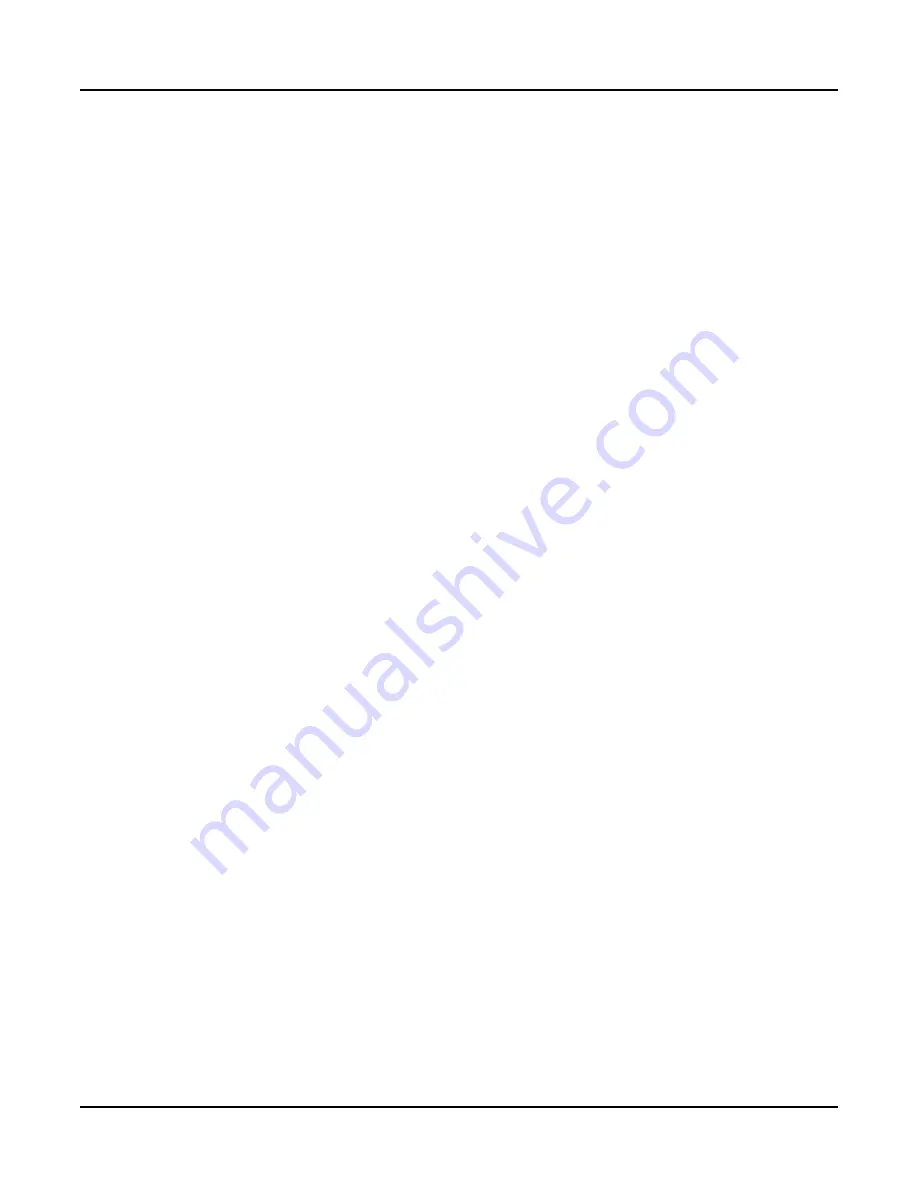
Chapter 8 — Inspection and Maintenance
8-10
Part No. 750-184
that might be present. If there are cracks, replace the electrode since they
can cause grounding of the ignition voltage. Since carbon is an electrical
conductor, it is necessary to keep the insulating portion of electrode(s) wiped
clean if any carbon is present. Ammonia will aid in removing carbon or soot.
Check ignition cables for cracks in the insulation. Also see that all
connections between the transformer and the electrodes are tight.
H. GAS BURNER MAINTENANCE
The gas burner components should be inspected for evidence of damage due
to improperly adjusted combustion. Combustion adjustments should be
checked monthly. See Section Q in Chapter 6.
Check periodically for a proper seal between the end of the burner housing
and boiler refractory. Any deterioration of the seal should be corrected, as an
improper or poor seal allows air leaks, which can cause overheating or
burning of the burner housing.
Whenever the burner is removed, the diffuser, gas housing and gas spuds
(HTB model only) should be checked for any deterioration. Verify that the
diffuser skirt conforms to the bore of the burner housing so as to minimize
the amount of combustion air which bypasses the diffuser. If the burner is a
high turndown burner (HTB) model, check to see that the diffuser is properly
located in reference to the gas spuds. There should be 1/4” between the
edge of the diffuser fins and the gas spuds when the burner is installed.
Check to see that the diffuser fins do not interfere with the gas ports or gas
spuds in the burner housing. See Section V in Chapter 6 for more
information.
Check the electrode setting for any cracks that might be present on the
porcelain insulator. Replace the electrode if cracking is evident, since
cracking can cause grounding of the ignition voltage. Inspect the tip of the
electrode for signs of pitting, combustion deposits and wear, and dress as
required with a fine file.
Periodically remove the access plug from the gas pilot aspirator and clean
out any accumulated lint or other foreign material.
Check the ignition cables for cracks in the insulation. Verify that all
connections between the transformer and the electrode are tight.
I. MOTORIZED GAS VALVE
The motorized gas valve (Hydramotor) operating mechanism is completely
immersed in oil and little maintenance is required because of the sealed
design. However, proper operation should be checked on a routine periodic
basis.
Keep outer parts of the valve clean, especially the stem between the operator
and the valve. A nicked, scored or otherwise damaged valve stem can cause
leakage. Do not remove dust covers if installed.
The packing gland is of the O-ring type. If oil is noticed around the operator
base or if leakage occurs, repair by replacing any leaking O-rings and refilling
the actuator with oil.
If the actuator is sluggish or fails to operate, even after the oil level is
checked, replace the entire operator portion.
Summary of Contents for CB Ohio Special 100 HP
Page 2: ...ii ...
Page 8: ...viii ...
Page 42: ...Chapter 2 Burner Operation and Control 2 22 Part No 750 184 ...
Page 116: ...Chapter 6 Adjustment Procedures 6 28 Part No 750 184 ...
Page 126: ...Chapter 8 Inspection and Maintenance 8 6 Part No 750 184 ...
Page 153: ...Chapter 9 Parts Part No 750 184 9 3 Insulated Front Head Model CB LE ...
Page 154: ...Chapter 9 Parts 9 4 Part No 750 184 Insulated Front Head Interior Model CB LE ...
Page 155: ...Chapter 9 Parts Part No 750 184 9 5 Insulated Inner Door Model CB OS ...
Page 156: ...Chapter 9 Parts 9 6 Part No 750 184 Insulated Rear Head CB LE ...
Page 157: ...Chapter 9 Parts Part No 750 184 9 7 Insulated Rear Head CB LE ...
Page 158: ...Chapter 9 Parts 9 8 Part No 750 184 Insulated Rear Head CB OS ...
Page 159: ...Chapter 9 Parts Part No 750 184 9 9 Dry Oven Model CB LE ...
Page 161: ...Chapter 9 Parts Part No 750 184 9 11 Motor Impeller Model CB LE ...
Page 162: ...Chapter 9 Parts 9 12 Part No 750 184 Front Head Linkage ...
Page 170: ...Chapter 9 Parts 9 20 Part No 750 184 Control Cabinet Hawk ICS ...
Page 171: ...Chapter 9 Parts Part No 750 184 9 21 Control Panel Standard ...
Page 172: ...Chapter 9 Parts 9 22 Part No 750 184 Entrance Box ...
Page 173: ...Chapter 9 Parts Part No 750 184 9 23 Front Head Electrical CB LE ...
Page 174: ...Chapter 9 Parts 9 24 Part No 750 184 Front Head Electrical CB LE ...
Page 175: ...Chapter 9 Parts Part No 750 184 9 25 Front Head Electrical CB OS ...
Page 176: ...Chapter 9 Parts 9 26 Part No 750 184 Front Head Electrical CB OS ...
Page 179: ...Chapter 9 Parts Part No 750 184 9 29 Heavy Oil Piping 60 Steam CB LE ...
Page 180: ...Chapter 9 Parts 9 30 Part No 750 184 Heavy Oil Piping 60 Steam CB LE SEE TABLE NEXT PAGE ...
Page 181: ...Chapter 9 Parts Part No 750 184 9 31 Common Oil Parts Heavy Oil ...
Page 182: ...Chapter 9 Parts 9 32 Part No 750 184 Side Mounted Air Compressor Piping ...
Page 183: ...Chapter 9 Parts Part No 750 184 9 33 Air Compressor Piping CB OS ...
Page 185: ...Chapter 9 Parts Part No 750 184 9 35 Light Oil Piping ...
Page 186: ...Chapter 9 Parts 9 36 Part No 750 184 Light Oil Air Piping Front Head ...
Page 187: ...Chapter 9 Parts Part No 750 184 9 37 Light Oil Air Piping Front Head PAGE 9 31 ...
Page 191: ...Chapter 9 Parts Part No 750 184 9 41 Gas Train 125 150 HP ...
Page 193: ...Chapter 9 Parts Part No 750 184 9 43 Gas Train 200 HP ...
Page 195: ...Chapter 9 Parts Part No 750 184 9 45 Steam Pressure Controls ...
Page 196: ...Chapter 9 Parts 9 46 Part No 750 184 Hot Water Temperature Controls ...
Page 197: ...Chapter 9 Parts Part No 750 184 9 47 Water Column ...
Page 198: ...Chapter 9 Parts 9 48 Part No 750 184 Water Column ...
Page 199: ...Chapter 9 Parts Part No 750 184 9 49 Fireside Gaskets CB LE ...
Page 200: ...Chapter 9 Parts 9 50 Part No 750 184 Fireside Gaskets CB OS ...