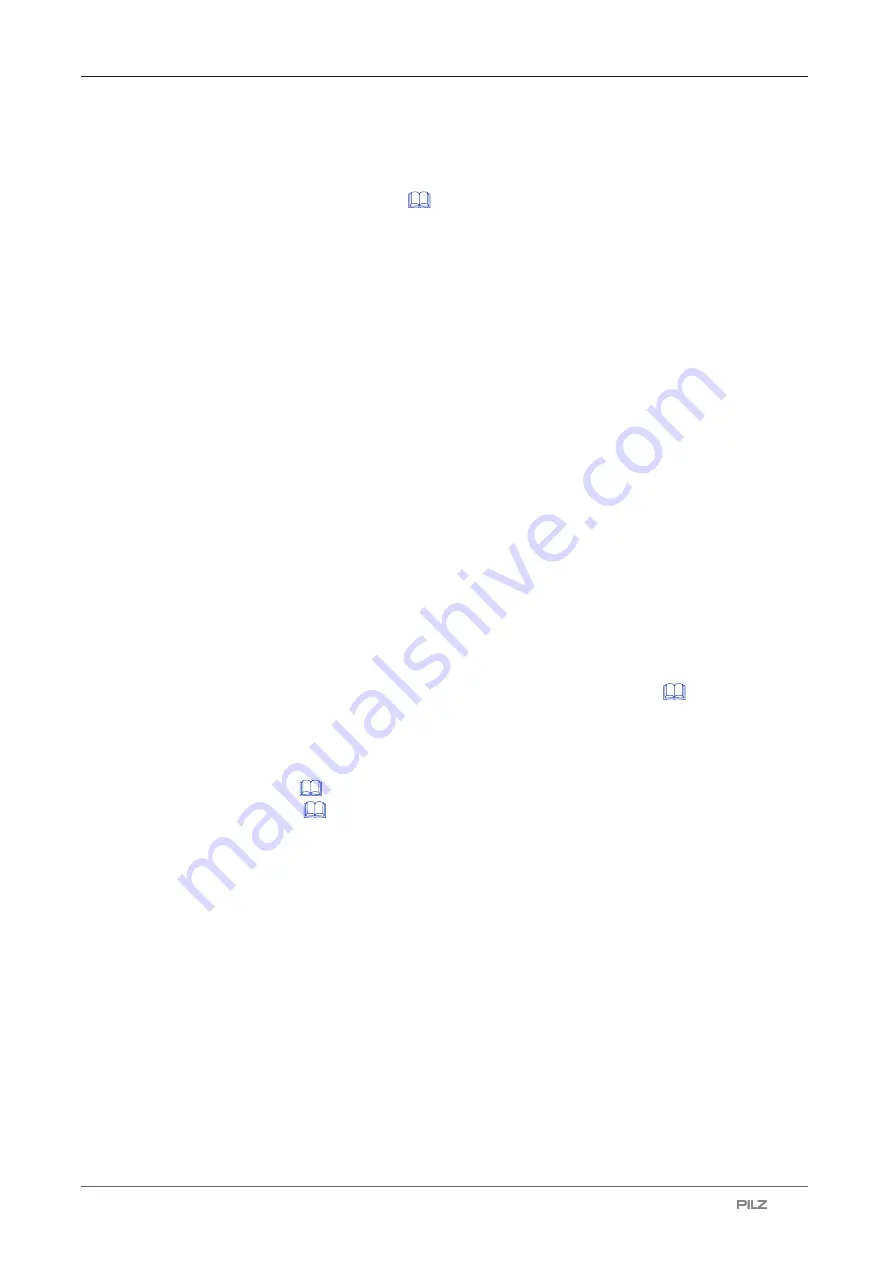
Commissioning
System Description Service Robotics Modules
1004870-EN-05
| 100
9.2
Recommissioning
Recommissioning is always necessary when a change has been made to the plant/ma-
Prerequisites
}
The safety requirements resulting from the risk assessment have been implemented.
}
The assembly and wiring of the modified components have been tested based on the
specific assembly instructions and wiring diagram for the plant/machinery.
Procedure
}
Switch on the robot at the control cabinet main switch.
}
Test the safety functions
Following a change, if the safety analysis has shown that safety functions need to be val-
idated and tested, the change itself must be tested, as must the course of the entire pro-
cess. The tests must be performed in one of the manual operating modes.
}
Test the safety devices in automatic operating mode
– Ensure that all emergency stop pushbuttons are unlocked.
– Ensure that all safety gates are closed.
– Switch to the operating mode "Automatic" with teach pendant.
– Operate the reset button on the teach pendant (“2nd” button) to request the motion
enable.
– Test the emergency stop function.
Operate the emergency stop pushbutton on the teach pendant. This must trigger the
emergency stop function. Repeat this test for all available emergency stop devices.
Further information is available under
.
– Test all available safety devices, such as safety gates for example.
Operate the safety device. This must trigger the protective stop function. Further in-
formation is available under
Protective stop function for protective stop
external [
Protective stop function for PSENmlock (safety gate
.
}
Intended operation
As soon as all the tests are completed and there are no faults present, it is possible to
start the intended operation with or without the teach pendant, depending on the applica-
tion (operating mode "Automatic" with teach pendant or operating mode "Automatic" with
external controller).