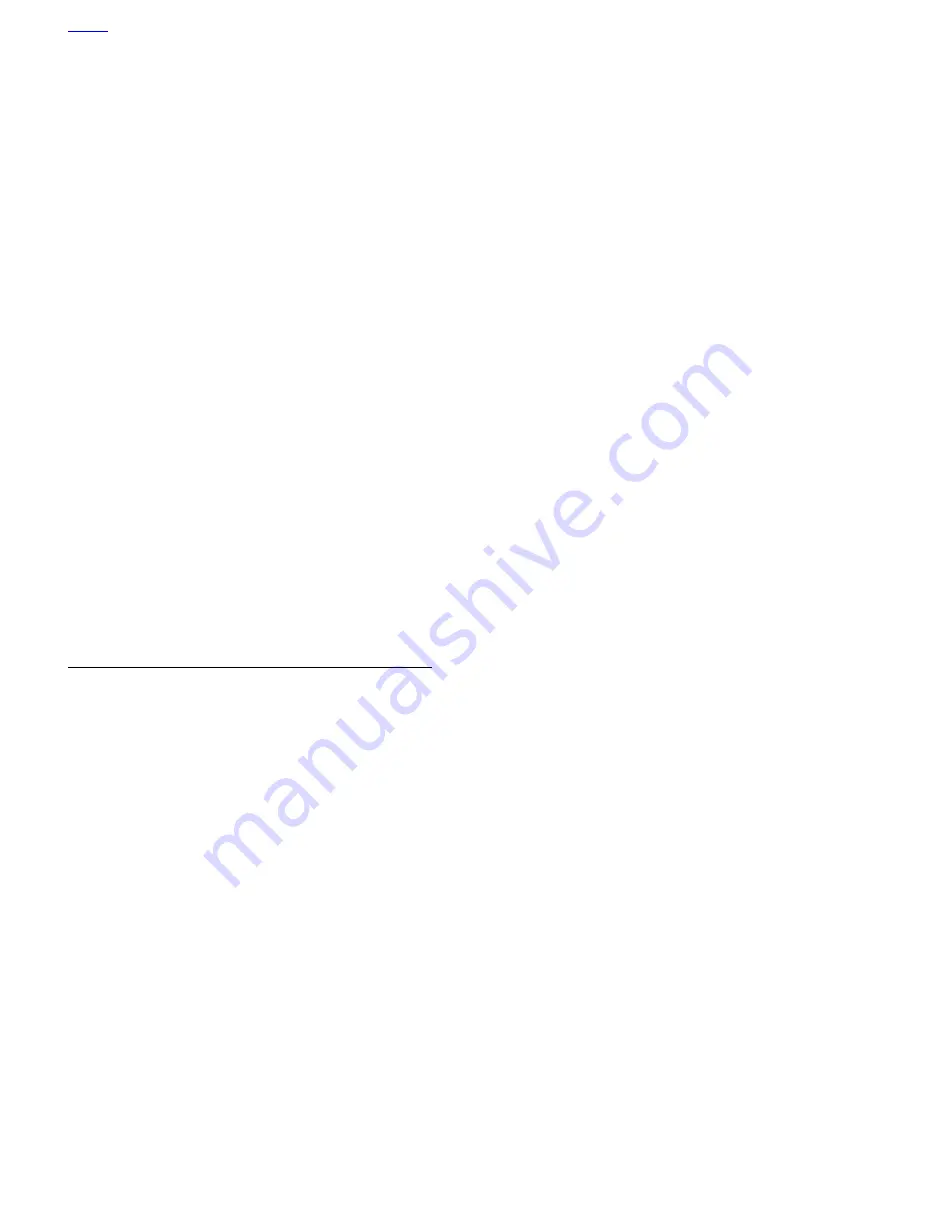
Disassembly and Assembly
Always assemble or disassemble one part at a time. Do not
work on two assemblies simultaneously. Be sure to make all
necessary adjustments. Recheck your work when finished. Be
sure that everything is done.
Operate the vehicle to perform any final check or adjustments.
If all is correct, the vehicle is ready to go back to the customer.
Checking Torques on Fasteners with Lock
Patches
To check the torque on a fastener that has a lock patch:
1.
Set the torque wrench for the lowest setting in the specified
torque range.
2.
Attempt to tighten fastener to set torque. If fastener does
not move and lowest setting is satisfied (torque wrench
clicks), then the proper torque has been maintained.
Magnetic Parts Trays
Magnetic parts trays are becoming common in the service
facility because they are convenient and can keep parts from
becoming lost during a repair procedure.
However, hardened steel parts can become magnetized when
held in magnetic parts trays. Metal fragments that would
ordinarily be washed away in the oil and trapped in the oil filter
or magnetic drain plug during vehicle operation could be cap-
tured by magnetized parts in the engine, potentially causing
accelerated engine wear and damage.
Parts that will be returned to service inside the vehicle's
powertrain such as gears, thrust washers and especially
bearings should never be kept in magnetic parts trays.
REPAIR AND REPLACEMENT
PROCEDURES
Hardware and Threaded Parts
Install thread repair inserts when threaded holes in castings
are stripped, damaged or not capable of withstanding specified
torque.
Replace bolts, nuts, studs, washers, spacers and small
common hardware if missing or damaged. Clean up or repair
minor thread damage with a suitable tap or die.
Replace all damaged or missing lubrication fittings.
Use Teflon pipe sealant or LOCTITE 565 THREAD SEALANT
on pipe fitting threads.
Threadlocking Agents
Always follow specific service manual procedures when working
with fasteners containing preapplied threadlocking agents when
fastener replacement is recommended. When re-using
fasteners containing threadlocking agents, be sure to com-
pletely remove all existing threadlocking agent from fastener
threads with a wire brush or wire wheel. Also, be sure to
remove residual threadlocking agent from fastener hole using
an appropriate thread chasing device and compressed air.
Always use the recommended threadlocking agent for the
specific procedure.
Wiring, Hoses and Lines
Hoses, clamps, electrical wiring, electrical switches or fuel lines
if they do not meet specifications.
Instruments and Gauges
Replace damaged or defective instruments and gauges.
Bearings
Anti-friction bearings must be handled in a special way. To
keep out dirt and abrasives, cover the bearings as soon as
they are removed from the package.
When bearings are installed against shoulders, be sure that
the chamfered side of the bearing always faces the shoulder.
Lubricate bearings and all metal contact surfaces before
pressing into place. Only apply pressure on the part of the
bearing that makes direct contact with the mating part. Install
bearings with numbered side facing out.
Always use the proper tools and fixtures for removing and
installing bearings.
Only remove bearings if necessary. Removal usually damages
bearings requiring them to be replaced with new parts.
Bushings
Do not remove a bushing unless damaged, excessively worn
or loose in its bore. Press out bushings that must be replaced.
When pressing or driving bushings, be sure to apply pressure
in line with the bushing bore. Use a bearing/bushing driver or
a bar with a smooth, flat end. Never use a hammer to drive
bushings.
Inspect the bushing and the mating parts for oil holes before
installation, and be sure all oil holes are properly aligned during
installation.
Gaskets
Always discard gaskets after removal. Replace with new gas-
kets. Never use the same gasket twice. Be sure that gasket
holes match up with holes in the mating part. But be aware
that sections of a gasket may be used to seal passages.
Lip-Type Seals
Lip seals are used to seal oil or grease and are usually installed
with the sealing lip facing the contained lubricant. Seal orient-
ation, however, may vary under different applications.
Seals should not be removed unless necessary. Only remove
seals if required to gain access to other parts or if seal damage
or wear dictates replacement.
Leaking oil or grease usually means that a seal is damaged.
Replace leaking seals to prevent overheated bearings.
Always discard seals after removal. Do not use the same seal
twice.
O-Rings (Pre-Formed Packings)
Always discard O-rings after removal. Replace with new O-
ring. To prevent leaks, lubricate the O-rings before installation.
Apply the same type of lubricant as that being sealed. Be sure
that all gasket, O-ring and seal mating surfaces are thoroughly
clean before installation.
1-4 2010 XB Service: Maintenance
Summary of Contents for XB 2010
Page 1: ...2010 Buell XB Models Service Manual 99490 10Y 2009 Buell Motorcycle Company ...
Page 4: ...Blank Text Here ...
Page 6: ...NOTES ...
Page 22: ...NOTES ...
Page 78: ...1 56 2010 XB Service Maintenance NOTES ...
Page 80: ...NOTES ...
Page 268: ...NOTES ...
Page 306: ...sm00134 Figure 3 46 Valve Spring Compressor HOME 3 38 2010 XB Service Engine ...
Page 338: ...sm00207 Figure 3 98 Flanged Oil Line HOME 3 70 2010 XB Service Engine ...
Page 364: ...3 96 2010 XB Service Engine NOTES ...
Page 366: ...NOTES ...
Page 410: ...4 44 2010 XB Service Fuel System NOTES ...
Page 412: ...NOTES ...
Page 472: ...5 60 2010 XB Service Drive Transmission NOTES ...
Page 474: ...NOTES ...
Page 488: ...sm00366 Figure 6 13 Boot Gap HOME 6 14 2010 XB Service Electrical ...
Page 570: ...6 96 2010 XB Service Electrical NOTES ...
Page 572: ...NOTES ...
Page 596: ...NOTES ...
Page 610: ......
Page 620: ...B 24 2010 XB Service Appendix B Wiring NOTES ...
Page 622: ...NOTES ...
Page 626: ...C 4 2010 XB Service Appendix C Conversions NOTES ...
Page 628: ...NOTES ...
Page 666: ...D 38 2010 XB Service Appendix D Hose and Wire Routing NOTES ...
Page 668: ...NOTES ...
Page 674: ...E 6 2010 XB Service Appendix E Active Intake Japanese Models NOTES ...
Page 675: ...TABLE OF CONTENTS SUBJECT PAGE NO F 1 GLOSSARY F 1 APPENDIX F GLOSSARY ...
Page 676: ...NOTES ...
Page 680: ...F 4 2010 XB Service Appendix F Glossary NOTES ...
Page 706: ...XXVI TORQUE VALUES NOTES ...