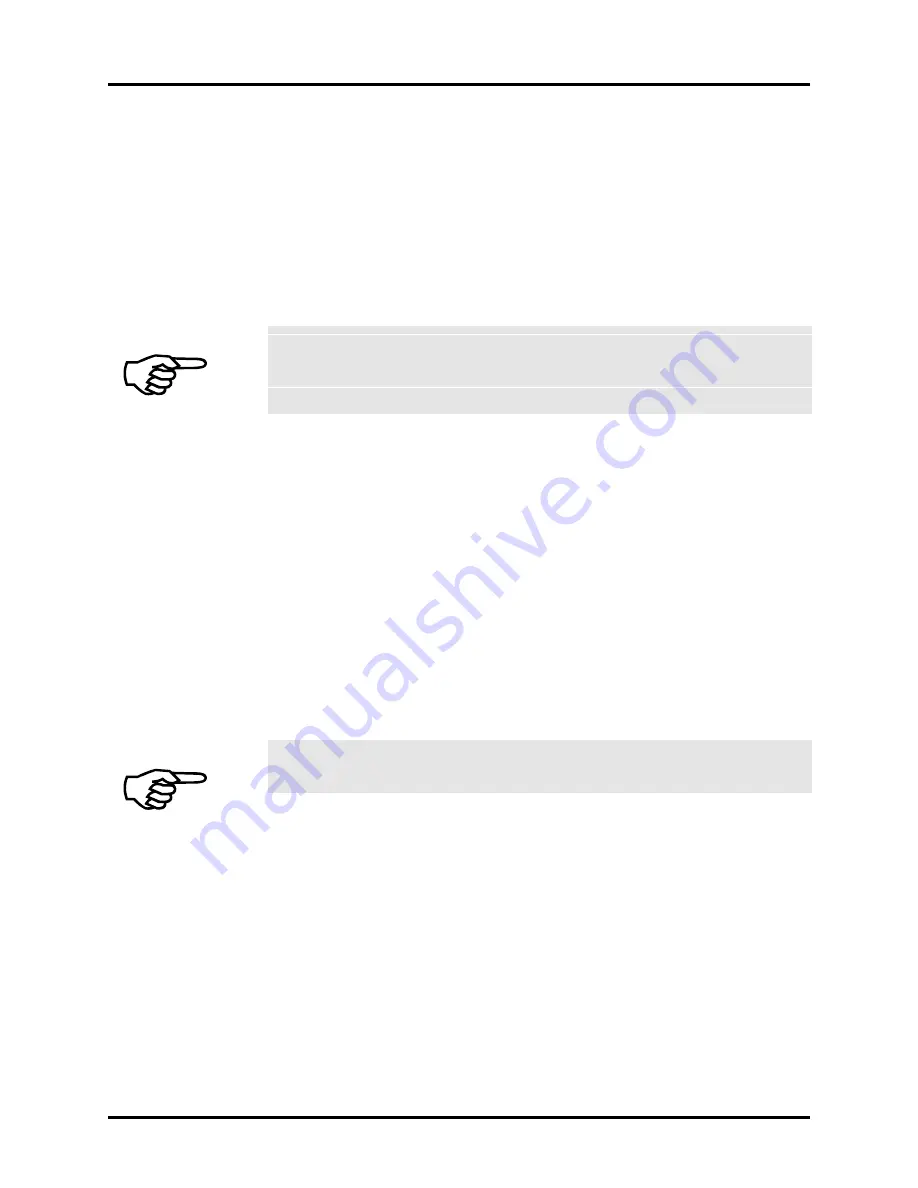
Setup Wizard
U600 User’s Guide
12-18
Aerotech, Inc.
Version 1.4
Stepper Channel
This field specifies the clock and direction channel number for the axis. The 4 channels
on the U600 board are channels 1 through 4. Then encoder expansion cards (4EN-PC) do
not support stepper axes.
Bounded by Software Limits
The Bounded by Software Limits field within the Axis Configuration Wizard is used to
specify if software limits are to be activated for the axis (true or false may be selected).
The software limits are defined by the CWEOT and CCWEOT axis parameters.
If a drive enable signal is required for the stepper axis, specify a D2A (DAC) for the
Command Output so that a DAC output may be specified. The drive enable
associated with this DAC channel may then be used as the drive enable for the
stepper axis.
12.4.6.7.
Null (Virtual) Configuration
A Null (or Virtual) secondary feedback device requires no parameters to be entered. This
is the default configuration.
An axis may be configured as Virtual or NULL by setting the Primary, Command Output
and Secondary feedback devices to Null. In virtual axes, the servo loop is bypassed, and
the Position and Velocity feedback are instead set equal to the Position and Velocity
Commands, respectively. The tracking displays for a virtual axis will display position and
velocity as though it were a real axis, except that the Position Error and Velocity Error
will always be zero. This will facilitate debugging of a CNC motion program when no
drives are physically present. However, even if drives and feedback devices are present,
you may configure the axis as virtual. In this case, no torque will be commanded to the
drive, and no feedback will be read from the feedback device. But when drives and
feedback are properly connected, normally the SIMULATION parameter is a more
convenient way to debug programs, since you won’t need to restore the actual axis
configuration after debugging.
When an axis is configured virtual, the IOLEVEL axis parameter will be
automatically set to 63, to avoid axis faults from being generated.
If a virtual axis is homed, it will immediately set the current position to the value of the
HomeOffsetInch (or HomeOffsetDeg) task parameter, rather than simulating any motion.
Axis calibration, hardware and software limits have no effect on virtual axes.
12.4.6.8.
Configuring Dual Loop Axes
The Hall effect, limits, encoder fault and drive fault inputs are always read from the same
channel. The axis status words are derived from a direct read of this data as part of the
background task. The servo loop reads the hall inputs directly because they need to have
minimal latency for motor commutation. This implies that the servo loop can (and does in
this instance) look at a different source for the hall inputs than does the axis status word.
The use must be aware of this when configuring axes.
Dual loop encoder axes MUST be configured as follows:
Summary of Contents for UNIDEX 600 Series
Page 19: ...Table of Contents U600 User s Guide xviii Aerotech Inc Version 1 4...
Page 27: ...Preface U600 User s Guide xxvi Aerotech Inc Version 1 4...
Page 163: ...AerPlot U600 User s Guide 6 6 Aerotech Inc Version 1 4...
Page 169: ...AerReg U600 User s Guide 8 4 Aerotech Inc Version 1 4...
Page 177: ...AerPlotIO U600 User s Guide 10 4 Aerotech Inc Version 1 4...
Page 179: ...Filter U600 User s Guide 11 2 Aerotech Inc Version 1 4...
Page 219: ...PrmSetup U600 User s Guide 13 2 Aerotech Inc Version 1 4...
Page 223: ...Glossary of Terms U600 User s Guide A 4 Aerotech Inc Version 1 4...
Page 353: ......