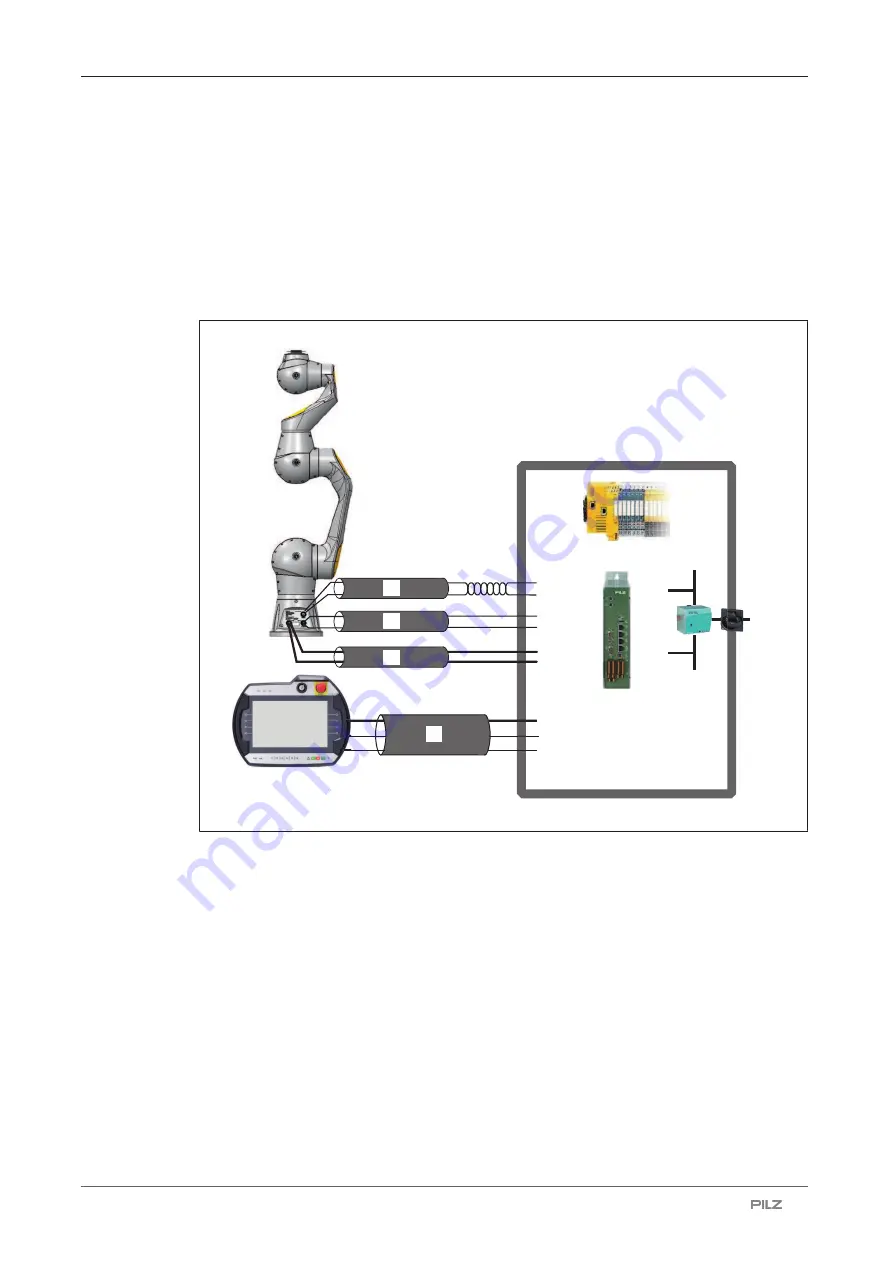
Overview
System Description Service Robotics Modules
1004870-EN-05
| 8
2
Overview
2.1
Overview of industrial robots with service robotics modules
from Pilz
Using the robot arm PRBT 6 together with the robot control module PRCM1 (control cab-
inet) and the teach pendant PRTM1, an industrial robot can be built that corresponds to the
harmonised standard EN ISO 10218-1.
[1]
[2]
[3]
Safety control system
Motion controller
Ethernet
- Enable signal for operating mode selection
- Emergency stop signal
- Enabling signal
STO
CANopen
24 VDC
24 VDC
Robot arm
End-effector
X1 (Power)
[4]
[5]
[7]
X3 (AUX)
[6]
X2 (Signals)
230 VAC
Fig.: Industrial robots with service robotics modules from Pilz
Legend
[1]
Robot arm PRBT 6 with
}
Inputs for triggering STO and SBC via two separate shutdown paths
}
Flange for attachment of a suitable end-effector
}
Communication interface (CANopen) for controlling the axes and the end-effector
[2]
Teach pendant PRTM1 with
}
Software from Pilz for programming, commissioning and diagnostics of the Pilz in-
dustrial robots
}
Key switch to release the operating mode selection
}
Emergency stop pushbutton
}
Enabling device (3-stage) for the manual operating modes