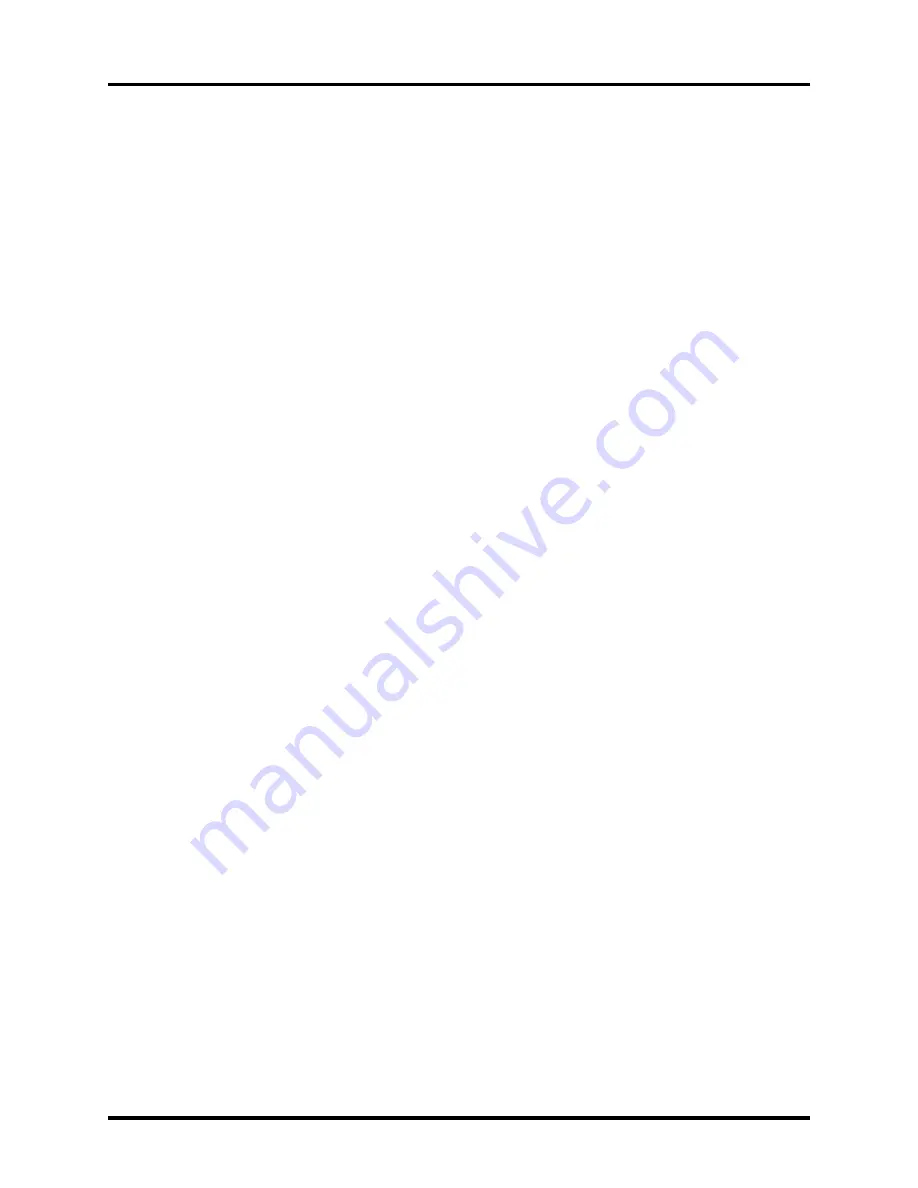
Getting Started
U600 User’s Guide
2-20
Aerotech, Inc.
Version 1.4
2.10.
Accelerations
All moves except synchronous CNC moves (G1, G2, G3) and Cam Table motion use a
set of axis parameters to determine acceleration and deceleration behavior. This includes
homing and jogging motion.
The user must make sure these axis parameters are set properly before moving an axis:
ACCELMODE, ACCEL, and ACCELRATE. Acceleration takes place at the given rate,
(ACCELRATE) or within the given time (ACCEL) based on the value of ACCELMODE.
ACCELMODE also determines the profile (as seen in velocity/time space) of the
acceleration.
A similar set of axis parameters: DECELMODE, DECEL, and DECELRATE exist for
setting the deceleration behavior of an axis. These also must be set properly.
2.11.
Axis Tuning
The servo loop gains must be adjusted based upon the load and required performance of
the axis. For detailed information on tuning a servo loop, refer to Chapter 5: AerTune.
The following axis parameters are used for adjusting the response of a torque (current)
mode servo loop: KI, KP, PGAIN, VFF, AFFGAIN, ALPHA, and, the VGAIN parameter
for large frictional loads.
The following axis parameters are used for adjusting the response of a velocity mode
servo loop (see section 2.3.3.): PGAIN, VGAIN, AFFGAIN, and ALPHA. Both the KI and
KP should be set to zero for velocity mode servo loops. In addition, the DACOFFSET
parameter may be used for nulling offsets from the DAC that may be present in velocity
loop systems.
Axis tuning is thoroughly described in Chapter 5: AerTune, which is designed for tuning
and monitoring an axis’ performance.
2.12.
Jogging
The user can use the U600MMI in the manual page to jog the axes. Set the axes to move,
the distances and velocities, enable the drive, and push an arrow button.
In AerDebug, the user can easily test axis motion with the INDEX or MOVETO CNC
commands. See the example below, where we “jog” axis 2, 4000 mm from the current
position, at a speed of 500 mm/second. Do not enter the text after the “;” below, these are
just comments.
AX 2
EXEL “G71”
; Sets unit used in “INDEX” to mm. Do a
; G70 instead to set them to inches
EXEL “MAP Y2”
; “Y” now means physical axis (channel) 2
EXEL “BIND Y”
PARMSET A DRIVE 1
EXEL “INDEX Y 4000 500”
; Starts the motion
These commands can be used to monitor the progress of the move.
TSKI
; This should show “No Errors” in the fault line
PARMMON A POS
; Shows the position moving (counts)
PARMMON M POSUNITS
; Shows the position moving (mm/inch)
Summary of Contents for UNIDEX 600 Series
Page 19: ...Table of Contents U600 User s Guide xviii Aerotech Inc Version 1 4...
Page 27: ...Preface U600 User s Guide xxvi Aerotech Inc Version 1 4...
Page 163: ...AerPlot U600 User s Guide 6 6 Aerotech Inc Version 1 4...
Page 169: ...AerReg U600 User s Guide 8 4 Aerotech Inc Version 1 4...
Page 177: ...AerPlotIO U600 User s Guide 10 4 Aerotech Inc Version 1 4...
Page 179: ...Filter U600 User s Guide 11 2 Aerotech Inc Version 1 4...
Page 219: ...PrmSetup U600 User s Guide 13 2 Aerotech Inc Version 1 4...
Page 223: ...Glossary of Terms U600 User s Guide A 4 Aerotech Inc Version 1 4...
Page 353: ......