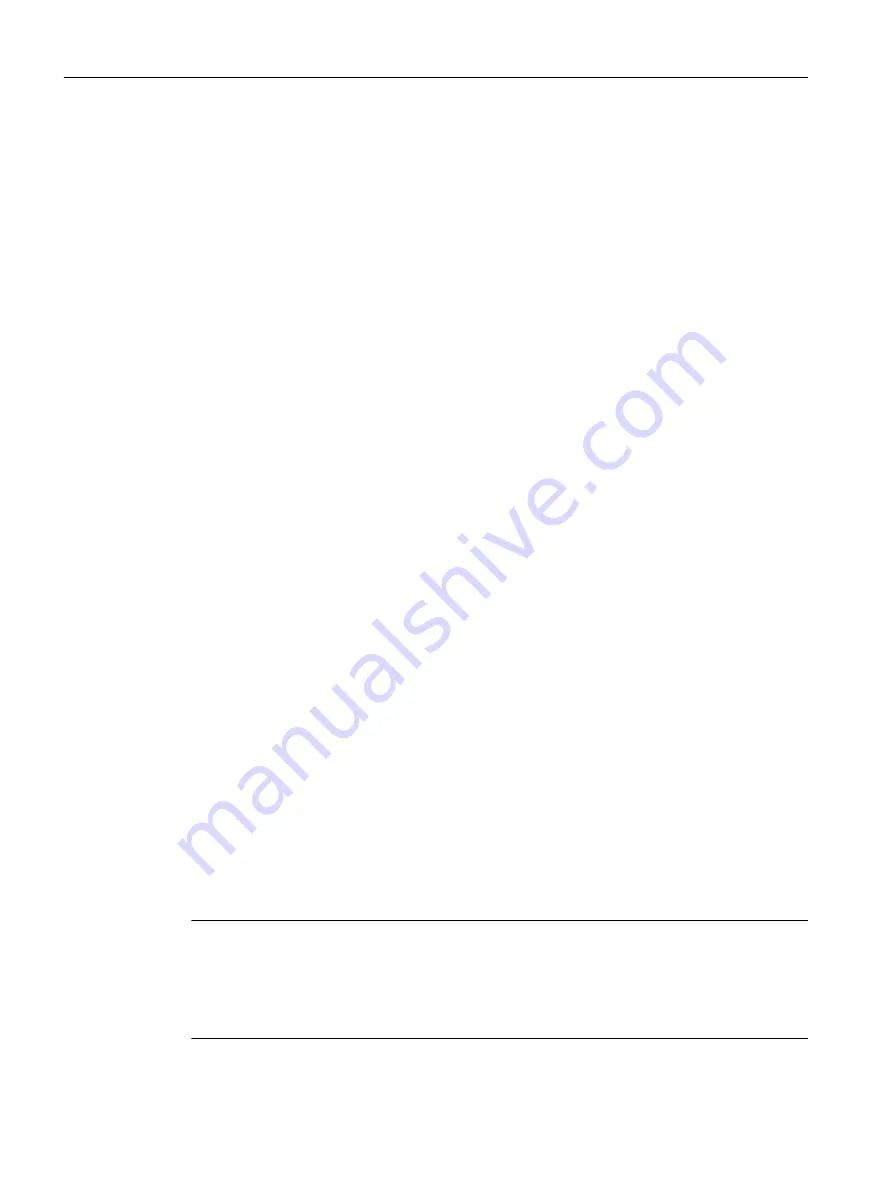
6.17
Setting for automatic mode
Before machining a workpiece, you can test the program in order to identify programming errors
at an early stage. Use the dry run feedrate for this purpose.
You have the option of additionally limiting the traversing speed so that when running-in a new
program with rapid traverse, no undesirably high traversing speeds occur.
Dry run feedrate
If you selected "DRY run feedrate" under program control, then the value entered in "Dry run
freedrate DRY” replaces the programmed feedrate when executing/machining.
Reduced rapid traverse
If you selected “RG0 reduced rapid traverse" under program control, then rapid traverse is
reduced to the percentage value entered in "reduced rapid traverse RG0”.
Displaying measurement results
Using an MMC command, measurement results can be displayed in a part program:
The following settings are possible:
● When it reaches the command, the control automatically jumps to the "Machine" operating
area and the window with the measurement results is displayed
● The window with the measurement results is opened by pressing the "Measurement result"
softkey.
Recording machining times
To provide support when creating and optimizing a program, you have the option of displaying
the machining times.
You define whether the time is determined while the workpiece is being machined (i.e. if the
function is energized).
● Off
Machining times are not determined when machining a workpiece. No machining times are
determined.
● Non-modal
The machining times are determined for each traversing block of a main program.
Note: You also have the option of displaying the cumulative times for blocks.
Please observe the information provided by the machine manufacturer.
● Block-by-block
Machining times are determined for all blocks.
Note
Utilization of resources
The more machining times are displayed, the more resources are utilized.
More machining times are determined and saved with the non-modal setting than with the
block-by-block setting.
Machining the workpiece
6.17 Setting for automatic mode
Turning
232
Operating Manual, 06/2019, A5E44903486B AB
Содержание SINUMERIK 840D sl
Страница 8: ...Preface Turning 8 Operating Manual 06 2019 A5E44903486B AB ...
Страница 70: ...Introduction 2 4 User interface Turning 70 Operating Manual 06 2019 A5E44903486B AB ...
Страница 274: ... Creating a G code program 8 8 Selection of the cycles via softkey Turning 274 Operating Manual 06 2019 A5E44903486B AB ...
Страница 275: ... Creating a G code program 8 8 Selection of the cycles via softkey Turning Operating Manual 06 2019 A5E44903486B AB 275 ...
Страница 282: ...Creating a G code program 8 10 Measuring cycle support Turning 282 Operating Manual 06 2019 A5E44903486B AB ...
Страница 344: ...Creating a ShopTurn program 9 19 Example Standard machining Turning 344 Operating Manual 06 2019 A5E44903486B AB ...
Страница 716: ...Collision avoidance 12 2 Set collision avoidance Turning 716 Operating Manual 06 2019 A5E44903486B AB ...
Страница 774: ...Tool management 13 15 Working with multitool Turning 774 Operating Manual 06 2019 A5E44903486B AB ...
Страница 834: ...Managing programs 14 19 RS 232 C Turning 834 Operating Manual 06 2019 A5E44903486B AB ...
Страница 856: ...Alarm error and system messages 15 9 Remote diagnostics Turning 856 Operating Manual 06 2019 A5E44903486B AB ...
Страница 892: ...Working with two tool carriers 18 2 Measure tool Turning 892 Operating Manual 06 2019 A5E44903486B AB ...
Страница 912: ...HT 8 840D sl only 20 5 Calibrating the touch panel Turning 912 Operating Manual 06 2019 A5E44903486B AB ...
Страница 927: ...Appendix A A 1 840D sl 828D documentation overview Turning Operating Manual 06 2019 A5E44903486B AB 927 ...