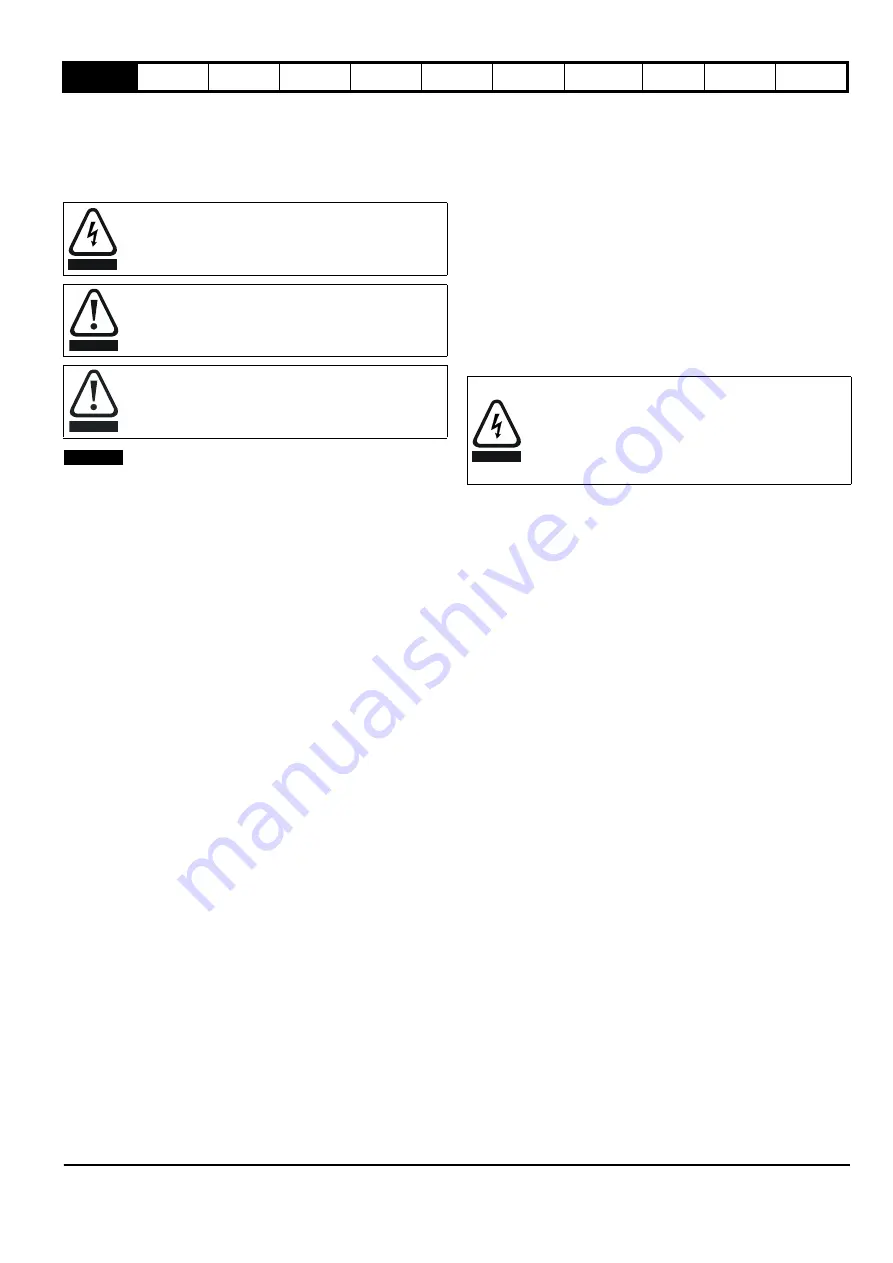
Communications Diagnostics Technical data
Commander S100 User Guide
5
1 Safety information
1.1 Important safety information
Specific warnings are given at the relevant places in this User Guide as
follows:
A Note contains information which helps to ensure correct operation of
the product.
1.1.1 Hazards
This User Guide applies to the Commander S100 which are Basic Drive
Modules (BDM) and auxiliary equipment. All safety information within
this guide must be observed. In all applications the hazards associated
with powerful electrical drive is present.
1.2 Responsibility
It is the responsibility of the installer to ensure the safety of the complete
Power Drive System (PDS), so as to avoid the risk of injury in normal
operation, in the event of a fault and of reasonably foreseeable misuse.
The manufacturer of the BDM drive accepts no liability for any
consequences resulting from inappropriate, negligent, or incorrect
system design and installation or as a result of drive failure.
Drives are intended as components for professional incorporation into
complete systems. The drive uses high voltages and currents, has a
high level of stored electrical energy, and is used to control equipment
which can cause injury and generate excessive acoustic noise. If
installed incorrectly the drive may present a safety hazard.
System design, installation, commissioning, start-up and maintenance
must be carried out by personnel with the necessary training and
competence who must read all of the safety information and instructions
in this User Guide.
1.3 Compliance with regulations
The installer is responsible of ensuring that the PDS complies with all
applicable laws, regulations, and codes in the country where it is to be
used, including but not limited to the following:
UK Electrical Equipment (Safety) Regulations 2016
EU Low Voltage Directive 2014/35
UK Electromagnetic Compatibility Regulations 2016
EU Electromagnetic Compatibility Directive 2014/30/EU
UK Supply of Machinery (Safety) Regulations 2008
EU Machinery Directive 2006/42/EC
USA National Electric Code (NEC)
Canadian Electrical Code.
Particular attention must be given to the cross-sectional areas of
conductors, the selection of fuses or other protection, and protective
ground (earth) connections. This guide contains instructions for
achieving compliance with specific EMC standards.
1.4 Electrical hazards
The voltages used in the drive can cause severe electrical shock and/or
burns and could be lethal. Care is necessary when working with or
adjacent to the drive. Hazardous voltage may be present in any of the
following locations:
•
A.C. supply cables and connections
•
Motor cables and connections
•
Relay cable and connections
•
Many internal parts of the drive.
No commands remove dangerous voltages from the drive or motor. E.g.
stop, rdy or inh.
1.4.1 Mechanical to electrical energy
Unsafe voltages can be present on the drive even with the A.C. supply
disconnected if the motor shaft is mechanically driven by another source
of power.
1.4.2 Stored electrical charge
1.4.3 Products connected by plug and socket
If a plug and socket are used to connect the PDS / BDM to the supply,
the plug should conform to IEC60309.
A hazard may exist where the drive is incorporated into a product which
is connected to the supply by a plug and socket. When unplugged, the
pins of the plug may be connected to the drive supply, which is
separated from the charge stored in the capacitor only by semiconductor
devices. A means must be provided for automatically isolating the plug
from the drive - e.g. a contactor, or the use of shrouded pins.
It is recommended to remove the EMC filter disconnect screw and fit a
type B RCB fitted on the drive side of the plug.
1.5 Mechanical hazards
In any application where a malfunction of the drive or its control system
could lead to or allow damage, loss, or injury, a risk analysis must be
carried out, and where necessary, further measures taken to reduce the
risk. For example, an over-speed protection device in case of failure of
the speed control, or a fail-safe mechanical brake in case of loss of
motor braking. None of the drive functions should be used to ensure
safety of personnel.
1.6 Motor
The safety of the motor under variable speed conditions must be
ensured. To avoid the risk of physical injury, do not exceed the maximum
specified speed of the motor.
Low speeds may cause the motor to overheat because the cooling fan
becomes less effective, causing a fire hazard. The motor should be
installed with a protection thermistor. If necessary, an electric forced vent
fan should be used.
The values of the motor parameters set in the drive affect the protection
of the motor. The default values in the drive must not be relied upon. It
is essential that the correct value is entered in the Motor Rated Current
parameter from the motor nameplate.
The drive has electronic motor overload protection and typical overloads
are 150 % for 60 s (from cold) or 150 % for 8 s (from hot). The protection
includes speed sensitivity and thermal memory retention through power
cycle and disable. See
Thermal Protection Action
(P3.21) for details.
This type of warning contains information which is essential
for avoiding an electric shock.
This type of warning contains information which is essential
for avoiding a safety hazard.
A Caution contains information which is necessary for
avoiding a risk of damage to the product or other equipment.
WARNING
WARNING
CAUTION
NOTE
Risk of Electric Shock.
The drive contains capacitors that remain charged to a
potentially lethal voltage after the A.C. supply has been
disconnected. If the drive has been energized, the A.C.
supply must be isolated for at least 5 minutes before work
may continue. In the event of a failure the stored charge could
remain longer.
WARNING
Содержание COMMANDER S100
Страница 118: ...0478 0650 02...