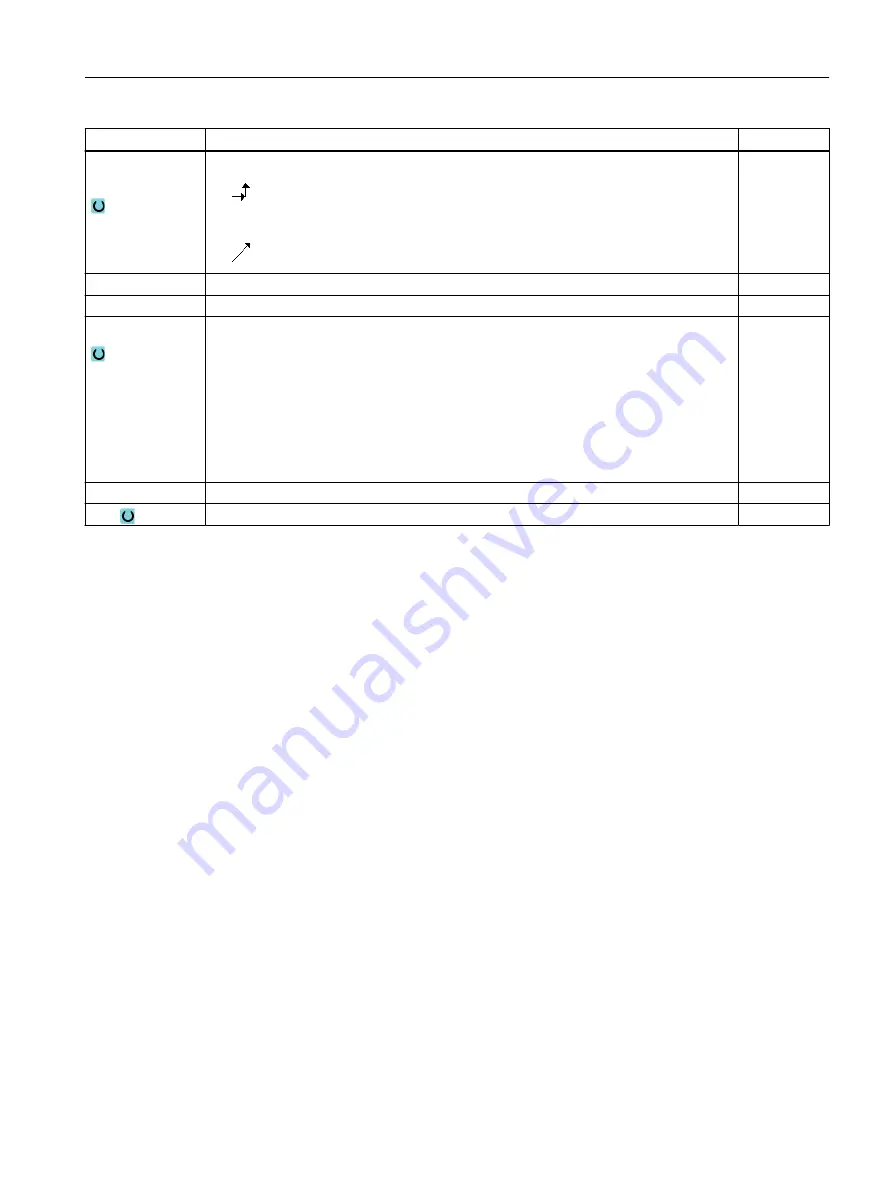
Parameter
Description
Unit
Retraction strat‐
egy
● axis-by-axis
● spatial
R2
Retraction radius - (only for "quadrant or semi-circle" retraction)
mm
L2
Retraction distance - (only for "straight line" retraction)
mm
Lift mode
If more than one depth infeed is necessary, specify the retraction height to which the tool
retracts between the individual infeeds (at the transition from the end of the contour to the
start).
Lift mode before new infeed
● No retraction
● to RP
● Z0 + safety clearance
● By the safety clearance
FS
Chamfer width for chamfering - (only for chamfering machining)
mm
ZFS
Insertion depth of tool tip (abs or inc) - (for chamfering machining only)
mm
* Unit of feedrate as programmed before the cycle call
10.5.8
Contour pocket/contour spigot (CYCLE63/64)
Contours for pockets or islands
Contours for pockets or islands must be closed, i.e. the starting point and end point of the
contour are identical. You can also mill pockets that contain one or more islands. The islands
can also be located partially outside the pocket or overlap each other. The first contour you
specify is interpreted as the pocket contour and all the others as islands.
Automatic calculation / manual input of the starting point
Using "Automatic starting point" you have the option of calculating the optimum plunge point.
By selecting "Manual starting point", you define the plunge point in the parameter screen.
If the islands and the miller diameter, which must be plunged at various locations, are obtained
from the pocket contour, then the manual entry only defines the first plunge point; the remaining
plunge points are automatically calculated.
Contours for spigots
Contours for spigots must be closed, i.e. the starting point and end point of the contour are
identical. You can define multiple spigots that can also overlap. The first contour specified is
interpreted as a blank contour and all others as spigots.
Programming technology functions (cycles)
10.5 Contour milling
Turning
Operating Manual, 06/2019, A5E44903486B AB
581
Содержание SINUMERIK 840D sl
Страница 8: ...Preface Turning 8 Operating Manual 06 2019 A5E44903486B AB ...
Страница 70: ...Introduction 2 4 User interface Turning 70 Operating Manual 06 2019 A5E44903486B AB ...
Страница 274: ... Creating a G code program 8 8 Selection of the cycles via softkey Turning 274 Operating Manual 06 2019 A5E44903486B AB ...
Страница 275: ... Creating a G code program 8 8 Selection of the cycles via softkey Turning Operating Manual 06 2019 A5E44903486B AB 275 ...
Страница 282: ...Creating a G code program 8 10 Measuring cycle support Turning 282 Operating Manual 06 2019 A5E44903486B AB ...
Страница 344: ...Creating a ShopTurn program 9 19 Example Standard machining Turning 344 Operating Manual 06 2019 A5E44903486B AB ...
Страница 716: ...Collision avoidance 12 2 Set collision avoidance Turning 716 Operating Manual 06 2019 A5E44903486B AB ...
Страница 774: ...Tool management 13 15 Working with multitool Turning 774 Operating Manual 06 2019 A5E44903486B AB ...
Страница 834: ...Managing programs 14 19 RS 232 C Turning 834 Operating Manual 06 2019 A5E44903486B AB ...
Страница 856: ...Alarm error and system messages 15 9 Remote diagnostics Turning 856 Operating Manual 06 2019 A5E44903486B AB ...
Страница 892: ...Working with two tool carriers 18 2 Measure tool Turning 892 Operating Manual 06 2019 A5E44903486B AB ...
Страница 912: ...HT 8 840D sl only 20 5 Calibrating the touch panel Turning 912 Operating Manual 06 2019 A5E44903486B AB ...
Страница 927: ...Appendix A A 1 840D sl 828D documentation overview Turning Operating Manual 06 2019 A5E44903486B AB 927 ...