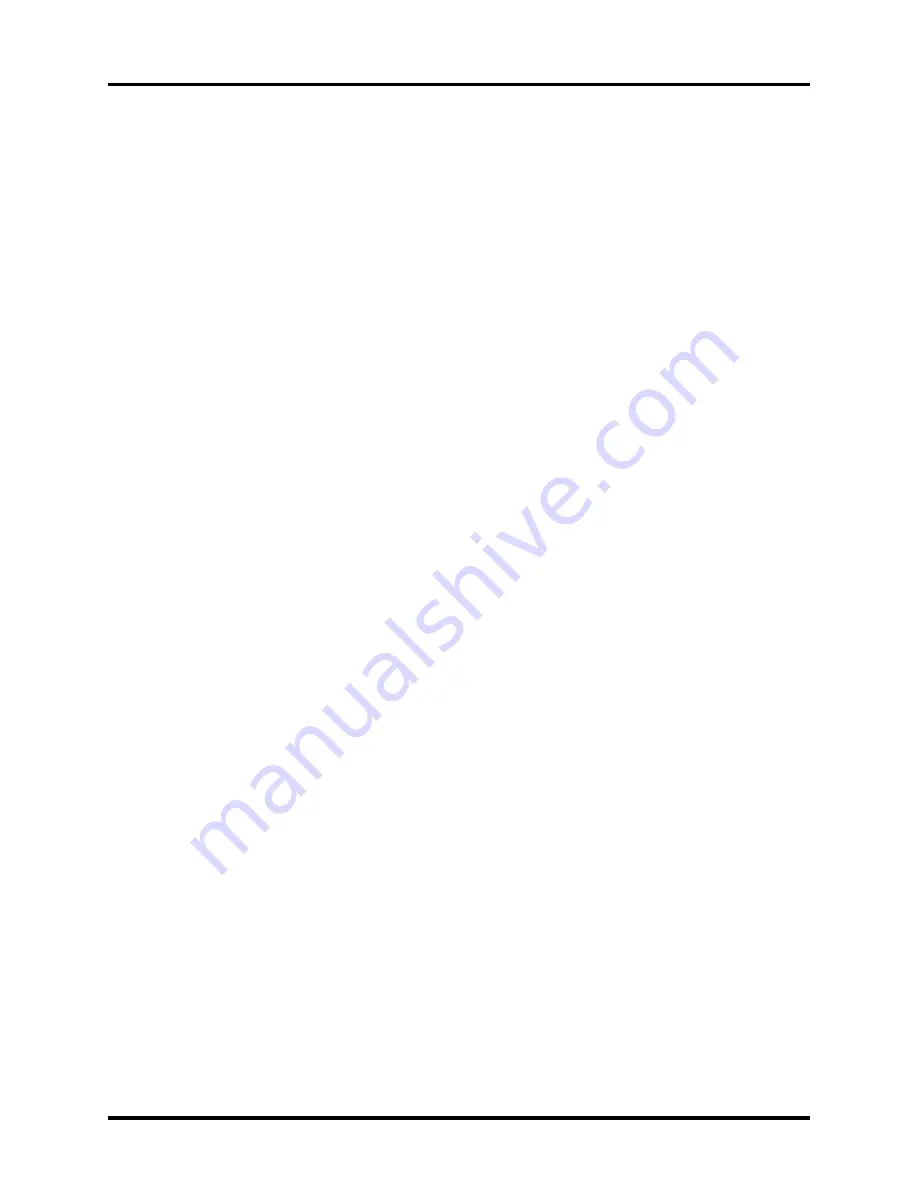
U600 User’s Guide
Parameters
Version 1.4
Aerotech, Inc.
C-9
C.2.10.
AUXDELAY
This parameter suspends fault checking for all faults in the AUXMASK parameter after a
“fault acknowledge” for the specified period of time. This parameter is specified in units
of 10 milliseconds (i.e., 1 = 10ms, 5 = 50ms, etc…).
C.2.11.
AUXMASK
This parameter allows the user to designate which fault conditions will enable the
auxiliary (mode) output associated with the axis. This parameter is a bit mask where each
bit corresponds to a specific fault. Each bit set in this parameter should also be set in the
FAULTMASK axis parameter to enable detection of that fault condition.
C.2.12.
AUXOFFSET
This parameter is added to the master position before doing the auxiliary table lookup.
For example, if the table covers master positions from 0 to 360 degrees and the actual
master position is 2 degrees and the CAMOFFSET parameter is 3 degrees, then the CNC
will use the value of 5 degrees as the master position to search the table. To understand
how this parameter functions, the reader must be familiar with the operation of the
synchronized auxiliary output tables on the UNIDEX 600 Series motion controller. In
brief, each synchronized auxiliary output table entry specifies a master position and a
corresponding state for the auxiliary output. When the observed master position becomes
greater than or equal to that specified in the table entry, the output gets set to the
appropriate state. The only requirement is that the master positions must constantly
increase and never repeat. This parameter refers to an offset applied to the master position
of the auxiliary output table associated with an axis. The point at which the table begins
and ends is advanced or retarded. The user must be aware of the table's setup before
setting the value of this parameter.
C.2.13.
AUXVELCMD
The AUXVELCMD specifies the source of an external velocity command, which is
added to the current axis' velocity command. The AUXVELCMD, while active, does not
change the position command or target of the specified axis. Only the actual position of
the motor will change in response to AUXVELCMD. When AUXVELCMD is disabled
(set to zero) the position command and target are updated to reflect any change in
position, which may have occurred while AUXVELCMD was active. The valid range is
0 to 48 where:
0:
No auxiliary velocity command is added to the current axis velocity
command.
1-16:
Axis 1 to 16’s velocity command is added to the current axis velocity
command.
17-32:
Axis 1 to 16’s actual velocity is added to the current axis velocity command.
Where 17 is axis 1, 18 is axis 2…32 is axis 16.
33-48:
Axis 1 to 16’s torque command is added to the current axis velocity
command. Where 33 is axis 1, 34 is axis 2…48 is axis 16
Summary of Contents for UNIDEX 600 Series
Page 19: ...Table of Contents U600 User s Guide xviii Aerotech Inc Version 1 4...
Page 27: ...Preface U600 User s Guide xxvi Aerotech Inc Version 1 4...
Page 163: ...AerPlot U600 User s Guide 6 6 Aerotech Inc Version 1 4...
Page 169: ...AerReg U600 User s Guide 8 4 Aerotech Inc Version 1 4...
Page 177: ...AerPlotIO U600 User s Guide 10 4 Aerotech Inc Version 1 4...
Page 179: ...Filter U600 User s Guide 11 2 Aerotech Inc Version 1 4...
Page 219: ...PrmSetup U600 User s Guide 13 2 Aerotech Inc Version 1 4...
Page 223: ...Glossary of Terms U600 User s Guide A 4 Aerotech Inc Version 1 4...
Page 353: ......