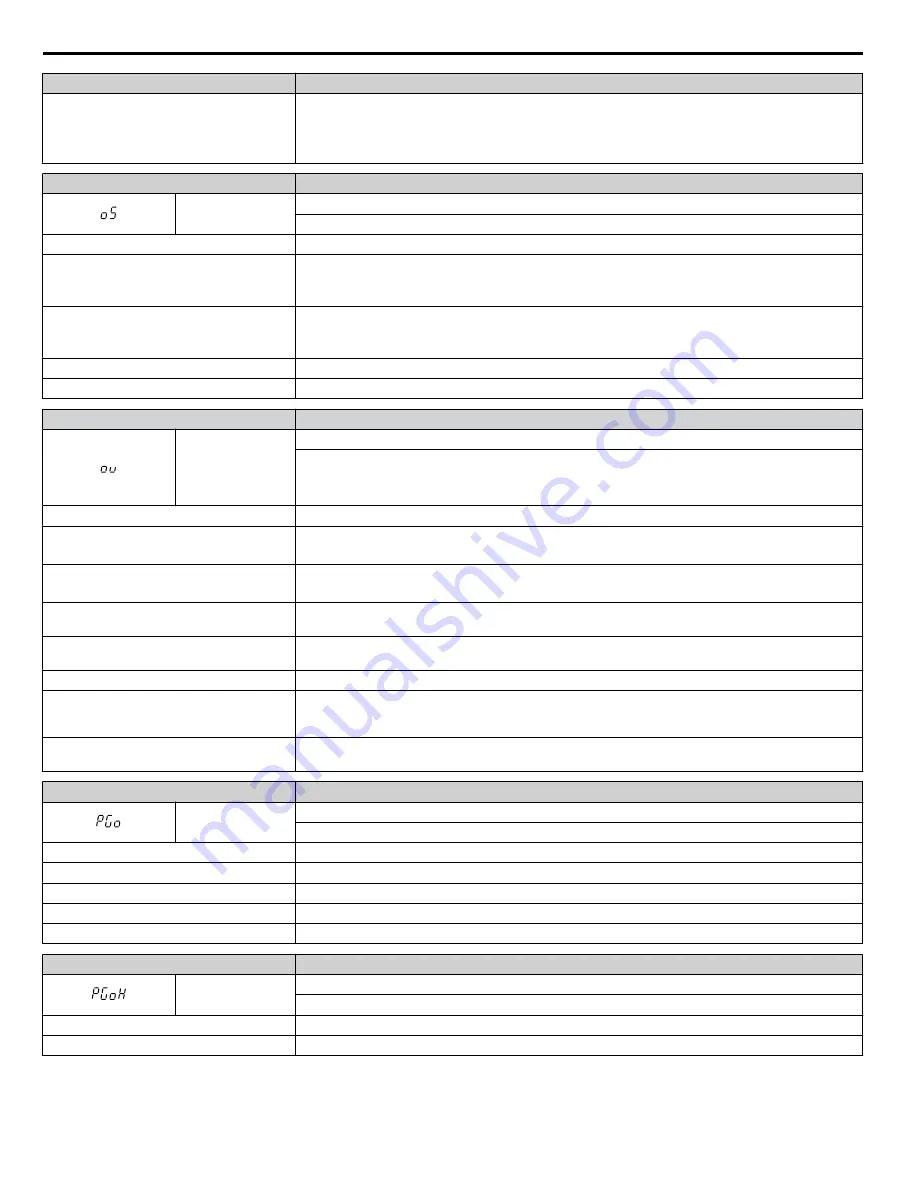
Digital Operator Display
Fault Name
External operator is not properly connected to
the drive
• Check the connection between the operator and the drive.
• Replace the cable if damaged.
• Turn off the drive input power and disconnect the operator. Reconnect the operator and reapply drive
input power.
Digital Operator Display
Fault Name
oS
Overspeed
The motor speed feedback exceeded the F1-08 setting.
Cause
Possible Solution
Overshoot is occurring
• Reduce the C5-01, Speed Control Proportional Gain 1, setting and increase the C5-02, Speed Control
Integral Time 1, setting.
• If using Closed Loop Vector mode, enable Feed Forward and perform Inertia Auto-Tuning.
Incorrect speed feedback scaling if terminal
RP is used as speed feedback input in V/f
control
• Set H6-02 to the value of the speed feedback signal frequency when the motor runs at the maximum
speed.
• Adjust the input signal using parameters H6-03 through H6-05.
Incorrect number of PG pulses has been set
Check and correct parameter F1-01.
Inappropriate parameter settings
Check the setting for the overspeed detection level and the overspeed detection time (F1-08 and F1-09).
Digital Operator Display
Fault Name
ov
Control Circuit Overvoltage
Voltage in the control circuit has exceeded the overvoltage level.
• For 200 V class drives: approximately 450 V
• For 400 V class drives: approximately 900 V
Cause
Possible Solution
Ground fault in the output circuit causing the
capacitor to overcharge.
• Check the motor wiring for ground faults.
• Correct grounding shorts and reapply power.
Drive input power voltage is too high.
• Check the voltage.
• Lower drive input power voltage within the limits listed in the specifications.
The capacity of the input power supply is too
small.
Use a power supply that has at least twice the input capacity of the drive.
The input power supply repeatedly turned on
and off over a short period of time.
Implement countermeasures so that chattering does not occur for the input power supply.
An I/O terminal is loose.
Check the tightening torque of the I/O terminals.
Chattering in the magnetic contactor (MC)
installed between the drive output terminals
and the motor.
Implement countermeasures so that chattering does not occur for the MC.
There is a phase loss or an imbalance in the
interphase voltages of the input power supply. Check the status of the input power supply and eliminate phase losses and imbalance.
Digital Operator Display
Fault Name
PGo
PG Disconnect (for any control modes using a PG option card)
No PG pulses are received for longer than the time set to F1-14.
Cause
Possible Solution
PG cable is disconnected
Reconnect the cable.
PG cable wiring is wrong
Correct the wiring.
PG has no power
Check the power line to the PG encoder.
PG encoder brake is clamped shut
Ensure the motor brake releases properly.
Digital Operator Display
Fault Name
PGoH
PG Hardware Fault (detected when using a PG-X3 option card)
PG cable is not connected properly.
Cause
Possible Solution
PG cable is disconnected
Reconnect the cable and check the setting of F1-20.
6.4 Fault Detection
380
YASKAWA ELECTRIC SIEP C710636 04D U1000 Industrial MATRIX Drive Technical Manual
Содержание U1000 iQpump Drive
Страница 705: ......