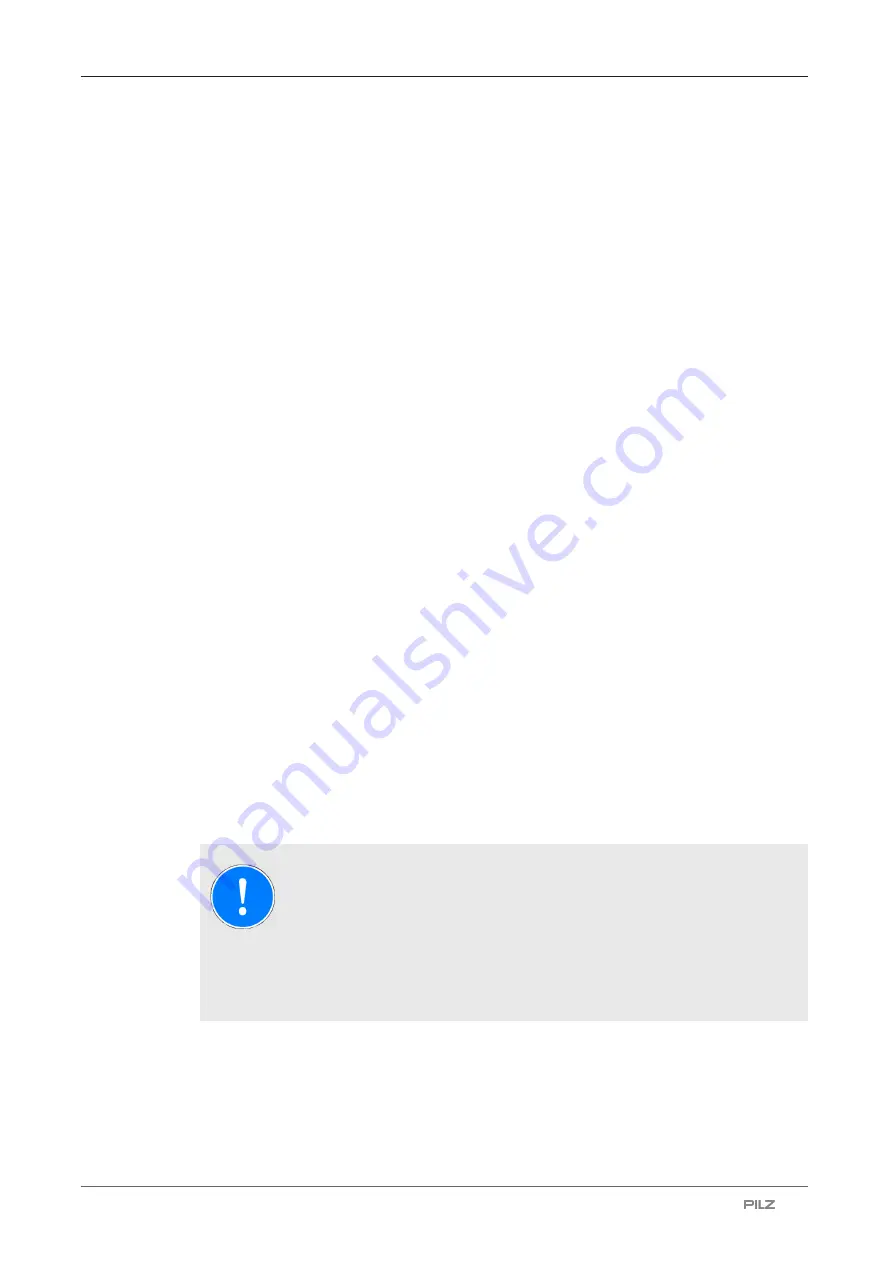
Commissioning
System Description Service Robotics Modules
1004870-EN-05
| 97
9
Commissioning
The system or plant integrator is obligated to define the requirements for the (initial) com-
missioning and recommissioning of the robot arm depending on the application.
Note the following, for example:
}
Secure the site in accordance with the regulations (barrier, warning signs etc.). The sys-
tem may only be commissioned/recommissioned by competent persons.
}
Please refer to the information and specifications stated in the relevant documentation.
}
During commissioning/recommissioning, make sure that no personal injury and/or mater-
ial damage can occur, even if the plant/machine should move unintentionally (e.g. phys-
ical barrier for the danger zone or for the whole plant/machine if necessary).
9.1
Initial commissioning
Prerequisites
}
The robot arm is properly set up and safely mounted. The requirements from the operat-
ing manual for the robot arm PRBT 6 have been adhered to.
}
The robot control module (control cabinet) has been set up properly. The requirements
from the operating manual for the robot control module PRCM1 have been adhered to.
}
The robot arm is wired properly. The requirements from the "Wiring" section, the operat-
ing manual for the robot arm PRBT 6 and the operating manual for the robot control mod-
ule PRCM1 have been adhered to.
}
The connection cable for the teach pendant PRTM1 is connected to the robot control
module.
}
The power cable (supply voltage) is plugged in.
}
The safety requirements resulting from the risk assessment have been implemented.
Procedure
}
Perform a visual inspection
Ensure that there are no foreign bodies or defective or loose parts on the robot arm or
end-effector.
}
Switch on the control cabinet main switch
NOTICE
(Re-)commissioning at very low ambient temperatures
If (re-)commissioning is to take place at very low ambient temperatures (0°C
… 5°C), you should leave the robot arm at a controlled stop for 10 minutes
before moving the axes. This is recommended particularly for operation with
high load.
}
Completely check safety devices and fault detection mechanisms.
Test the safety functions using the safety plan that resulted from the safety analysis. The
tests must be performed in one of the manual operating modes.
You will find the general and complete table for the verification of safety requirements and
measures in EN ISO 10218-2 Annex G.