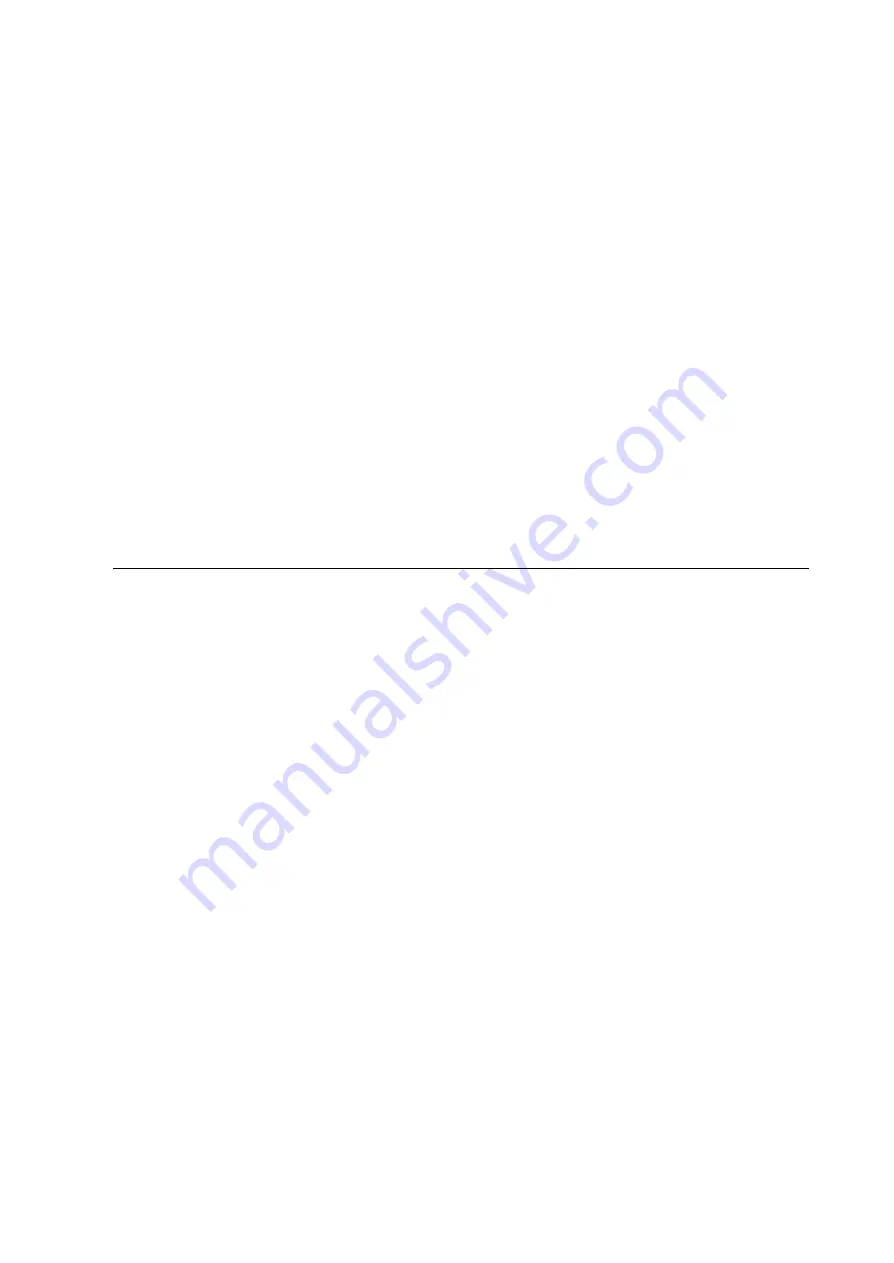
54
(29) Swift Lift 2 Limit Timer TA2 (S4-13)
If the acceleration hold or acceleration time extension in the high-speed area continues for longer than the time set to
the Swift Lift 2 Timer, then acceleration will stop for that period of time. Normally, set between 50% to 100% of the
acceleration time in the high speed area.
Prevents re-acceleration when making a transition in Swift Lift or when the load being lowered has reached the
ground.
(30) Swift Lift 2 Fault Detection Level LEA2 (S4-15), Detection Time TEA2 (S4-16)
This parameter sets the level of protection level and the detection time so that the output power is not suppressed even
if the drive stops acceleration or acceleration time is smoothed out.
S4-15 is set relative to the motor rated power (normally between 100% to 150%).
S4-16 is set as high as 0.1~1.0sec.
(31) Swift Lift 2 Accel Time Gain GAT (S4-17)
In order to accurately detect the load power and reduce the effects of acceleration power, this parameter adjusts the
acceleration time to keep it above S4-08 (Swift Lift 2 Activation Frequency). The actual acceleration time becomes a
combination of the value in C1-xx multiplied by S4-17 (Swift Lift 2 Acceleration Time Gain).
Normally set between 1.5 and 3.0 (at 1.0, the acceleration rate is identical to the acceleration time setting value in
C1-
xx
).
(32) Operation Selection During Swift Lift 2 Regen (S4-18)
Affected by the acceleration power, when detection cannot be performed due to insufficient load power during
regeneration or when Swift Lift is unnecessary during regen, then parameter S4-18 is disabled (initial/default settings
= disabled).
If regeneration is occurring, then the Swift Lift 2 Activation Frequency will not be reached even with Swift Lift 2
functions enabled.
Note: Be sure that adequate protection in the system side are taken for load-slipping when using Swift Lift 1 or 2.y7
(33) Swift Lift 1 Torque Bias (S4-19, -20)
Open Loop Vector Control Mode
Sets the mechanical loss for the crane. For information on tuning, see section 6.4.1, “Swift Lift 1 Function”.
(34) Output Phase Detection Level (L8-08)
Normally set to 50%.
·
By using motor switching functions, the setting value is reduced so that the output phase (LF) is not inaccurately
detected when the motor capacity is much smaller in relation to the drive capacity.
Be sure the wiring on the output side of the drive is correct when the setting value is reduced. Also, avoid reducing the
setting more than is necessary.
When using applications with a contactor installed to the output side of the drive, be sure that the contactor is not left
open while the drive is running. No output phase detection will occur if three phases loose.
Содержание CIMR-F7Z
Страница 3: ......