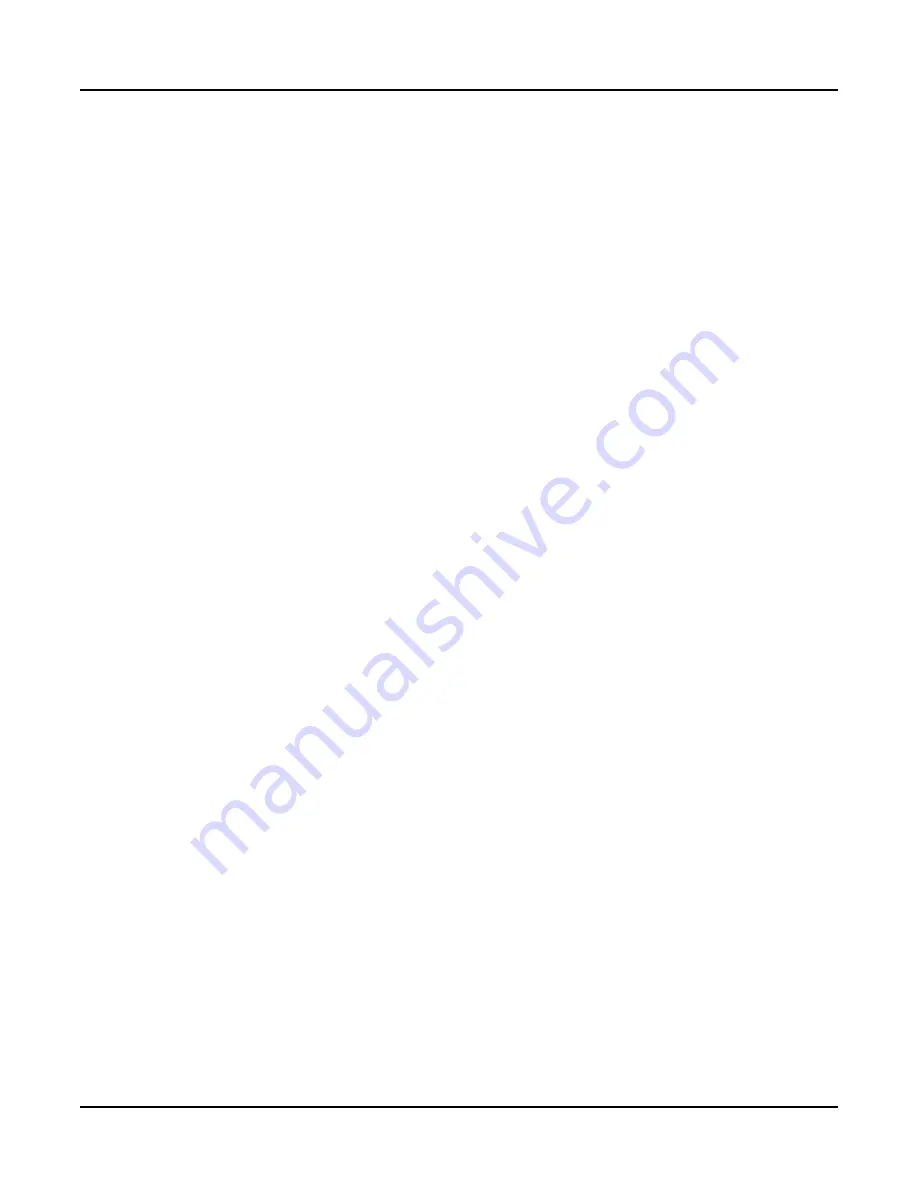
Chapter 3 — Waterside Care and Requirements
3-12
Part No. 750-184
F. WASHING OUT
1. HOT WATER BOILER
In theory, a hot water system and boiler that has been initially
cleaned, filled with raw water (and water treated), and with no
make-up water added, will require no further cleaning or treatment.
However, since the system (new or old) can allow entrance of air
and unnoticed or undetected leakage of water, introductions of raw
water make-up or air may lead to pitting, corrosion and formation
of sludge, sediment, scale, etc., on the pressure vessel waterside.
If the operator is absolutely certain that the system is tight, then an
annual waterside inspection may be sufficient. However, if there is
any doubt, the pressure vessel waterside should be inspected no
later than three months after initially placing the boiler into
operation, and periodically thereafter as indicated by conditions
observed during inspections.
2. STEAM BOILER
No later than three months after initially placing the boiler into
operation and starting service, and thereafter as conditions warrant,
the pressure vessel should be drained after being properly cooled to
near ambient temperature. Handhole covers should be removed and
waterside surfaces should be inspected for corrosion, pitting, or
formation of deposits.
Flushing of Pressure Vessel Interior
Upon completion of the inspection, the pressure vessel interior
should be flushed out, as required, with a high pressure hose. If
deposits are not fully removed by flushing, a consultation may be
required with your local Cleaver-Brooks authorized representative.
In extreme cases, it may be necessary to resort to acid cleaning.
Professional advice is recommended if acid cleaning is required.
The inspections will indicate the effectiveness of the feedwater
treatment. The effectiveness of treatment, the water conditions, and
the amount of fresh water make-up required are all factors to be
considered in establishing frequency of future pressure vessel
w a s h o u t s . C o n t a c t y o u r l o c a l C l e a v e r- b r o o k s a u t h o r i z e d
representative for more information.
G. BLOWDOWN STEAM BOILER
Boiler water blowdown is the removal of some of the concentrated
water from the pressure vessel and its replacement with feedwater
so that the lowering of the concentration of solids in the boiler water
occurs.
Solids are brought in by the feedwater even though the water is
treated prior to use through external processes that are designed to
remove unwanted substances which contribute to scale and deposit
formations. However, none of the processes can remove all
Summary of Contents for CB Ohio Special 100 HP
Page 2: ...ii ...
Page 8: ...viii ...
Page 42: ...Chapter 2 Burner Operation and Control 2 22 Part No 750 184 ...
Page 116: ...Chapter 6 Adjustment Procedures 6 28 Part No 750 184 ...
Page 126: ...Chapter 8 Inspection and Maintenance 8 6 Part No 750 184 ...
Page 153: ...Chapter 9 Parts Part No 750 184 9 3 Insulated Front Head Model CB LE ...
Page 154: ...Chapter 9 Parts 9 4 Part No 750 184 Insulated Front Head Interior Model CB LE ...
Page 155: ...Chapter 9 Parts Part No 750 184 9 5 Insulated Inner Door Model CB OS ...
Page 156: ...Chapter 9 Parts 9 6 Part No 750 184 Insulated Rear Head CB LE ...
Page 157: ...Chapter 9 Parts Part No 750 184 9 7 Insulated Rear Head CB LE ...
Page 158: ...Chapter 9 Parts 9 8 Part No 750 184 Insulated Rear Head CB OS ...
Page 159: ...Chapter 9 Parts Part No 750 184 9 9 Dry Oven Model CB LE ...
Page 161: ...Chapter 9 Parts Part No 750 184 9 11 Motor Impeller Model CB LE ...
Page 162: ...Chapter 9 Parts 9 12 Part No 750 184 Front Head Linkage ...
Page 170: ...Chapter 9 Parts 9 20 Part No 750 184 Control Cabinet Hawk ICS ...
Page 171: ...Chapter 9 Parts Part No 750 184 9 21 Control Panel Standard ...
Page 172: ...Chapter 9 Parts 9 22 Part No 750 184 Entrance Box ...
Page 173: ...Chapter 9 Parts Part No 750 184 9 23 Front Head Electrical CB LE ...
Page 174: ...Chapter 9 Parts 9 24 Part No 750 184 Front Head Electrical CB LE ...
Page 175: ...Chapter 9 Parts Part No 750 184 9 25 Front Head Electrical CB OS ...
Page 176: ...Chapter 9 Parts 9 26 Part No 750 184 Front Head Electrical CB OS ...
Page 179: ...Chapter 9 Parts Part No 750 184 9 29 Heavy Oil Piping 60 Steam CB LE ...
Page 180: ...Chapter 9 Parts 9 30 Part No 750 184 Heavy Oil Piping 60 Steam CB LE SEE TABLE NEXT PAGE ...
Page 181: ...Chapter 9 Parts Part No 750 184 9 31 Common Oil Parts Heavy Oil ...
Page 182: ...Chapter 9 Parts 9 32 Part No 750 184 Side Mounted Air Compressor Piping ...
Page 183: ...Chapter 9 Parts Part No 750 184 9 33 Air Compressor Piping CB OS ...
Page 185: ...Chapter 9 Parts Part No 750 184 9 35 Light Oil Piping ...
Page 186: ...Chapter 9 Parts 9 36 Part No 750 184 Light Oil Air Piping Front Head ...
Page 187: ...Chapter 9 Parts Part No 750 184 9 37 Light Oil Air Piping Front Head PAGE 9 31 ...
Page 191: ...Chapter 9 Parts Part No 750 184 9 41 Gas Train 125 150 HP ...
Page 193: ...Chapter 9 Parts Part No 750 184 9 43 Gas Train 200 HP ...
Page 195: ...Chapter 9 Parts Part No 750 184 9 45 Steam Pressure Controls ...
Page 196: ...Chapter 9 Parts 9 46 Part No 750 184 Hot Water Temperature Controls ...
Page 197: ...Chapter 9 Parts Part No 750 184 9 47 Water Column ...
Page 198: ...Chapter 9 Parts 9 48 Part No 750 184 Water Column ...
Page 199: ...Chapter 9 Parts Part No 750 184 9 49 Fireside Gaskets CB LE ...
Page 200: ...Chapter 9 Parts 9 50 Part No 750 184 Fireside Gaskets CB OS ...