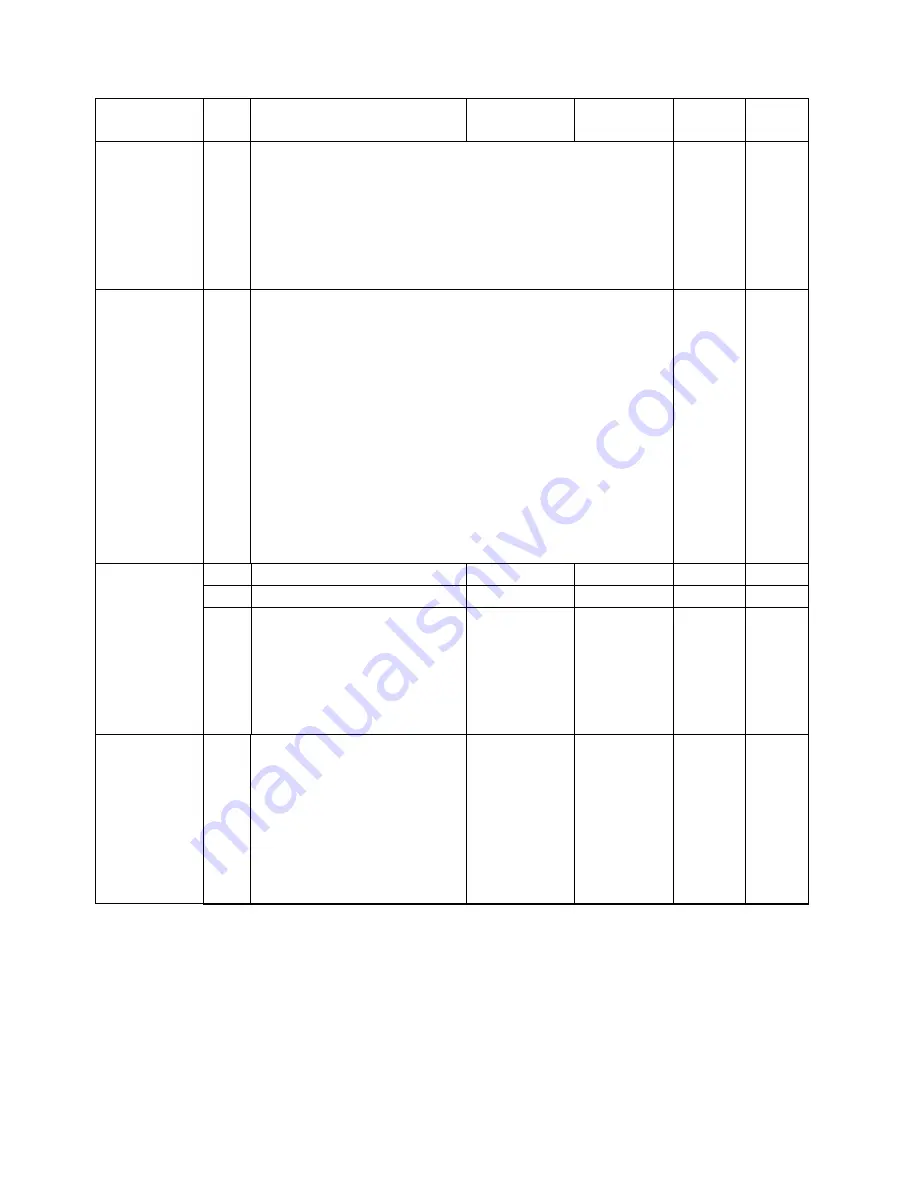
21
Function
Fn_
xx
Description
Engineering
Units
Range
Factory
Setting
Page
Fault Contact
Control
(Continued)
97
x0xx : Fault Contact is Not energized during
External Emergency Stop
x1xx : Fault Contact is energized during
External Emergency Stop
0xxx : Fault Contact is Not energized during
External Base Block
1xxx : Fault Contact is energized during External Base Block
0000
50
Fault Contact
Control
98
xxx0 : Fault Contact is Not energized after
Overtorque is Detected
xxx1 : Fault Contact is energized after Overtorque is Detected
xx0x : Fault Contact is Not energized after
Electronic Thermal Motor Protection is activated
xx1x : Fault Contact is energized after
Electronic Thermal Motor Protection is activated
x0xx : Fault Contact is Normally Open (NO)
x1xx : Fault Contact is Normally Closed (NC)
0xxx : Fault Contact is Not energized after
Electronic Thermal Inverter Protection is activated
1xxx : Fault Contact is energized after
Electronic Thermal Inverter Protection is activated
0000
50
99
Reserved for Future Use
50
100 Communication Address
1
1 - 32
*3
51
Parameter
Control for
Communication
101 Baud Rate of Communication
1
0 : 4800 bps
1 : 9600 bps
2 : 19200
bps
3 : 38400
bps
*3
51
Parameter
Control for
Communication
102 xxx0 : 1 Stop Bit
xxx1 : 2 Stop Bits
xx0x : Even Parity
xx1x : Odd Parity
x0xx : With Parity
x1xx : Without Parity
0xxx : 8 Bits Data
1xxx : 7 Bits Data
*3
52
51