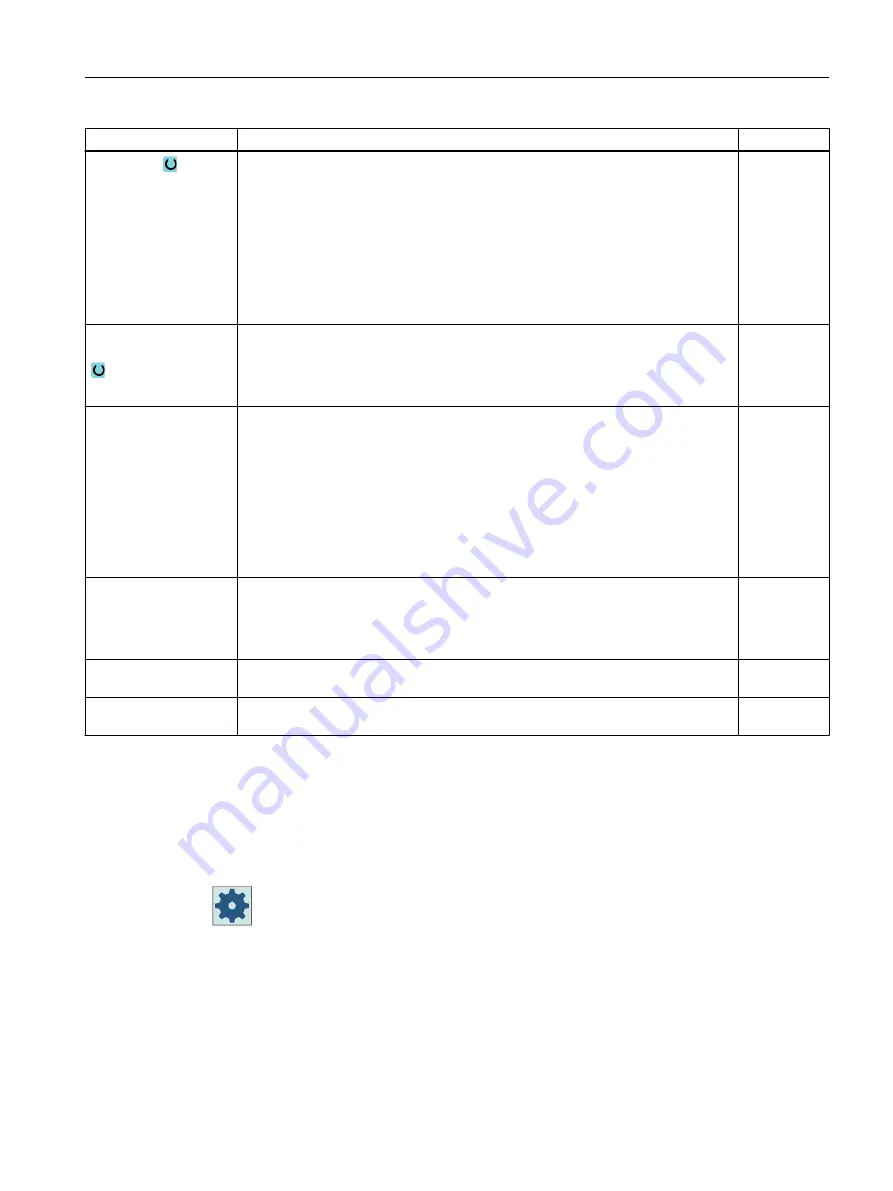
Parameter
Description
Unit
Work offset
Work offset in which the coordinate system, which was shifted according to ZW and
by ZV as well as mirrored in Z, must be saved:
● Basic reference
● G54
● G55
● G56
● G57
● ...
Write to the
work offset
● Yes
The Z value of the work offset can be directly written to the input screen form.
● No
The actual Z value of the work offset is used.
ZV - only for work offset
write "yes"
● Offset Z = 0 (abs)
● Workpiece zero is offset in Z direction (inc, the sign is also evaluated)
The parameter is used to ensure that the correct display is shown in the
simulation. It has no influence on machining itself.
The workpiece is re-clamped when switching between the main spindle and
counterspindle. The new work offset defines the position for machining at the
machine. However, the simulation must know by which amount the work offset
has shifted with respect to the workpiece, so that both sides of the machining can
be displayed.
mm
mm
Park counter-spindle -
for machining with main
spindle
● Yes
The counter-spindle is traversed to the park position.
● No
The counter-spindle is not traversed.
Z4P - for machining
with main spindle
Park position of the counter-spindle (abs); MCS
mm
Z4W - for machining
with counter-spindle
Machining position of the counter-spindle (abs); MCS
mm
10.7.18
Machining with fixed counterspindle
If your lathe is equipped with a second spindle, which is setup as a counterspindle and cannot
be traversed, then the workpieces must be manually reclamped
Machine manufacturer
Please refer to the machine manufacturer's specifications.
Machining with main spindle and counterspindle
For instance, a new blank can be clamped in the main spindle, and a blank that has already
been machined at the front can be clamped in the counterspindle. With the ShopTurn program,
Programming technology functions (cycles)
10.7 Additional cycles and functions in ShopTurn
Turning
Operating Manual, 06/2019, A5E44903486B AB
657
Содержание SINUMERIK 840D sl
Страница 8: ...Preface Turning 8 Operating Manual 06 2019 A5E44903486B AB ...
Страница 70: ...Introduction 2 4 User interface Turning 70 Operating Manual 06 2019 A5E44903486B AB ...
Страница 274: ... Creating a G code program 8 8 Selection of the cycles via softkey Turning 274 Operating Manual 06 2019 A5E44903486B AB ...
Страница 275: ... Creating a G code program 8 8 Selection of the cycles via softkey Turning Operating Manual 06 2019 A5E44903486B AB 275 ...
Страница 282: ...Creating a G code program 8 10 Measuring cycle support Turning 282 Operating Manual 06 2019 A5E44903486B AB ...
Страница 344: ...Creating a ShopTurn program 9 19 Example Standard machining Turning 344 Operating Manual 06 2019 A5E44903486B AB ...
Страница 716: ...Collision avoidance 12 2 Set collision avoidance Turning 716 Operating Manual 06 2019 A5E44903486B AB ...
Страница 774: ...Tool management 13 15 Working with multitool Turning 774 Operating Manual 06 2019 A5E44903486B AB ...
Страница 834: ...Managing programs 14 19 RS 232 C Turning 834 Operating Manual 06 2019 A5E44903486B AB ...
Страница 856: ...Alarm error and system messages 15 9 Remote diagnostics Turning 856 Operating Manual 06 2019 A5E44903486B AB ...
Страница 892: ...Working with two tool carriers 18 2 Measure tool Turning 892 Operating Manual 06 2019 A5E44903486B AB ...
Страница 912: ...HT 8 840D sl only 20 5 Calibrating the touch panel Turning 912 Operating Manual 06 2019 A5E44903486B AB ...
Страница 927: ...Appendix A A 1 840D sl 828D documentation overview Turning Operating Manual 06 2019 A5E44903486B AB 927 ...