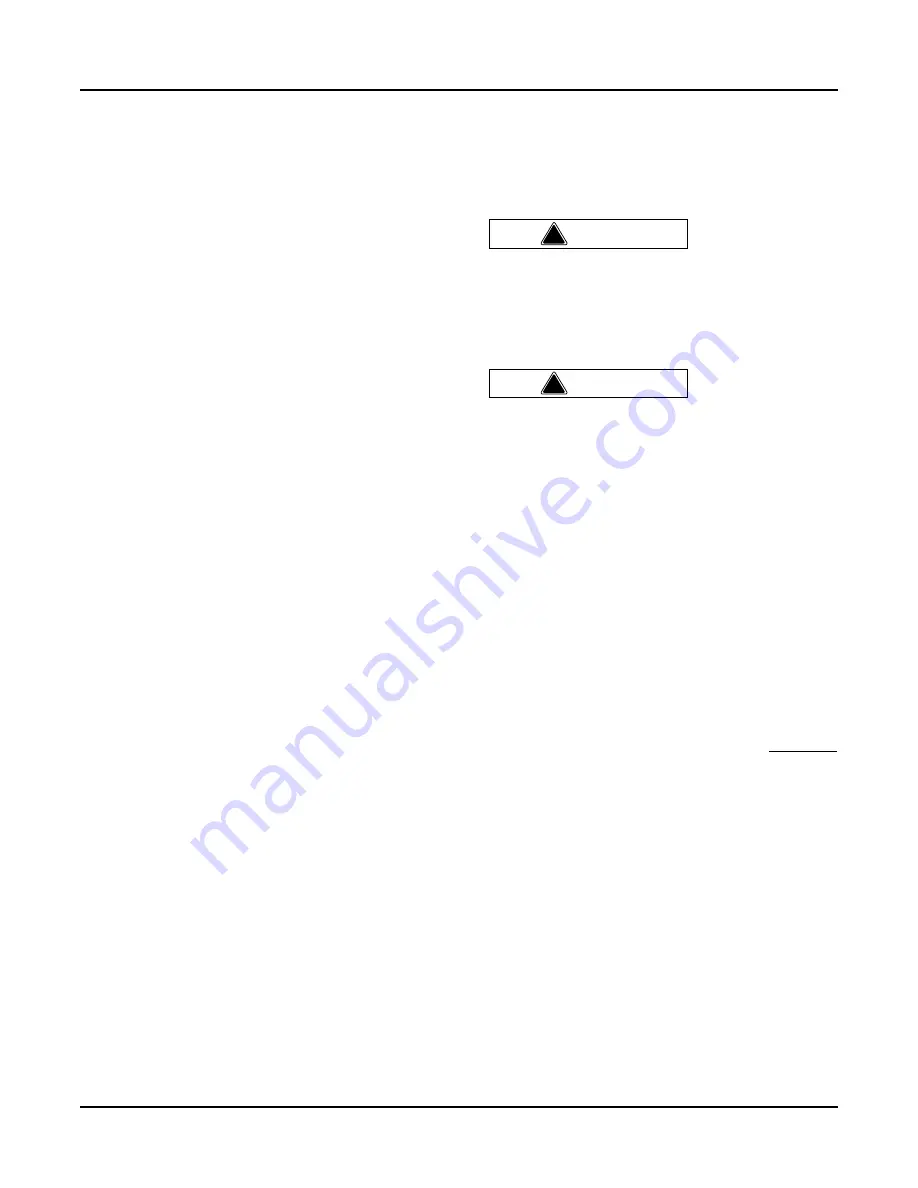
Chapter 5 — Starting and Operating Instructions
5-14
Part No. 750-184
On ignition failure, the flame failure light will glow and the blower
will purge the boiler of unburned fuel vapors before stopping. After
ignition failure, wait a few moments before re-setting the lockout
switch.
!
Warning
Do not re-light the pilot or attempt to start the main burner, either
oil or gas, if the combustion chamber is hot and/or if gas or oil vapor
combustion gases are present in the furnace or flue passages.
Failure to follow these instructions could result in serious personal
injury or death
!
Warning
The burner and control system is designed to provide a “pre-purge”
period of fan operation prior to establishing ignition spark and pilot
flame. Do not attempt to alter the system or take any action that
might circumvent the “pre-purge” feature. Failure to follow these
instructions could result in serious personal injury or death
After main flame ignition, the burner should be set on manual
control at its low fire setting (that is, with manual flame control at
“close”) until the boiler is properly warmed. Close the steam header.
In the case of a steam boiler, CLOSE THE TEST VALVE when steam
begins to appear.
A hot water boiler must have a continuous flow of system water
through the vessel during the warm-up period. The entire water
content of the system and boiler must be warmed prior to increasing
fuel input.
If the flame at low fire provides insufficient heat to reach normal
operating pressure or temperature after 30 minutes, gradually
increase the firing rate by turning the
Manual Flame Control
in one
point increments to no higher than the third cam screw. Operate at
the increased fuel input rate for a period of time until an increase is
noted in pressure or temperature.
After the boiler is thoroughly warmed, turn the manual flame control
to high fire. At this point a combustion analysis should be made,
with instruments, and fuel flow regulated as required. Refer to the
adjustment procedures in Chapter 6. After making the high-fire
adjustment, manually decrease the firing rate, stopping at each cam
screw to analyze combustion gases, and adjust as required.
To properly perform the testing and adjusting, it is necessary that
the burner be allowed to fire at a maximum rate long enough to
achieve desired results.
Operating
- Normal operation of the burner should be with the
switch in the automatic position and under the direction of the
modulating control. The manual position is provided for initial
Summary of Contents for CB Ohio Special 100 HP
Page 2: ...ii ...
Page 8: ...viii ...
Page 42: ...Chapter 2 Burner Operation and Control 2 22 Part No 750 184 ...
Page 116: ...Chapter 6 Adjustment Procedures 6 28 Part No 750 184 ...
Page 126: ...Chapter 8 Inspection and Maintenance 8 6 Part No 750 184 ...
Page 153: ...Chapter 9 Parts Part No 750 184 9 3 Insulated Front Head Model CB LE ...
Page 154: ...Chapter 9 Parts 9 4 Part No 750 184 Insulated Front Head Interior Model CB LE ...
Page 155: ...Chapter 9 Parts Part No 750 184 9 5 Insulated Inner Door Model CB OS ...
Page 156: ...Chapter 9 Parts 9 6 Part No 750 184 Insulated Rear Head CB LE ...
Page 157: ...Chapter 9 Parts Part No 750 184 9 7 Insulated Rear Head CB LE ...
Page 158: ...Chapter 9 Parts 9 8 Part No 750 184 Insulated Rear Head CB OS ...
Page 159: ...Chapter 9 Parts Part No 750 184 9 9 Dry Oven Model CB LE ...
Page 161: ...Chapter 9 Parts Part No 750 184 9 11 Motor Impeller Model CB LE ...
Page 162: ...Chapter 9 Parts 9 12 Part No 750 184 Front Head Linkage ...
Page 170: ...Chapter 9 Parts 9 20 Part No 750 184 Control Cabinet Hawk ICS ...
Page 171: ...Chapter 9 Parts Part No 750 184 9 21 Control Panel Standard ...
Page 172: ...Chapter 9 Parts 9 22 Part No 750 184 Entrance Box ...
Page 173: ...Chapter 9 Parts Part No 750 184 9 23 Front Head Electrical CB LE ...
Page 174: ...Chapter 9 Parts 9 24 Part No 750 184 Front Head Electrical CB LE ...
Page 175: ...Chapter 9 Parts Part No 750 184 9 25 Front Head Electrical CB OS ...
Page 176: ...Chapter 9 Parts 9 26 Part No 750 184 Front Head Electrical CB OS ...
Page 179: ...Chapter 9 Parts Part No 750 184 9 29 Heavy Oil Piping 60 Steam CB LE ...
Page 180: ...Chapter 9 Parts 9 30 Part No 750 184 Heavy Oil Piping 60 Steam CB LE SEE TABLE NEXT PAGE ...
Page 181: ...Chapter 9 Parts Part No 750 184 9 31 Common Oil Parts Heavy Oil ...
Page 182: ...Chapter 9 Parts 9 32 Part No 750 184 Side Mounted Air Compressor Piping ...
Page 183: ...Chapter 9 Parts Part No 750 184 9 33 Air Compressor Piping CB OS ...
Page 185: ...Chapter 9 Parts Part No 750 184 9 35 Light Oil Piping ...
Page 186: ...Chapter 9 Parts 9 36 Part No 750 184 Light Oil Air Piping Front Head ...
Page 187: ...Chapter 9 Parts Part No 750 184 9 37 Light Oil Air Piping Front Head PAGE 9 31 ...
Page 191: ...Chapter 9 Parts Part No 750 184 9 41 Gas Train 125 150 HP ...
Page 193: ...Chapter 9 Parts Part No 750 184 9 43 Gas Train 200 HP ...
Page 195: ...Chapter 9 Parts Part No 750 184 9 45 Steam Pressure Controls ...
Page 196: ...Chapter 9 Parts 9 46 Part No 750 184 Hot Water Temperature Controls ...
Page 197: ...Chapter 9 Parts Part No 750 184 9 47 Water Column ...
Page 198: ...Chapter 9 Parts 9 48 Part No 750 184 Water Column ...
Page 199: ...Chapter 9 Parts Part No 750 184 9 49 Fireside Gaskets CB LE ...
Page 200: ...Chapter 9 Parts 9 50 Part No 750 184 Fireside Gaskets CB OS ...