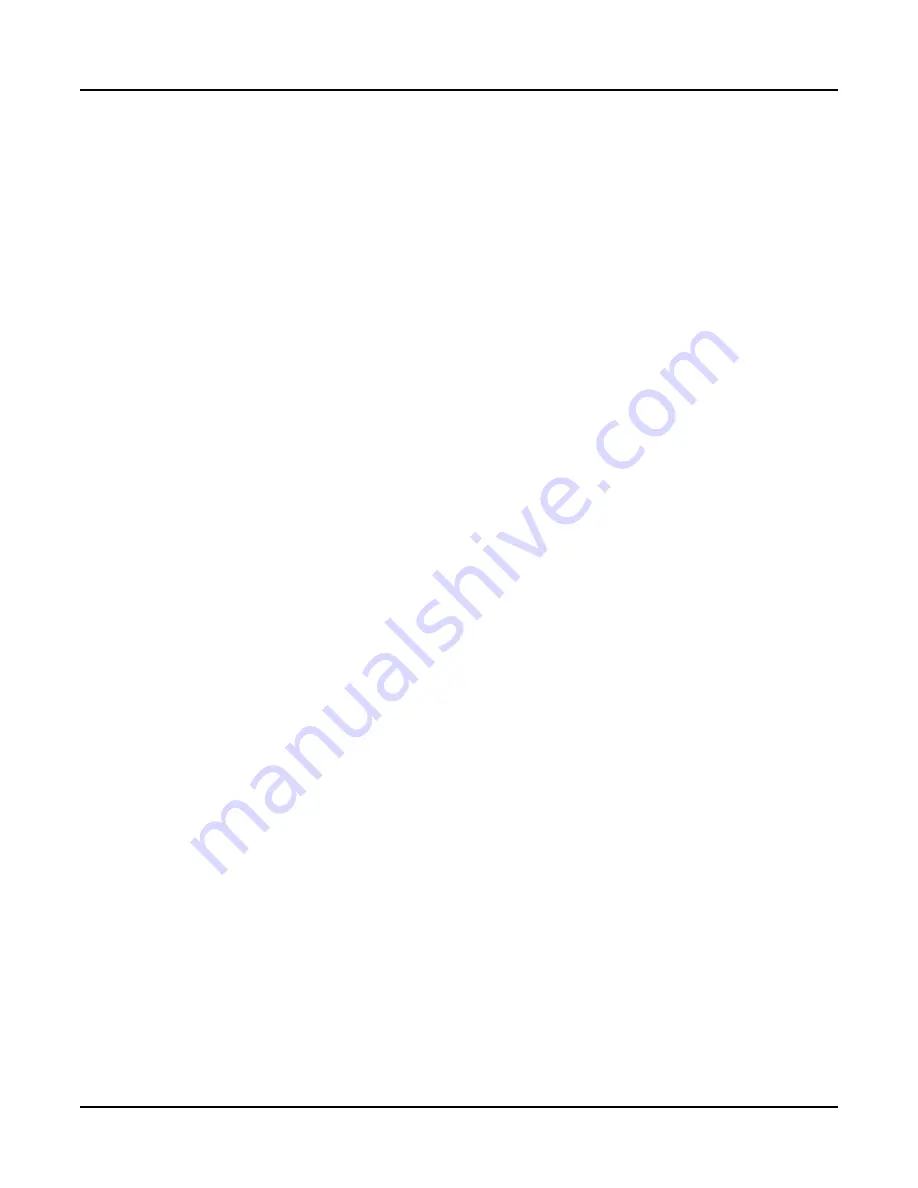
Chapter 3 — Waterside Care and Requirements
3-14
Part No. 750-184
purpose of skimming surface sediment, oil or other impurities from
the surface of the pressure vessel water.
A controlled-orifice valve is used to allow a continual, yet controlled,
flow of concentrated water.
Periodic adjustments are made to the valve setting to increase or
decrease the amount of blowdown in accordance with the test
analysis.
The flow control valve and piping are generally provided by others.
All piping must be to a safe point of discharge.
Frequency of Manual Blowdown
When continuous blowdown is utilized, manual blowdown is
primarily used to remove suspended solids or sludge. The
continuous blowdown removes sediment and oil from the surface of
the water along with a prescribed amount of dissolved solids.
When surface or continuous blowdown is not utilized, manual
blowdown is used to control the dissolved or suspended solids in
addition to the sludge.
In practice, the valve(s) of the bottom blowdown are opened
periodically in accordance with an operating schedule and/or
chemical control tests. From the standpoint of control, economy and
results, frequent short blows are preferred to infrequent lengthy
blows. The length and frequency of the blwdown is particularly
important when the suspended solids content of the water is high.
With the use of frequent short blows a more uniform concentration
of the pressure vessel water is maintained.
In cases where the feedwater is exceptionally pure, or where there
is a high percentage of return condensate, blowdown may be
employed less frequently since less sludge accumulates in the
pressure vessel. When dissolved and/or suspended solids approach
or exceed predetermined limits, manual blowdown to lower the
concentrations is required.
It is generally recommended that a steam boiler be blown down at
least once in every eight-hour period, but frequency may vary
depending upon water and operating conditions. The blowdown
amounts and schedule should be recommended by your local
Cleaver-Brooks authorized representative.
A hot water boiler does not normally include openings for surface
blowdown and bottom blowdown since blowdowns are seldom
practiced. The need remains to be alert to system water losses and
corresponding amount of raw water make-up. A water meter is
recommended for water make-up lines.
Manual Blowdown Procedure
Blowdown is most effective at a point in time when the generation
of steam is at the lowest rate and feedwater input is also low, thus
providing a minimum dilution of the boiler water with low
concentration feedwater.
Summary of Contents for CB Ohio Special 100 HP
Page 2: ...ii ...
Page 8: ...viii ...
Page 42: ...Chapter 2 Burner Operation and Control 2 22 Part No 750 184 ...
Page 116: ...Chapter 6 Adjustment Procedures 6 28 Part No 750 184 ...
Page 126: ...Chapter 8 Inspection and Maintenance 8 6 Part No 750 184 ...
Page 153: ...Chapter 9 Parts Part No 750 184 9 3 Insulated Front Head Model CB LE ...
Page 154: ...Chapter 9 Parts 9 4 Part No 750 184 Insulated Front Head Interior Model CB LE ...
Page 155: ...Chapter 9 Parts Part No 750 184 9 5 Insulated Inner Door Model CB OS ...
Page 156: ...Chapter 9 Parts 9 6 Part No 750 184 Insulated Rear Head CB LE ...
Page 157: ...Chapter 9 Parts Part No 750 184 9 7 Insulated Rear Head CB LE ...
Page 158: ...Chapter 9 Parts 9 8 Part No 750 184 Insulated Rear Head CB OS ...
Page 159: ...Chapter 9 Parts Part No 750 184 9 9 Dry Oven Model CB LE ...
Page 161: ...Chapter 9 Parts Part No 750 184 9 11 Motor Impeller Model CB LE ...
Page 162: ...Chapter 9 Parts 9 12 Part No 750 184 Front Head Linkage ...
Page 170: ...Chapter 9 Parts 9 20 Part No 750 184 Control Cabinet Hawk ICS ...
Page 171: ...Chapter 9 Parts Part No 750 184 9 21 Control Panel Standard ...
Page 172: ...Chapter 9 Parts 9 22 Part No 750 184 Entrance Box ...
Page 173: ...Chapter 9 Parts Part No 750 184 9 23 Front Head Electrical CB LE ...
Page 174: ...Chapter 9 Parts 9 24 Part No 750 184 Front Head Electrical CB LE ...
Page 175: ...Chapter 9 Parts Part No 750 184 9 25 Front Head Electrical CB OS ...
Page 176: ...Chapter 9 Parts 9 26 Part No 750 184 Front Head Electrical CB OS ...
Page 179: ...Chapter 9 Parts Part No 750 184 9 29 Heavy Oil Piping 60 Steam CB LE ...
Page 180: ...Chapter 9 Parts 9 30 Part No 750 184 Heavy Oil Piping 60 Steam CB LE SEE TABLE NEXT PAGE ...
Page 181: ...Chapter 9 Parts Part No 750 184 9 31 Common Oil Parts Heavy Oil ...
Page 182: ...Chapter 9 Parts 9 32 Part No 750 184 Side Mounted Air Compressor Piping ...
Page 183: ...Chapter 9 Parts Part No 750 184 9 33 Air Compressor Piping CB OS ...
Page 185: ...Chapter 9 Parts Part No 750 184 9 35 Light Oil Piping ...
Page 186: ...Chapter 9 Parts 9 36 Part No 750 184 Light Oil Air Piping Front Head ...
Page 187: ...Chapter 9 Parts Part No 750 184 9 37 Light Oil Air Piping Front Head PAGE 9 31 ...
Page 191: ...Chapter 9 Parts Part No 750 184 9 41 Gas Train 125 150 HP ...
Page 193: ...Chapter 9 Parts Part No 750 184 9 43 Gas Train 200 HP ...
Page 195: ...Chapter 9 Parts Part No 750 184 9 45 Steam Pressure Controls ...
Page 196: ...Chapter 9 Parts 9 46 Part No 750 184 Hot Water Temperature Controls ...
Page 197: ...Chapter 9 Parts Part No 750 184 9 47 Water Column ...
Page 198: ...Chapter 9 Parts 9 48 Part No 750 184 Water Column ...
Page 199: ...Chapter 9 Parts Part No 750 184 9 49 Fireside Gaskets CB LE ...
Page 200: ...Chapter 9 Parts 9 50 Part No 750 184 Fireside Gaskets CB OS ...