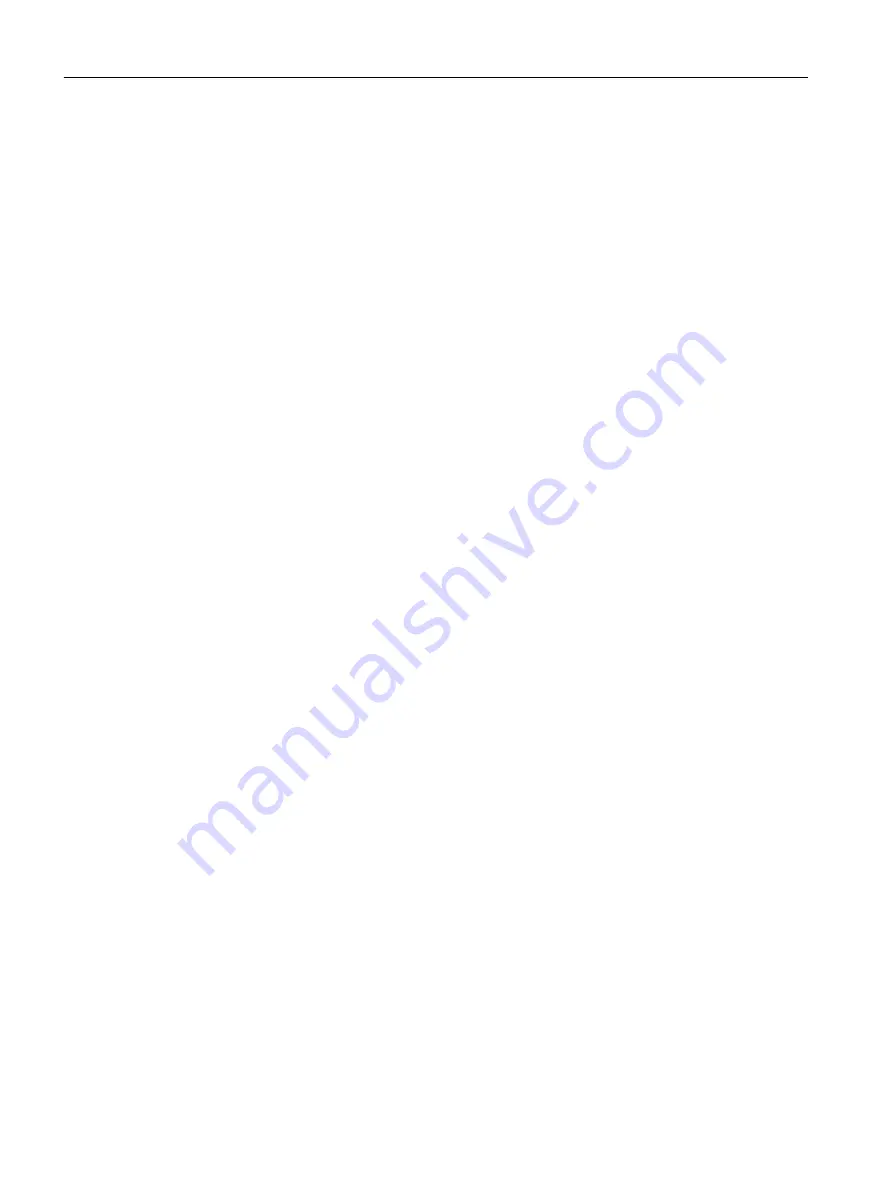
Approach/retraction when milling internal threads
1. Positioning on retraction plane with rapid traverse.
2. Approach of starting point of the approach circle in the current plane with rapid traverse.
3. Infeed to a starting point in the tool axis calculated internally in the controller with rapid
traverse.
4. Approach motion to thread diameter on an approach circle calculated internally in the
controller with the programmed feedrate, taking into account the finishing allowance and
maximum plane infeed.
5. Thread cutting along a spiral path in clockwise or counter-clockwise direction (depending on
whether it is left-hand/right-hand thread, for number of cutting teeth of a milling plate (NT) ≥
2 only one rotation, offset in the Z direction).
To reach the programmed thread length, traversing is beyond the Z1 value for different
distances depending on the thread parameters.
6. Exit motion along a circular path in the same rotational direction at programmed feedrate.
7. With a programmed number of threads per cutting edge NT > 2, the tool is fed in (offset) by
the amount NT-1 in the Z direction. Points 4 to 7 are repeated until the programmed thread
depth is reached.
8. If the plane infeed is less than the thread depth, points 3 to 7 are repeated until the thread
depth + programmed allowance is reached.
9. Retraction on the retraction plane in the tool axis with rapid traverse.
10.Rapid traverse thread center point approach with position pattern (MCALL).
Please note that when milling an internal thread the tool must not exceed the following value:
Milling cutter diameter < (nominal diameter - 2 · thread depth H1)
Approach/retraction when milling external threads
1. Positioning on retraction plane with rapid traverse.
2. Approach of starting point of the approach circle in the current plane with rapid traverse.
3. Infeed to a starting point in the tool axis calculated internally in the controller with rapid
traverse.
4. Approach motion to thread core diameter on an approach circle calculated internally in the
controller with the programmed feedrate, taking into account the finishing allowance and
maximum plane infeed.
5. Cut thread along a spiral path in clockwise or counter-clockwise direction (depending on
whether it is left-hand/right-hand thread, with NT ≥ 2 only one rotation, offset in Z direction).
To reach the programmed thread length, traversing is beyond the Z1 value for different
distances depending on the thread parameters.
6. Exit motion along a circular path in opposite rotational direction at programmed feedrate.
7. With a programmed number of threads per cutting edge NT > 2, the tool is fed in (offset) by
the amount NT-1 in the Z direction. Points 4 to 7 are repeated until the programmed thread
depth is reached.
Programming technology functions (cycles)
10.4 Milling
Turning
554
Operating Manual, 06/2019, A5E44903486B AB
Содержание SINUMERIK 840D sl
Страница 8: ...Preface Turning 8 Operating Manual 06 2019 A5E44903486B AB ...
Страница 70: ...Introduction 2 4 User interface Turning 70 Operating Manual 06 2019 A5E44903486B AB ...
Страница 274: ... Creating a G code program 8 8 Selection of the cycles via softkey Turning 274 Operating Manual 06 2019 A5E44903486B AB ...
Страница 275: ... Creating a G code program 8 8 Selection of the cycles via softkey Turning Operating Manual 06 2019 A5E44903486B AB 275 ...
Страница 282: ...Creating a G code program 8 10 Measuring cycle support Turning 282 Operating Manual 06 2019 A5E44903486B AB ...
Страница 344: ...Creating a ShopTurn program 9 19 Example Standard machining Turning 344 Operating Manual 06 2019 A5E44903486B AB ...
Страница 716: ...Collision avoidance 12 2 Set collision avoidance Turning 716 Operating Manual 06 2019 A5E44903486B AB ...
Страница 774: ...Tool management 13 15 Working with multitool Turning 774 Operating Manual 06 2019 A5E44903486B AB ...
Страница 834: ...Managing programs 14 19 RS 232 C Turning 834 Operating Manual 06 2019 A5E44903486B AB ...
Страница 856: ...Alarm error and system messages 15 9 Remote diagnostics Turning 856 Operating Manual 06 2019 A5E44903486B AB ...
Страница 892: ...Working with two tool carriers 18 2 Measure tool Turning 892 Operating Manual 06 2019 A5E44903486B AB ...
Страница 912: ...HT 8 840D sl only 20 5 Calibrating the touch panel Turning 912 Operating Manual 06 2019 A5E44903486B AB ...
Страница 927: ...Appendix A A 1 840D sl 828D documentation overview Turning Operating Manual 06 2019 A5E44903486B AB 927 ...