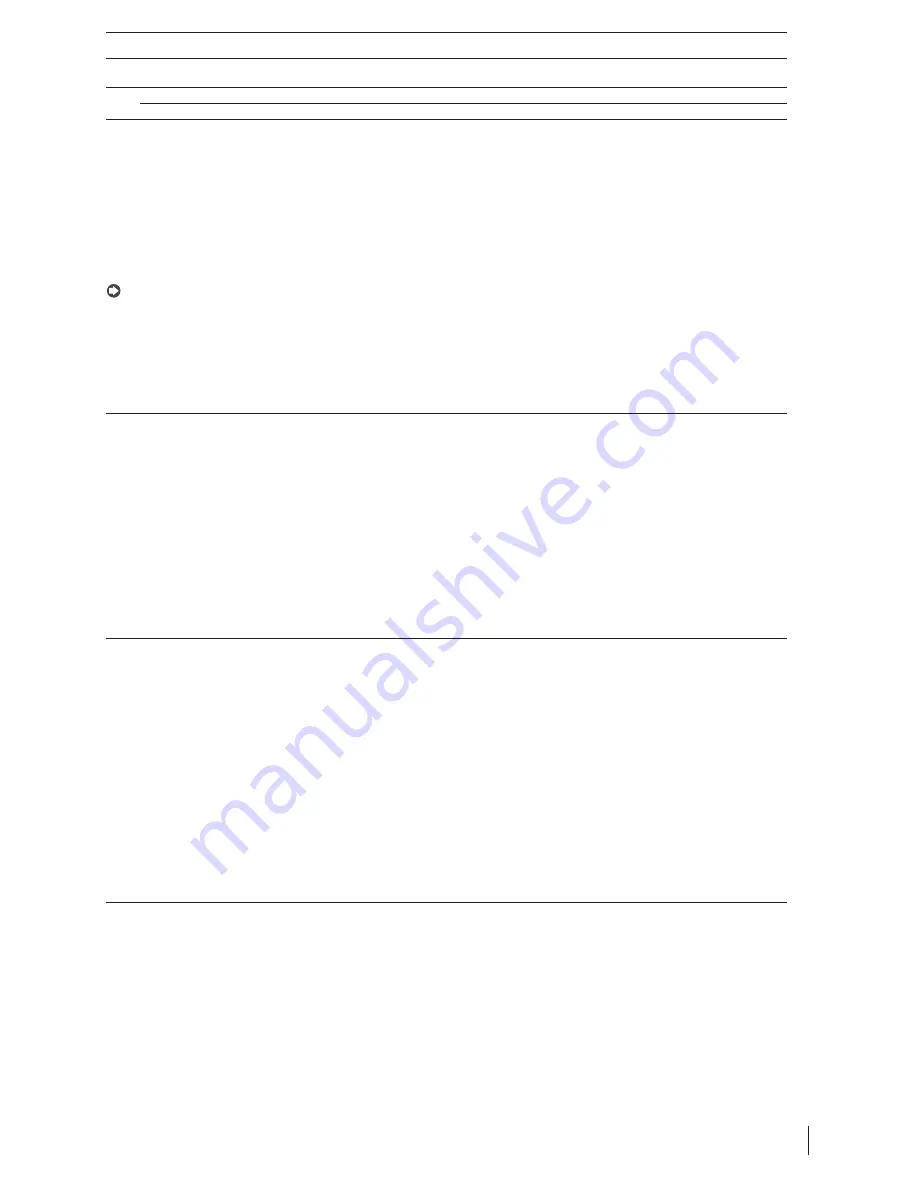
55
Functions
k.air +030220981 rel. 1.2 - 01.12.2020
R
if
D
escription
D
ev
Min
Max
UoM
D
ir
Modbus
BAC
net
U
N
IT
Ac18 Regulation type (0: Supply only; 1:Return only; 2: Room only;
3: Supply; 4: Room + Supply; 5: Disabled)
5
0
5
-
R/W HR1307
PIV2815
Ac32 Humidifi cation/Dehumidifi cation: Control probe
0
0
2
-
R/W HR1318
PIV2826
Humidifi cation/Dehumidifi cation: Control type
0
0
1
-
R/W HR1319
PIV2827
Tab. 9.h
Auxiliary control functions:
1. humidity:
the humidity request is sent by the controller to a humidifi er via the 0-10 V output or via the Modbus serial port (CA-
REL humiSonic, Carel Humifog);
2. dehumidifi cation:
the controller sends the request, either directly or via the dew point calculation, to the main coil.
3. air
quality:
the controller modulates the fan speed and/or the opening of the fresh air damper;
4. pressure:
the controller modulates the fan speed, based on the pressure set point.
5. air
fl ow-rate:
the controller modulates the fan speed, based on the supply set point.
Note:
see the chapter on “Fan speed control”.
9.5
P
I
D
control
The controller features three types of control:
• Cascaded PID;
Cascade control is applied to the main temperature controller with multiple control points (room + supply or supply)
or air quality controller.
• Sequential PID;
Sequential control features a single control point and activation of multiple actuators, so as to give priority to energy savings.
This is used for supply temperature control, for example.
• Incremental PID;
This features a single control point and a single actuator. It is used for independent control functions, such as air fl ow control.
9.5.1
C
ascaded
P
I
D
The cascaded PID is used for the following control functions:
• Main temperature control with supply probe
• Main temperature control with room probe
• Air quality control with fans and pressure or fl ow control.
This type of control is aimed at keeping two control points linked together. The output of the PID controller on the fi rst control
point calculates a set point that is used as the reference by the PID that controls the second set point. The fi rst control point, and
its corresponding PID, is considered the main control function, while the second is used to limit the operating range inside pre-
defi ned limits. For example, with supply temperature control, the main control is based on the return temperature, and
any deviation from the return set point causes the supply temperature set point to be lowered in cooling mode and increased
in heating mode, always within a predefi ned range. In other words, so as reach the required return temperature, the unit will
modulate the supply temperature within an optimal range.
9.5.2
S
equential
P
I
D
The k.Air controller has diff erent functions and devices that can act alone or in a coordinated way to ensure the best indoor
comfort conditions. Each of these devices may either be present or absent, or enabled or disabled on the unit; therefore, de-
pending on the situation, it will have a diff erent impact on energy consumption during operation. Each device is activated only
after the previous device reaches full load. Considering then that each device will make a diff erent contribution in terms of
deliverable capacity and response time, each individual actuator can be calibrated with its own gain and integral time.
Below is a functional diagram of sequential PID control: with a single set point and a series of PID parameters for each device, the
request is divided into a series of sub- requests, corresponding to the number of devices.
Summary of Contents for k.Air
Page 2: ......
Page 4: ......
Page 6: ......
Page 188: ...188 k air 030220981 rel 1 2 01 12 2020 Note...
Page 189: ...189 k air 030220981 rel 1 2 01 12 2020 Note...
Page 190: ...190 k air 030220981 rel 1 2 01 12 2020 Note...
Page 191: ......