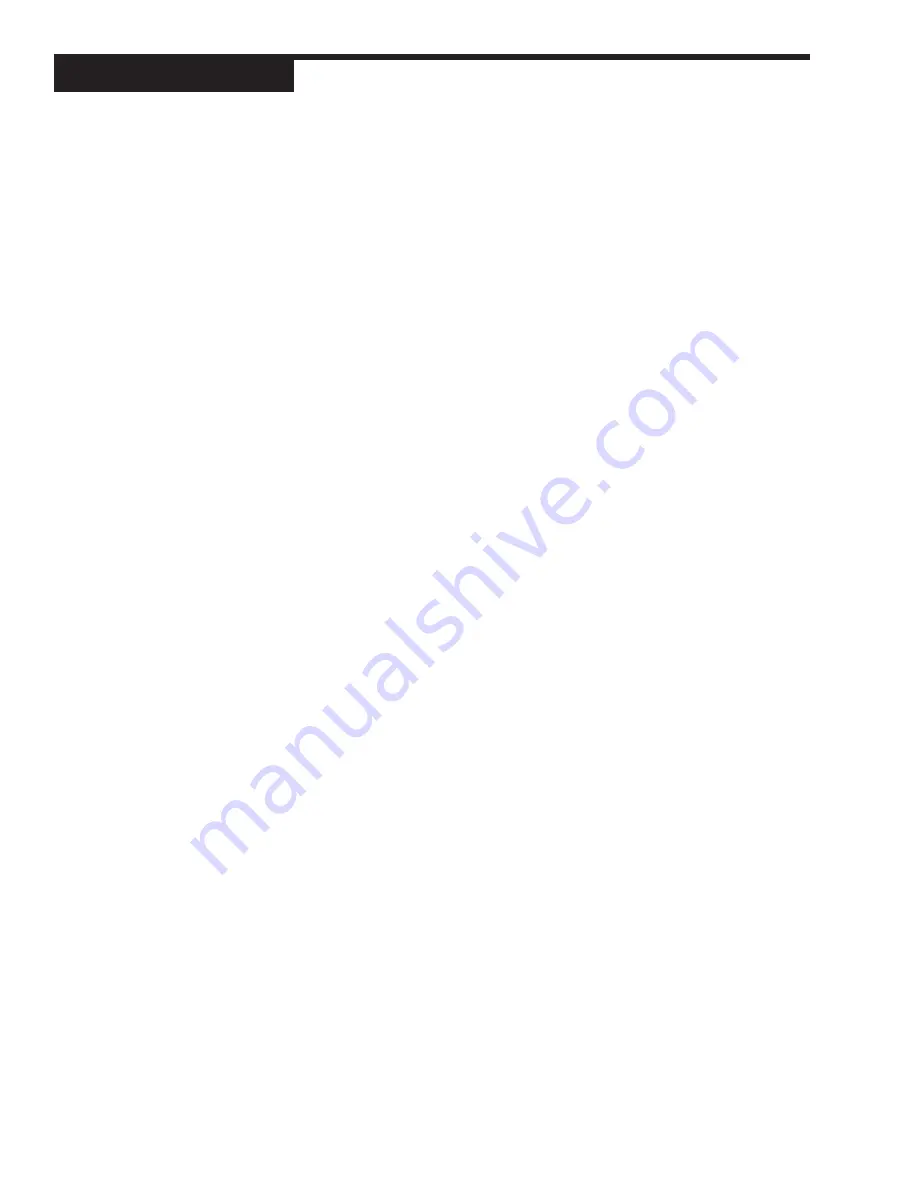
90
Chapter 7
535-PROF User's Manual
Applications
B. If the alarm setpoint is set to 100 and the time base set to 10, the rate
of change is also 10 units per second.
In example A, the process variable would only have to experience a ten
unit change over a short period of time, while in Example B, it would re-
quire a 100 unit change over a ten second period. Example A is much
more sensitive than Example B. In general, for a given rate-of-change,
the shorter the time period, the more sensitive the rate alarm.
D. DUPLEX CONTROL
The Duplex control algorithm enables two discrete control outputs for the control
loop. Duplex control is commonly used for applications that require both heating
and cooling or when 2 control elements are needed to achieve the desired result.
Hardware Configuration
•
The controller must have two output modules assigned to the loop (any
combination of output modules).
Software Configuration
1. Go to the
CONFIG
. menu.
Set
CTRL.TYPE
to DUPLEX.
2. To use different algorithms for each output (PID for the first, and On/Off for
the second):
Go to the
CONTROL
menu.
Set
ALGORITHM
to PID:ON/OFF.
3. To make the control action for each output independent of the other:
Go to the
CONTROL
menu.
Set
ACTION:1
or
ACTION:2
to either DIRECT or REVERSE action based
on the diagrams in the output examples section (
Figures 7.2 through 7.8).
4. Go to the
TUNING
menu.
Set values for
PID OFST:1
(or
ON OFST:1
) and
PID OFST:2
(or
ON OFST:2
).
These parameters allow the user to independently offset the point at which
output 1 and output 2 become active.
PID OFSET
units are in percent (%) of
control output;
ON OFST
is in engineering units. The settings can be used
to make sure there is a dead band, i.e., no controller output around setpoint.
They can also be used to overlap output 1 and output 2 so that both are “on”
in a small band around setpoint.
5. Set
MAN. RESET
(manual reset) term to 50%. This causes the PID output
to be 50% when there is zero error. This term is still active as a “load line”
setting when using automatic reset (integral), so set it to 50% whether using
automatic reset or not.
6.
REL. GAIN
(relative gain) changes the gain of Output 2 relative to Output 1.
Note that the relative gain can limit the maximum output available for Out-
put 2 when using PID control.
7. Go to the
CONTROL
menu.
Set
LOW OUT.
and
HIGH OUT.
to limit the maximum or minimum outputs
from Output 1 and Output 2. The actual limitation on the outputs is depen-
dent on the offset settings, the relative gain setting and the control action.
NOTE:
The duplex output states vary
depending upon:
1. Control Type (PID, On/Off, etc.)
2. Control Action (DA, RA)
3. Output Limits
4. Output Gap or Overlay, and
5. Ouput 2 Relative Gain and PID%
Output.
Please refer to the output state
examples in this section to confirm
that the configuration is appropriate
for the process.
NOTE:
Set manual reset/load line
parameters to 50% when using
Duplex control (
MAN. RST.:X
parameter is in the
TUNING
menu.)