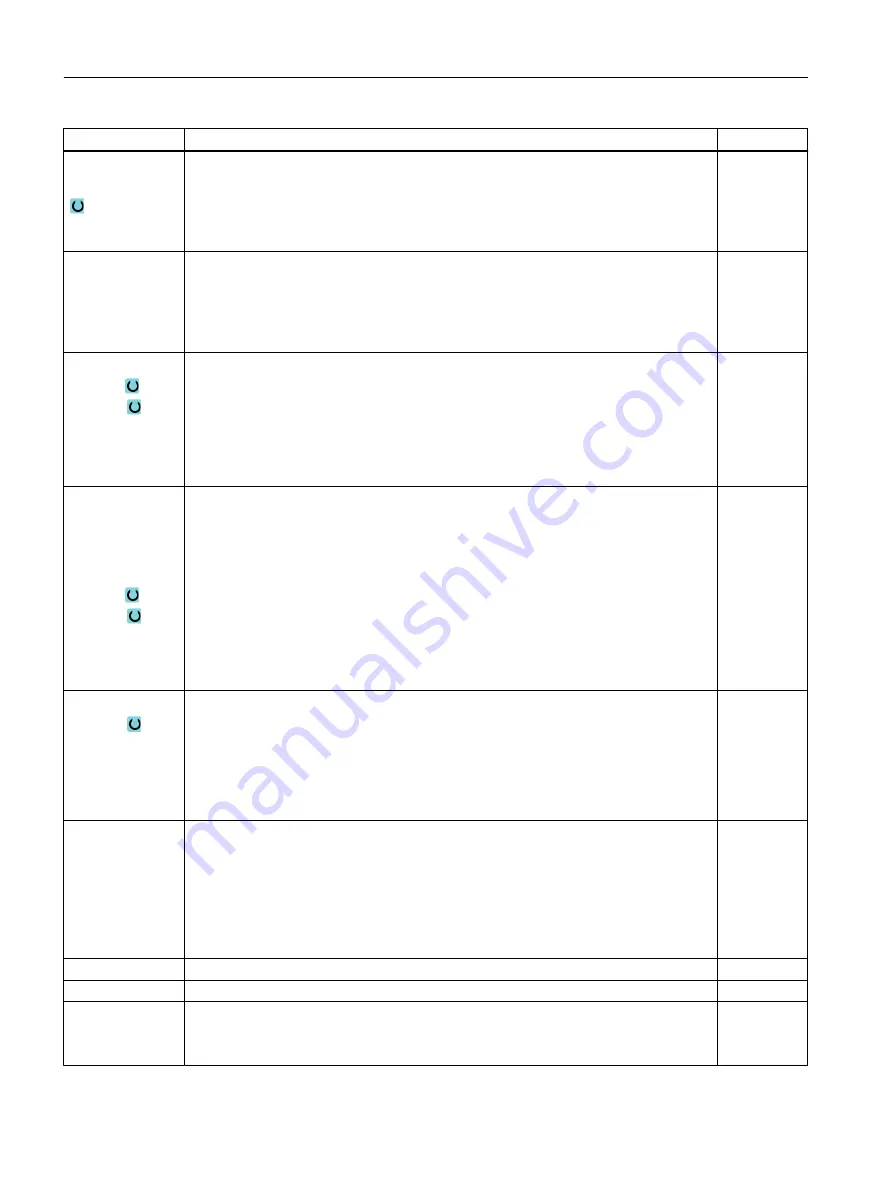
Parameter
Description
Unit
Machining
position
● Single position
A slot is milled at the programmed position (X0, Y0, Z0).
● Position pattern
Several slots are milled at the programmed position pattern (e.g. pitch circle, grid,
line).
X0
Y0
Z0
(only for G code)
The positions refer to the reference point:
Reference point X – (only for single position)
Reference point Y – (only for single position)
Reference point Z
mm
mm
mm
X0 or L0
Y0 or C0
Z0
(only for Shop‐
Turn)
Face C: The positions refer to the reference point:
Reference point X or reference point length polar – (only for single position)
Reference point Y or reference point angle polar – (only for single position)
Reference point Z – (only for single position)
mm
mm or de‐
grees
mm
CP
X0 or L0
Y0 or C0
Z0
(only for Shop‐
Turn)
Face Y: The positions refer to the reference point:
Positioning angle for machining area – (only single position)
Angle CP does not have any effect on the machining position in relation to the workpiece.
It is only used to position the workpiece with the rotary axis C in such a way that machining
is possible on the machine.
Reference point X or reference point length polar – (only for single position)
Reference point Y or reference point angle polar - (only for single position)
Reference point Z - (only for single position)
Degrees
mm
mm or de‐
grees
mm
Y0 or C0
Z0
X0
(only for Shop‐
Turn)
Peripheral surface C: The positions refer to the reference point:
Reference point Y or reference point angle polar - (only for single position)
Reference point Z - (only for single position)
Cylinder diameter ∅ – (only for single position)
mm or de‐
grees
mm
mm
C0
Y0
Z0
X0
(only for Shop‐
Turn)
Peripheral surface Y: The positions refer to the reference point:
Positioning angle for machining surface – (only for single position)
Reference point Y – (only for single position)
Reference point Z – (only for single position)
Reference point X – (only for single position)
Degrees
mm
mm
mm
W
Slot width
mm
L
Slot length
mm
α0
Angle of rotation of slot
Face: α0 refers to the X axis or to the position of C0 for a polar reference point
Peripheral surface: α0 refers to the Y axis
Degrees
Programming technology functions (cycles)
10.4 Milling
Turning
528
Operating Manual, 06/2019, A5E44903486B AB
Содержание SINUMERIK 840D sl
Страница 8: ...Preface Turning 8 Operating Manual 06 2019 A5E44903486B AB ...
Страница 70: ...Introduction 2 4 User interface Turning 70 Operating Manual 06 2019 A5E44903486B AB ...
Страница 274: ... Creating a G code program 8 8 Selection of the cycles via softkey Turning 274 Operating Manual 06 2019 A5E44903486B AB ...
Страница 275: ... Creating a G code program 8 8 Selection of the cycles via softkey Turning Operating Manual 06 2019 A5E44903486B AB 275 ...
Страница 282: ...Creating a G code program 8 10 Measuring cycle support Turning 282 Operating Manual 06 2019 A5E44903486B AB ...
Страница 344: ...Creating a ShopTurn program 9 19 Example Standard machining Turning 344 Operating Manual 06 2019 A5E44903486B AB ...
Страница 716: ...Collision avoidance 12 2 Set collision avoidance Turning 716 Operating Manual 06 2019 A5E44903486B AB ...
Страница 774: ...Tool management 13 15 Working with multitool Turning 774 Operating Manual 06 2019 A5E44903486B AB ...
Страница 834: ...Managing programs 14 19 RS 232 C Turning 834 Operating Manual 06 2019 A5E44903486B AB ...
Страница 856: ...Alarm error and system messages 15 9 Remote diagnostics Turning 856 Operating Manual 06 2019 A5E44903486B AB ...
Страница 892: ...Working with two tool carriers 18 2 Measure tool Turning 892 Operating Manual 06 2019 A5E44903486B AB ...
Страница 912: ...HT 8 840D sl only 20 5 Calibrating the touch panel Turning 912 Operating Manual 06 2019 A5E44903486B AB ...
Страница 927: ...Appendix A A 1 840D sl 828D documentation overview Turning Operating Manual 06 2019 A5E44903486B AB 927 ...