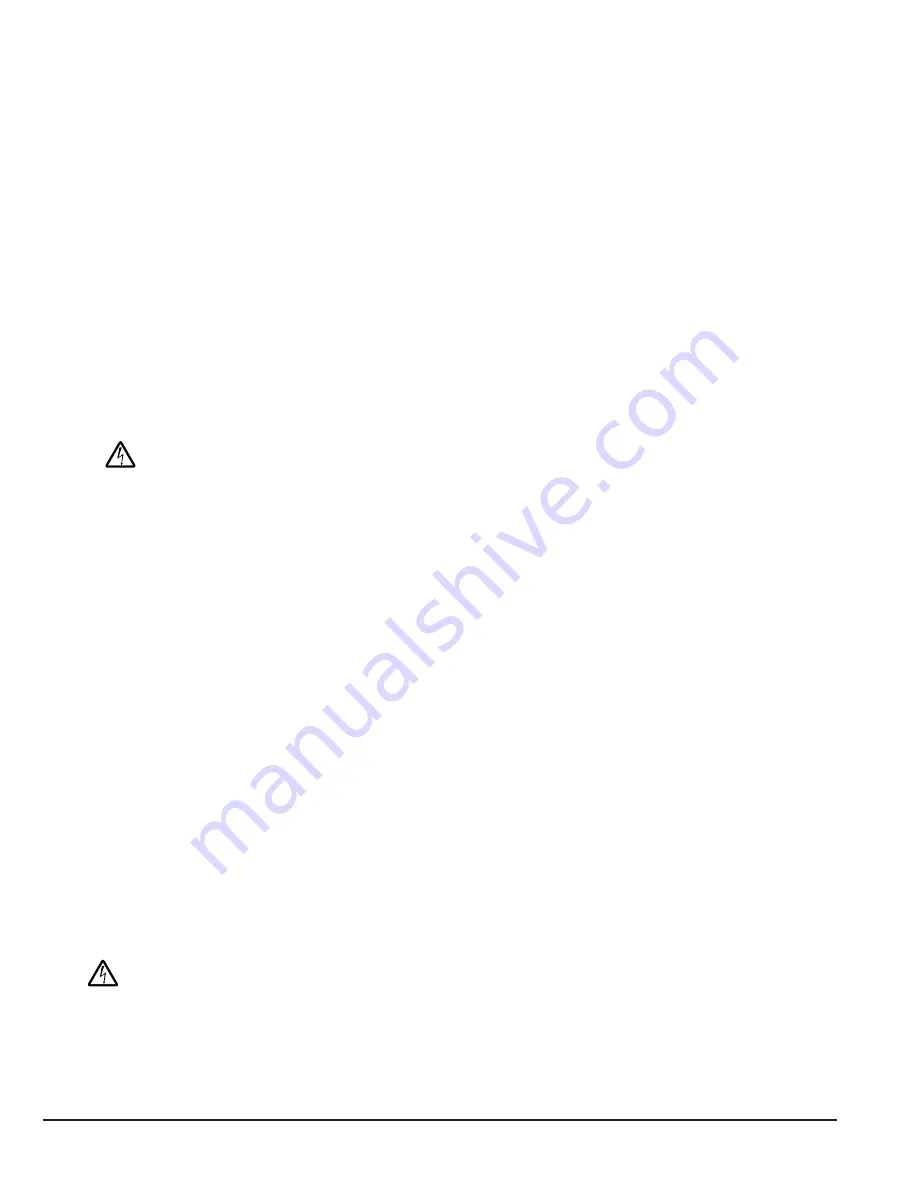
1-2 Introduction
3AXD50000011888
• Do not make any insulation or voltage withstand tests on the drive.
• Do not connect the drive to a voltage higher than what is marked on the type designation label. Higher voltage can
activate the brake chopper and lead to brake resistor overload, or activate the overvoltage controller what can lead to
motor rushing to maximum speed.
Note:
• The motor cable terminals on the drive are at a dangerously high voltage when the input power is on, regardless of
whether the motor is running or not.
• The DC terminals (UDC+, UDC-) carry a dangerous DC voltage (over 500V) when internally connected to the intermediate
DC circuit.
• Depending on the external wiring, dangerous voltages (115V, 220V or 230V) may be present on the terminals of relay
outputs (XRO1, XRO2 and XRO3).
• The Safe torque off function does not remove the voltage from the main and auxiliary circuits. The function is ineffective
against deliberate sabotage or misuse.
Grounding
- These instructions are intended for all who are responsible for the grounding of the drive.
WARNING:
Ignoring the following instructions can cause physical injury or death, or damage to the
equipment:
• Ground the drive, motor and adjoining equipment to ensure personnel safety in all circumstances, and to reduce
electromagnetic emission and interference.
• Make sure that grounding conductors are adequately sized as required by safety regulations.
• In a multiple-drive installation, connect each drive separately to protective earth (PE).
• Where EMC emissions must be minimized, make a 360° high frequency grounding of cable entries in order to suppress
electromagnetic disturbances. In addition, connect the cable shields to protective earth (PE) in order to meet safety
regulations.
• Do not install a drive with EMC filter E200 or +E202 on an ungrounded power system or a high-resistance-
grounded (over 30ohms) power system.
Note:
• Power cable shields are suitable for equipment grounding conductors only when adequately sized to meet safety
regulations.
• Standard EN 61800-5-1 (section 4.3.5.5.2.) requires that as the normal touch current of the drive is higher than 3.5mA AC
or 10mA DC, you must use a fixed protective earth connection and
• a cross-section of the protective earthing conductor of at least 10 mm
2
Cu or 16 mm
2
Al,
or
• automatic disconnection of the supply in case of discontinuity of the protective earthing conductor,
or
• a second protective earthing conductor of the same cross-sectional area as the original protective earthing conductor.
Permanent Magnet Motor Drives
- These are additional warnings concerning permanent magnet motor drives.
WARNING:
Ignoring the following instructions can cause physical injury or death, or damage to the equipment:
• Do not work on the drive when the permanent magnet motor is rotating. Also, when the supply power is switched off and
the inverter is stopped, a rotating permanent magnet motor feeds power to the intermediate circuit of the drive and the
supply connections become live.
Summary of Contents for ACS880+N5350
Page 1: ... ABB INDUSTRIAL DRIVES ACS880 N5350 cooling tower drives User s guide ...
Page 32: ...Terminal Specifications 4 7 3AXD50000011888 Figure 4 3 Cable Conduit Installation R6 R7 R8 R9 ...
Page 193: ...13 20 Troubleshooting 3AXD50000011888 ...
Page 211: ...C 2 CE Guidelines 3AXD50000011888 Figure C 1 Declaration of Conformity ...
Page 212: ...CE Guidelines C 3 3AXD50000011888 ...
Page 246: ...Ethernet IP Setup G 5 3AXD50000011888 8 The ACS880 CTD Drive is now added to the PLC I O ...