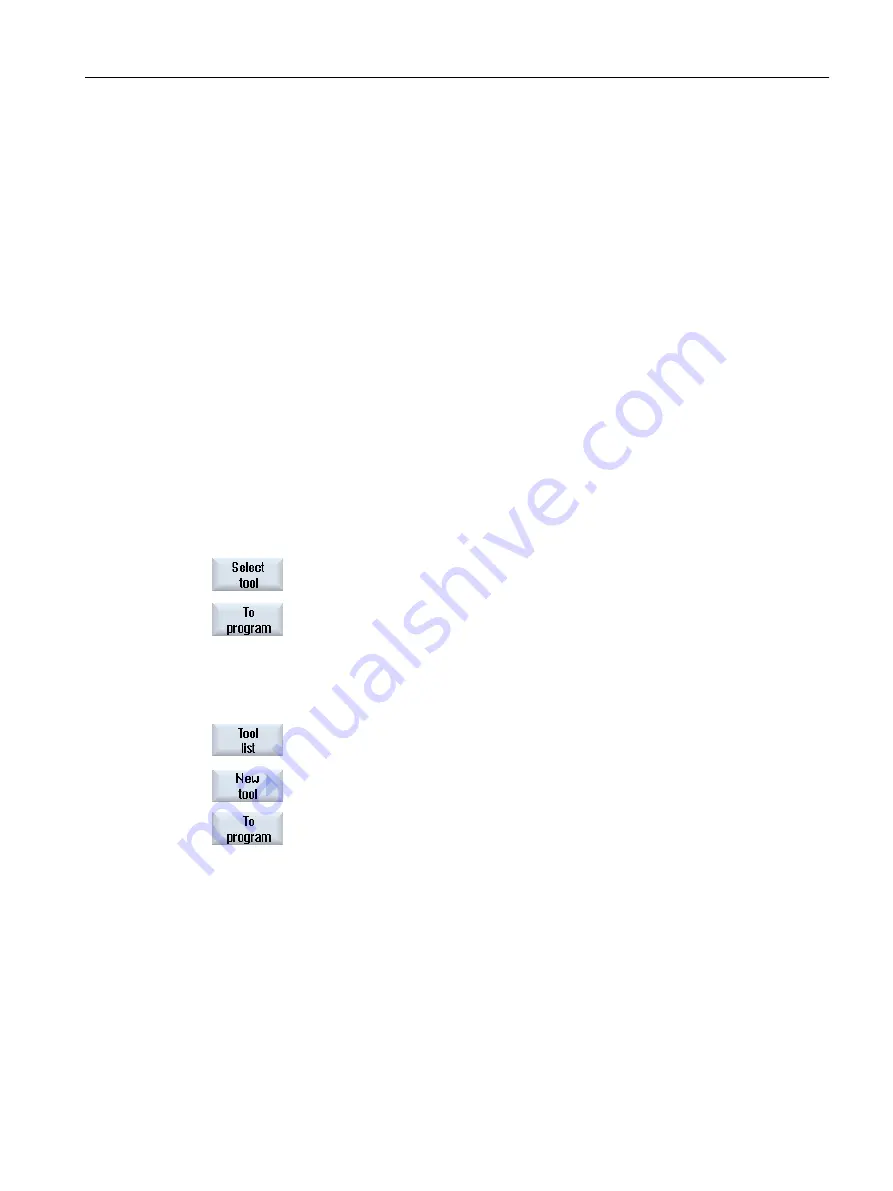
For G17, reference points in the plane are called X0 Y0, for G18 they are called Z0 X0 - and for
G19, they are called Y0 Z0. The depth specification in the tool axis for G17 is called Z1, for G18,
Y1 and for G19, X1.
If the entry field remains empty, the parameters, the help screens and the broken-line graphics
are displayed in the default plane (can be set via machine data):
● Turning: G18 (ZX)
● Milling: G17 (XY)
The plane is transferred to the cycles as new parameter. The plane is output in the cycle, i.e.
the cycle runs in the entered plane. It is also possible to leave the plane fields empty and thus
create a plane-independent program.
The entered plane only applies for this cycle (not modal)! At the end of the cycle, the plane from
the main program applies again. In this way, a new cycle can be inserted in a program without
having to change the plane for the remaining program.
8.4.3
Programming a tool (T)
Calling a tool
1.
You are in the part program.
2.
Press the "Select tool” softkey.
The "Tool selection" window is opened.
3.
Position the cursor on the desired tool and press the "To program" soft‐
key.
The selected tool is loaded into the G code editor. Text such as the fol‐
lowing is displayed at the current cursor position in the G code editor:
T="ROUGHINGTOOL100"
- OR -
4.
Press the "Tool list" and "New tool" softkeys.
5.
Then select the required tool using the softkeys on the vertical softkey
bar, parameterize it and then press the softkey "To program".
The selected tool is loaded into the G code editor.
6.
Then program the tool change (M6), the spindle direction (M3/M4), the
spindle speed (S...), the feedrate (F), the feedrate type (G94, G95,...), the
coolant (M7/M8) and, if required, further tool-specific functions.
Creating a G code program
8.4 Fundamentals
Turning
Operating Manual, 06/2019, A5E44903486B AB
267
Содержание SINUMERIK 840D sl
Страница 8: ...Preface Turning 8 Operating Manual 06 2019 A5E44903486B AB ...
Страница 70: ...Introduction 2 4 User interface Turning 70 Operating Manual 06 2019 A5E44903486B AB ...
Страница 274: ... Creating a G code program 8 8 Selection of the cycles via softkey Turning 274 Operating Manual 06 2019 A5E44903486B AB ...
Страница 275: ... Creating a G code program 8 8 Selection of the cycles via softkey Turning Operating Manual 06 2019 A5E44903486B AB 275 ...
Страница 282: ...Creating a G code program 8 10 Measuring cycle support Turning 282 Operating Manual 06 2019 A5E44903486B AB ...
Страница 344: ...Creating a ShopTurn program 9 19 Example Standard machining Turning 344 Operating Manual 06 2019 A5E44903486B AB ...
Страница 716: ...Collision avoidance 12 2 Set collision avoidance Turning 716 Operating Manual 06 2019 A5E44903486B AB ...
Страница 774: ...Tool management 13 15 Working with multitool Turning 774 Operating Manual 06 2019 A5E44903486B AB ...
Страница 834: ...Managing programs 14 19 RS 232 C Turning 834 Operating Manual 06 2019 A5E44903486B AB ...
Страница 856: ...Alarm error and system messages 15 9 Remote diagnostics Turning 856 Operating Manual 06 2019 A5E44903486B AB ...
Страница 892: ...Working with two tool carriers 18 2 Measure tool Turning 892 Operating Manual 06 2019 A5E44903486B AB ...
Страница 912: ...HT 8 840D sl only 20 5 Calibrating the touch panel Turning 912 Operating Manual 06 2019 A5E44903486B AB ...
Страница 927: ...Appendix A A 1 840D sl 828D documentation overview Turning Operating Manual 06 2019 A5E44903486B AB 927 ...