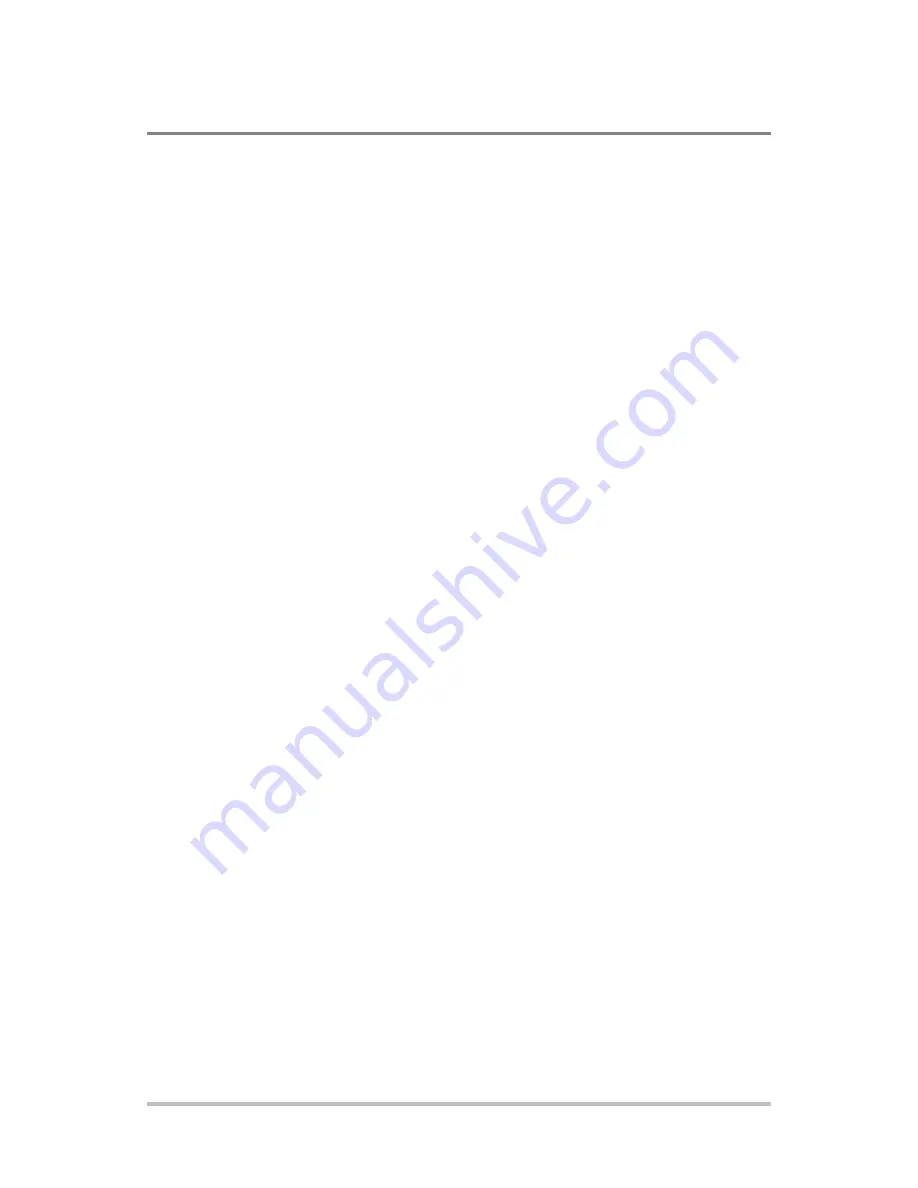
Remote Operation
5-72
M370430-01 Rev B
Save and Recall
The save and recall of user settings can be done using commands as well
as at the front panel. Executing the save and recall commands will have
the same outcome as following the procedure outlined in “Saving User
Setting Memory Locations” on page 3-40 and “Recalling User Setting
Memory Locations” on page 3-41.
Commands:
[:]SYSTem[<channel>]:SAVE {<user settings slot>}
[:]SYSTem[<channel>]:RECall {<user settings slot>}
Where
<user settings slot> is any integer between 1 and 3. The value
corresponds to the setting to be operated on.
Set Analog Programming Level
Setting the analog programming level is used to define the range from 0
to the level that will be input into the analog programming lines to
control the output. The command is equivalent to the procedure
described in “Analog Programming Mode” on page 4-9.
Commands:
[:]SYSTem[<channel>]:COMMunicate:APRogram:LEVel
[:VOLTage][:ISOLated] {?|<level>}
[:]SYSTem[<channel>]:COMMunicate:APRogram:LEVel
[:VOLTage] {?|<level>}
[:]SYSTem[<channel>]:COMMunicate:APRogram:LEVel
:CURRent[:ISOLated] {?|<level>}
[:]SYSTem[<channel>]:COMMunicate:APRogram:LEVel
:CURRent {?|<level>}
Where
<level> is the maximum voltage or resistance that will be input to the
analog inputs.The acceptable range is from 2 to 10 V and 2 to 10kΩ.
Set Remote Programming Interface
The remote source can be select using the following SCPI
commands. These commands are equivalent to the procedure on
“Voltage-Controlled Voltage APG Setup” on page 4-10 and
“Voltage-Controlled Current APG Setup” on page 4-12.
Summary of Contents for Sorensen XG
Page 2: ......
Page 22: ...Contents xx M370430 01 Rev B ...
Page 96: ...Local Operation 3 48 M370430 01 Rev B Figure 3 5 Series Operation ...
Page 102: ...Local Operation 3 54 M370430 01 Rev B ...
Page 210: ...Remote Operation 5 76 M370430 01 Rev B ...
Page 276: ...Communications Options 6 66 M370430 01 Rev B ...
Page 378: ...Rack Mount Options and Installation Instructions D 12 M370430 01 Rev B ...
Page 381: ......