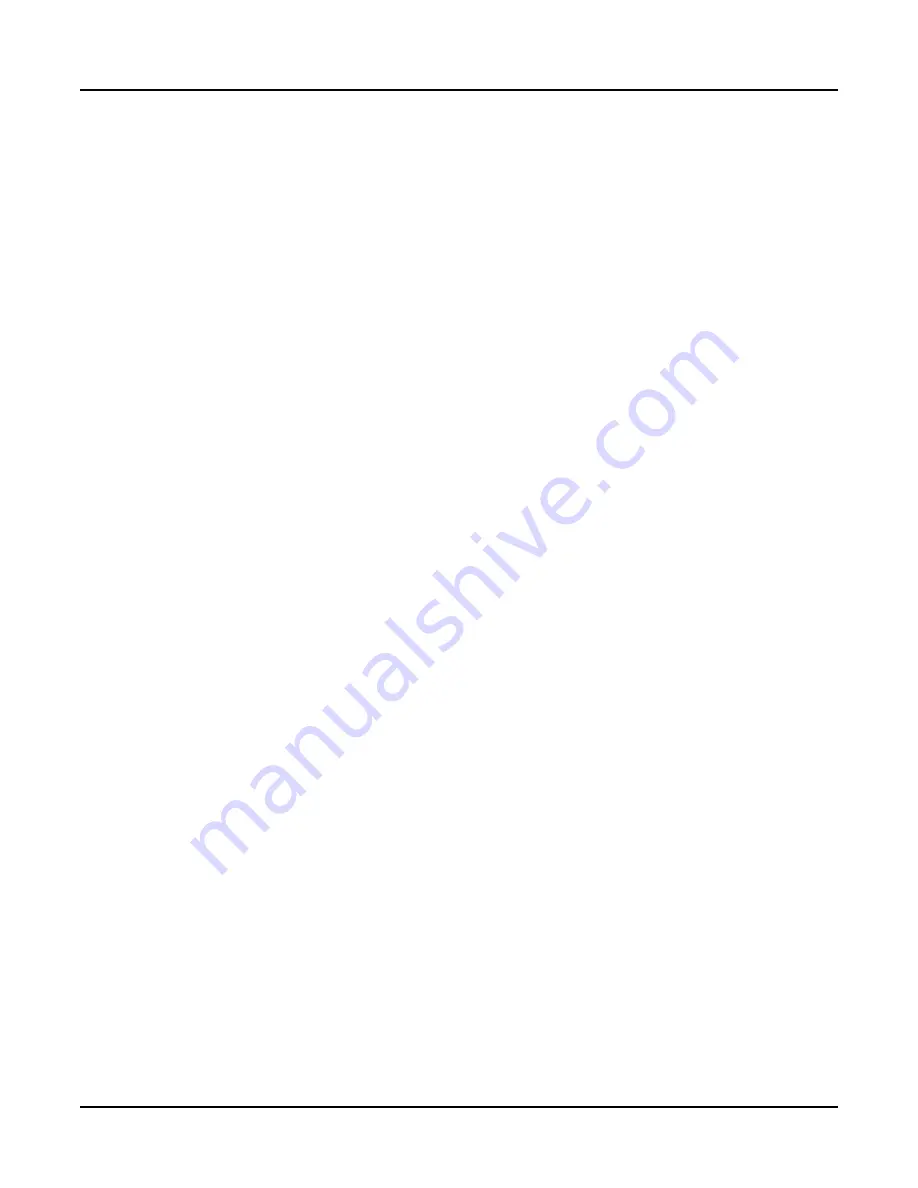
Chapter 5 — Starting and Operating Instructions
Part No. 750-184
5-5
Check the oil level of the air intake strainer. When operating a
standard CB boiler, make certain that the V-belt which drives the air
pump is in place and has proper tension.
To verify air flow and pressure, place the burner
Run/test Switch
on
the program relay to the test position. If the burner is a combination
fuel burner, be sure that the gas/oil selector switch is set to “oil.”
Turn the
Burner Switch
on. The burner will cycle to the low fire pre-
purge position and stop there.
Observe the reading on the air pressure gauge. With no oil flow, the
pressure should be a minimum of 7 psi.
If there is no pressure, determine the cause and correct it before
proceeding. Check for obstructions in the air inlet line, incorrect
rotation, or a loose oil nozzle or other leaks. If the pressure is much
higher without any oil flow, check for obstruction in the discharge
line or at the oil nozzle. If there is no obstruction, restrict the air flow
by adjusting the air intake valve screw.
The air pressure will increase when an oil flow exists. At low firing
rate, the air pressure may rise to 12 psi or more.
Note: The air pressure should not exceed 35 psi at high fire. Greater
air pressure causes excessive wear of the air pump, increases
lube oil usage, and can overload the motor, thus causing
damage to the equipment.
Note: Abnormally high pressure indicated on the nozzle air pressure
gauge is an indication that the burner nozzle has become
clogged. In the event of clogging, check the nozzle and clean
as necessary.
After air flow has been verified, turn the burner switch off and return
the run/test switch to the run position.
E. FIRING PREPARATIONS FOR NO. 2 OIL (SERIES
100-200)
Prior to initial firing, oil flow and pressure should be established and
verified. Atomizing air pressure should also be established as
outlined in
Section D.
See section H for IFGR setting procedures.
If the burner is a combination fuel model, be certain that the
Main
Gas Shutoff Cock
is closed and set the
Gas/oil Selector Switch
to
“oil.” Insert the burner drawer gun into its most forward position
and latch it in place.
Oil Flow
- Open all valves in the oil suction and oil return lines.
If the oil supply tank is located above the level of the pump and flow
to the pump is by gravity, then it will usually be necessary to vent
the suction line to allow oil to fill the line. Venting the suction line
can generally be accomplished by cracking a union fitting, or by
opening the cap of the oil strainer using care to prevent spillage of
oil. Tighten the fitting or the cap as soon as oil flow appears.
Summary of Contents for CB Ohio Special 100 HP
Page 2: ...ii ...
Page 8: ...viii ...
Page 42: ...Chapter 2 Burner Operation and Control 2 22 Part No 750 184 ...
Page 116: ...Chapter 6 Adjustment Procedures 6 28 Part No 750 184 ...
Page 126: ...Chapter 8 Inspection and Maintenance 8 6 Part No 750 184 ...
Page 153: ...Chapter 9 Parts Part No 750 184 9 3 Insulated Front Head Model CB LE ...
Page 154: ...Chapter 9 Parts 9 4 Part No 750 184 Insulated Front Head Interior Model CB LE ...
Page 155: ...Chapter 9 Parts Part No 750 184 9 5 Insulated Inner Door Model CB OS ...
Page 156: ...Chapter 9 Parts 9 6 Part No 750 184 Insulated Rear Head CB LE ...
Page 157: ...Chapter 9 Parts Part No 750 184 9 7 Insulated Rear Head CB LE ...
Page 158: ...Chapter 9 Parts 9 8 Part No 750 184 Insulated Rear Head CB OS ...
Page 159: ...Chapter 9 Parts Part No 750 184 9 9 Dry Oven Model CB LE ...
Page 161: ...Chapter 9 Parts Part No 750 184 9 11 Motor Impeller Model CB LE ...
Page 162: ...Chapter 9 Parts 9 12 Part No 750 184 Front Head Linkage ...
Page 170: ...Chapter 9 Parts 9 20 Part No 750 184 Control Cabinet Hawk ICS ...
Page 171: ...Chapter 9 Parts Part No 750 184 9 21 Control Panel Standard ...
Page 172: ...Chapter 9 Parts 9 22 Part No 750 184 Entrance Box ...
Page 173: ...Chapter 9 Parts Part No 750 184 9 23 Front Head Electrical CB LE ...
Page 174: ...Chapter 9 Parts 9 24 Part No 750 184 Front Head Electrical CB LE ...
Page 175: ...Chapter 9 Parts Part No 750 184 9 25 Front Head Electrical CB OS ...
Page 176: ...Chapter 9 Parts 9 26 Part No 750 184 Front Head Electrical CB OS ...
Page 179: ...Chapter 9 Parts Part No 750 184 9 29 Heavy Oil Piping 60 Steam CB LE ...
Page 180: ...Chapter 9 Parts 9 30 Part No 750 184 Heavy Oil Piping 60 Steam CB LE SEE TABLE NEXT PAGE ...
Page 181: ...Chapter 9 Parts Part No 750 184 9 31 Common Oil Parts Heavy Oil ...
Page 182: ...Chapter 9 Parts 9 32 Part No 750 184 Side Mounted Air Compressor Piping ...
Page 183: ...Chapter 9 Parts Part No 750 184 9 33 Air Compressor Piping CB OS ...
Page 185: ...Chapter 9 Parts Part No 750 184 9 35 Light Oil Piping ...
Page 186: ...Chapter 9 Parts 9 36 Part No 750 184 Light Oil Air Piping Front Head ...
Page 187: ...Chapter 9 Parts Part No 750 184 9 37 Light Oil Air Piping Front Head PAGE 9 31 ...
Page 191: ...Chapter 9 Parts Part No 750 184 9 41 Gas Train 125 150 HP ...
Page 193: ...Chapter 9 Parts Part No 750 184 9 43 Gas Train 200 HP ...
Page 195: ...Chapter 9 Parts Part No 750 184 9 45 Steam Pressure Controls ...
Page 196: ...Chapter 9 Parts 9 46 Part No 750 184 Hot Water Temperature Controls ...
Page 197: ...Chapter 9 Parts Part No 750 184 9 47 Water Column ...
Page 198: ...Chapter 9 Parts 9 48 Part No 750 184 Water Column ...
Page 199: ...Chapter 9 Parts Part No 750 184 9 49 Fireside Gaskets CB LE ...
Page 200: ...Chapter 9 Parts 9 50 Part No 750 184 Fireside Gaskets CB OS ...