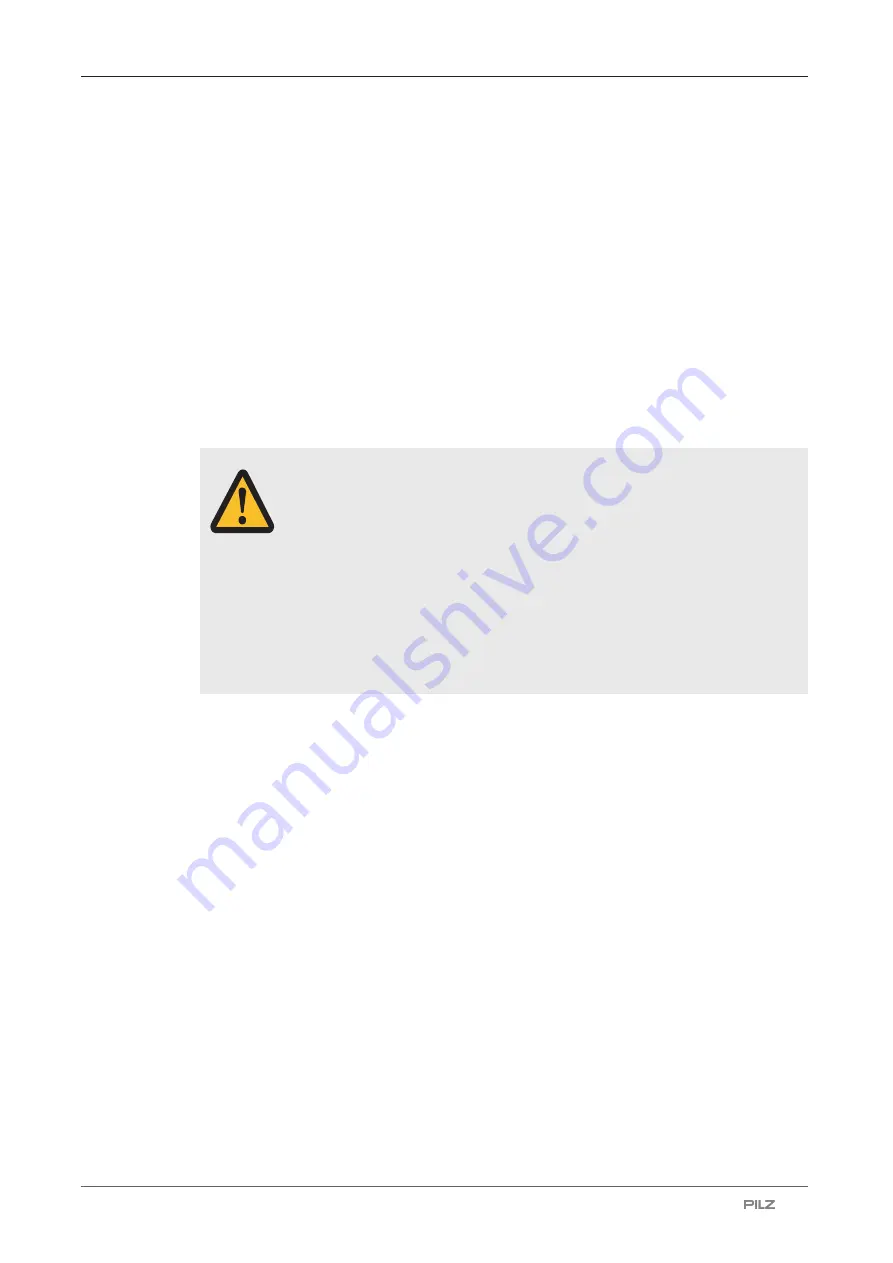
Commissioning
System Description Service Robotics Modules
1004870-EN-05
| 98
This includes, in particular:
– Test dual-channel emergency stop and protective stop for errors in one channel
– Test emergency stop pushbutton on teach pendant and any potential external emer-
gency stop pushbuttons
– Simulate shorts between contacts
– Simulate short circuits and open circuits;
in particular short circuits and open circuits should be simulated on the STO lines!
– Simulate faults on the external safeguard(s)
– Test holding brakes by triggering a brake test
– Check that a safe state is achieved in the event of a fault and that the STO-LED on
the foot of the robot arm lights up red.
– Check behaviour in the event of a power failure
CAUTION!
Injury and/or material damage caused by insufficient safety distances
If the risk assessment shows that the validity of the calculated values for
stopping time/overrun distance must be verified, the values must be valid-
ated by means of suitable measurements. Depending on the application, in-
jury or material damage may occur if the calculated values for stopping
time/overrun distance are not validated.
The system or plant integrator must ensure that the values calculated in the-
ory for the stopping time/overrun distance are validated.
}
Log the performed tests
}
Carry out setup work with the teach pendant
Always
execute new or modified robot programs in the operating mode "Manual reduced
speed".
Please note:
– Before starting the setup work, the person performing the setup work must ensure
that the devices required to control the enable operate in accordance with
EN 60204-1:2006. All persons in the area of the setup work must have a device for
controlling the enable (enabling device).
– As far as possible, setup work must be performed in the safe area outside the safe-
guards.
– The person performing the setup work must be able to view the danger zone and
avoid a danger, where applicable.
– Avoid having several people present in the protected area if possible.
– If several people are present in the protected area (and must be so), special addi-
tional protective measures must be met:
– No person’s view of the robot arm may be blocked.
– People must be able to maintain constant eye contact.