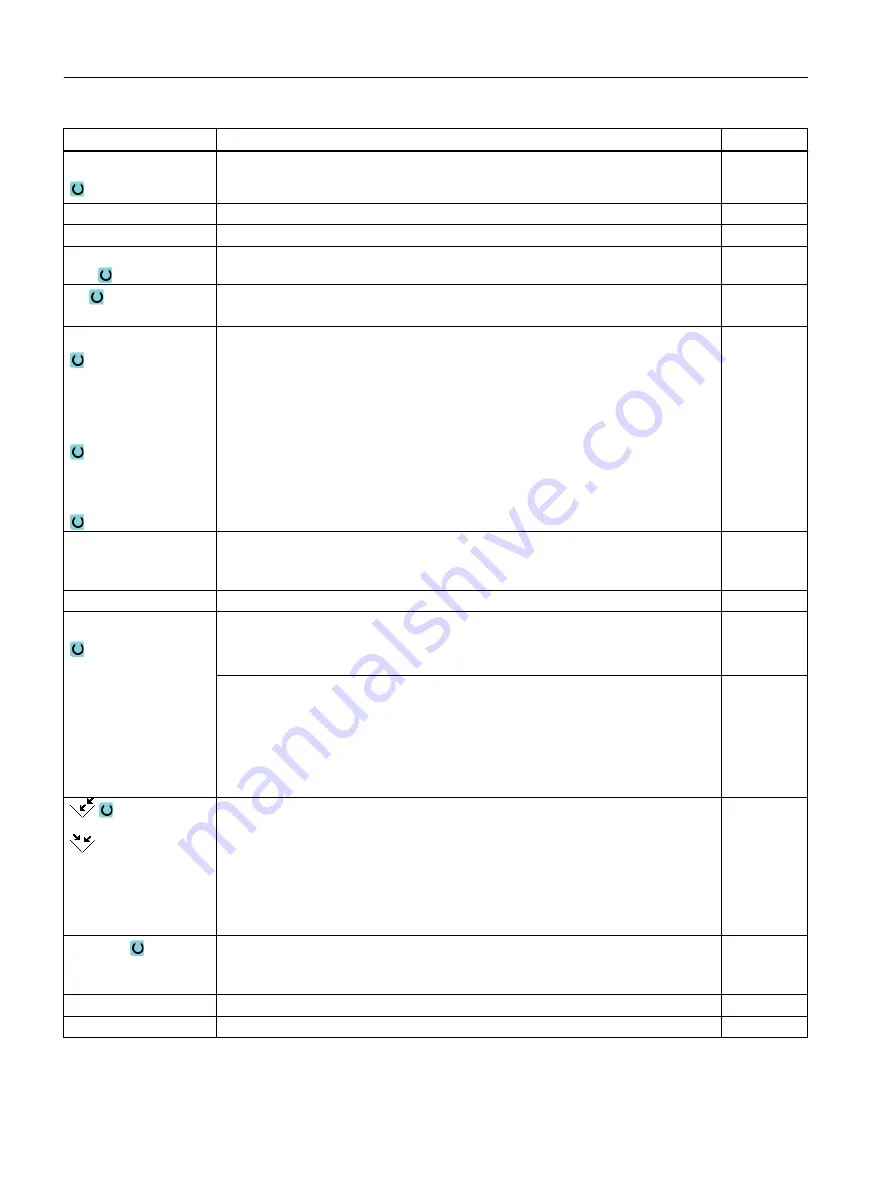
Parameter
Description
Unit
Thread
● Internal thread
● External thread
X0
Reference point X ∅ (abs, always diameter)
mm
Z0
Reference point Z (abs)
mm
X1 or
X1α
End point X ∅ (abs) or end point in relation to X0 (inc) or thread taper
incremental dimensions: The sign is also evaluated.
mm or
degrees
Z1
End point Z (abs) or end point in relation to Z0 (inc)
Incremental dimensions: The sign is also evaluated.
mm
LW
or
LW2
or
LW2 = LR
Thread advance (inc)
The starting point for the thread is the reference point (X0, Z0) brought forward by the
thread advance W. The thread advance can be used if you wish to begin the indi‐
vidual cuts slightly earlier in order to also produce a precise start of thread.
Thread run-in (inc)
The thread run-in can be used if you cannot approach the thread from the side and
instead have to insert the tool into the material (e.g. lubrication groove on a shaft).
Thread run-in = thread run-out (inc)
mm
mm
mm
LR
Thread run-out (inc)
The thread run-out can be used if you wish to retract the tool obliquely at the end of
the thread (e.g. lubrication groove on a shaft).
mm
H1
Thread depth (inc)
mm
DP
or
αP
Infeed slope as flank (inc) – (alternative to infeed slope as angle)
DP > 0: Infeed along the rear flank
DP < 0: Infeed along the front flank
mm
Infeed slope as angle – (alternative to infeed slope as flank)
α > 0: Infeed along the rear flank
α < 0: Infeed along the front flank
α = 0: Infeed at right angle to cutting direction
If you wish to infeed along the flanks, the maximum absolute value of this parameter
may be half the flank angle of the tool.
Degrees
Infeed along the flank
Infeed with alternating flanks (alternative)
Instead of infeed along one flank, you can infeed along alternating flanks to avoid
always loading the same tool cutting edge. As a consequence you can increase the
tool life.
α > 0: Start at the rear flank
α < 0: Start at the front flank
D1 or ND
(only for ∇ and
∇ + ∇∇∇)
First infeed depth or number of roughing cuts
The respective value is displayed when you switch between the number of roughing
cuts and the first infeed.
mm
U
Finishing allowance in X and Z – (only for ∇ and ∇ + ∇∇∇)
mm
NN
Number of noncuts - (only for ∇∇∇ and ∇ + ∇∇∇)
Programming technology functions (cycles)
10.2 Rotate
Turning
428
Operating Manual, 06/2019, A5E44903486B AB
Содержание SINUMERIK 840D sl
Страница 8: ...Preface Turning 8 Operating Manual 06 2019 A5E44903486B AB ...
Страница 70: ...Introduction 2 4 User interface Turning 70 Operating Manual 06 2019 A5E44903486B AB ...
Страница 274: ... Creating a G code program 8 8 Selection of the cycles via softkey Turning 274 Operating Manual 06 2019 A5E44903486B AB ...
Страница 275: ... Creating a G code program 8 8 Selection of the cycles via softkey Turning Operating Manual 06 2019 A5E44903486B AB 275 ...
Страница 282: ...Creating a G code program 8 10 Measuring cycle support Turning 282 Operating Manual 06 2019 A5E44903486B AB ...
Страница 344: ...Creating a ShopTurn program 9 19 Example Standard machining Turning 344 Operating Manual 06 2019 A5E44903486B AB ...
Страница 716: ...Collision avoidance 12 2 Set collision avoidance Turning 716 Operating Manual 06 2019 A5E44903486B AB ...
Страница 774: ...Tool management 13 15 Working with multitool Turning 774 Operating Manual 06 2019 A5E44903486B AB ...
Страница 834: ...Managing programs 14 19 RS 232 C Turning 834 Operating Manual 06 2019 A5E44903486B AB ...
Страница 856: ...Alarm error and system messages 15 9 Remote diagnostics Turning 856 Operating Manual 06 2019 A5E44903486B AB ...
Страница 892: ...Working with two tool carriers 18 2 Measure tool Turning 892 Operating Manual 06 2019 A5E44903486B AB ...
Страница 912: ...HT 8 840D sl only 20 5 Calibrating the touch panel Turning 912 Operating Manual 06 2019 A5E44903486B AB ...
Страница 927: ...Appendix A A 1 840D sl 828D documentation overview Turning Operating Manual 06 2019 A5E44903486B AB 927 ...