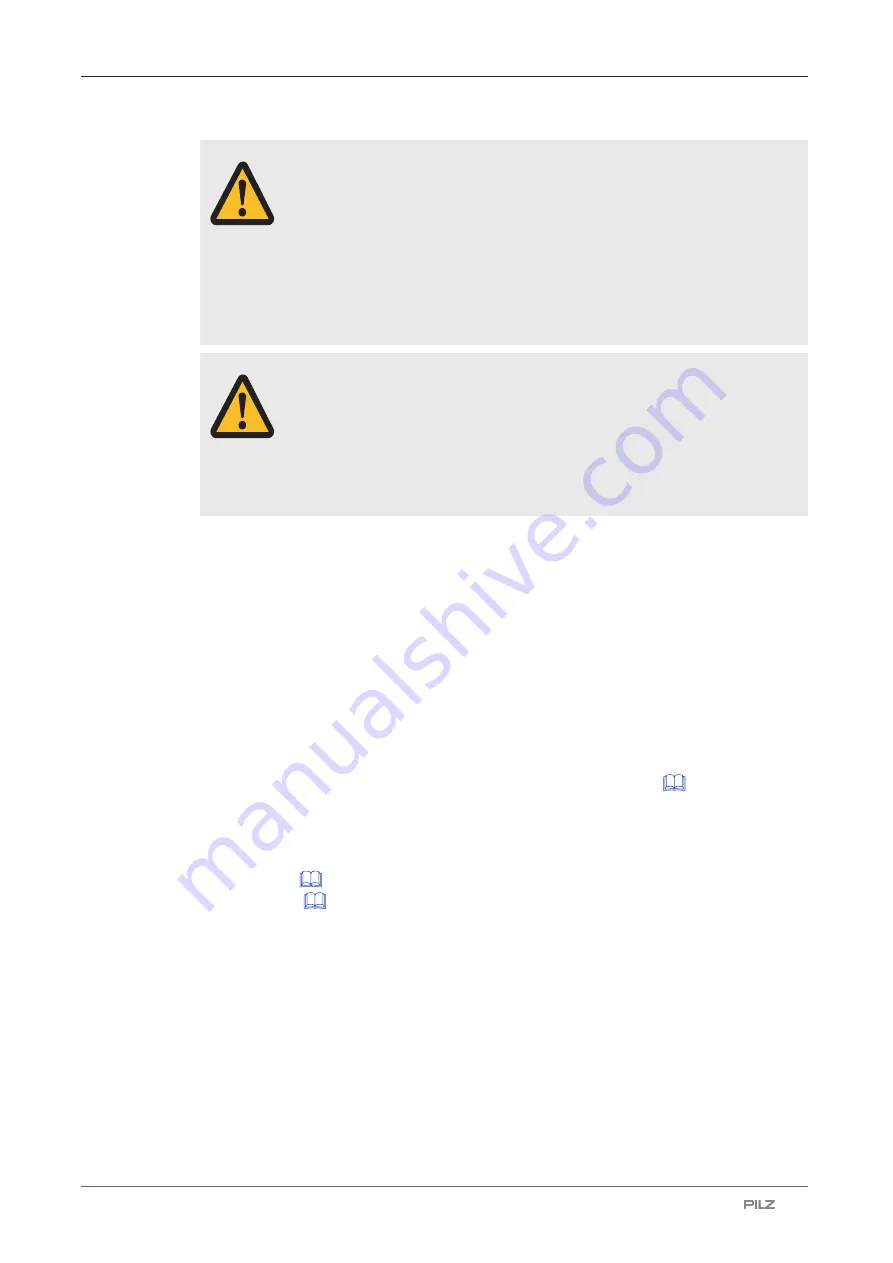
Commissioning
System Description Service Robotics Modules
1004870-EN-05
| 99
CAUTION!
Damage to the robot arm caused by collision with obstacles
Upon moving the axes, the robot arm or end-effector must never collide with
any obstacles such as barriers, otherwise material damage may occur and
the robot arm may be damaged.
Ensure that the robot arm never collides with obstacles. Also make sure that
a damaged robot arm is
not
taken into operation.
CAUTION!
Injury and/or material damage caused by reaching over barriers
Upon moving the axes, the robot arm or end-effector must never reach over
a barrier. Otherwise injury and/or material damage may occur.
Ensure that the robot arm
never
reaches over barriers.
}
Test the safety devices in automatic operating mode
– Ensure that all emergency stop pushbuttons are unlocked.
– Ensure that all safety gates are closed.
– Switch to the operating mode "Automatic" with teach pendant.
– Operate the reset button on the teach pendant (“2nd” button) to request the motion
enable.
– Test the emergency stop function.
Operate the emergency stop pushbutton on the teach pendant. This must trigger the
emergency stop function. Repeat this test for all available emergency stop devices.
Further information is available under
.
– Test all available safety devices, such as safety gates for example.
Operate the safety device. This must trigger the protective stop function. Further in-
formation is available under
Protective stop function for protective stop
external [
Protective stop function for PSENmlock (safety gate
.
}
Intended operation
As soon as all the tests are completed and there are no faults present, it is possible to
start the intended operation with or without the teach pendant, depending on the applica-
tion (operating mode "Automatic" with teach pendant or operating mode "Automatic" with
external controller).