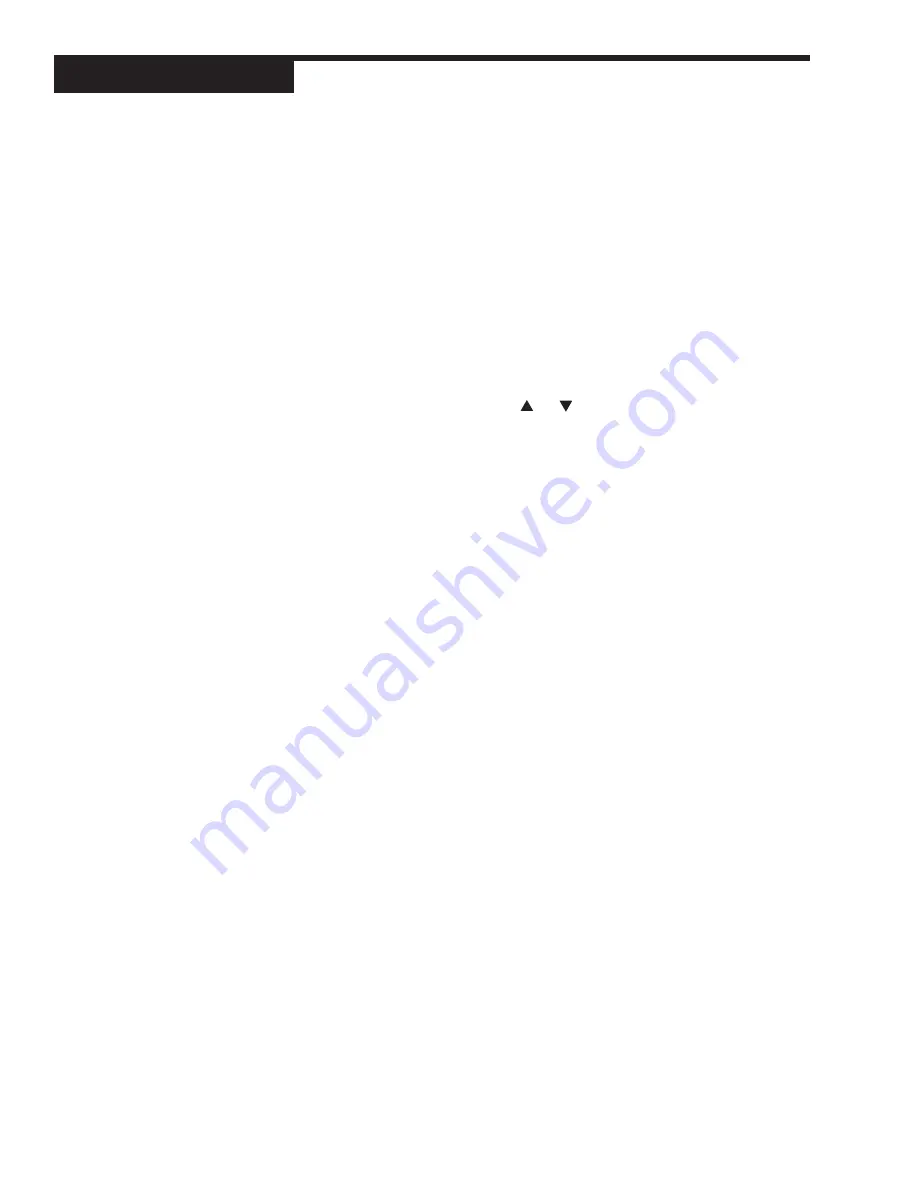
Specifications
A-14
Appendix 5
535-PROF User's Manual
DIGITAL INPUTS
A set of five external dry contacts or open collector transistor
driven inputs are available. Each can be configured to perform
one of the following functions:
• Select remote setpoint
• Select either direct or
reverse control action
• Select manual control•
Select second local setpoint
• Disable adaptive tuning
• Select a second set of
• Addressable through serial
PID values
communications only
• Acknowledge alarms
• Inhibit the reset term
• Simulate and keys
• Lock controller in manual
mode
• Simulate DISPLAY, FAST
• Select PV1 or PV2
and MENU keys
• Operate recipes
In addition, if the set of five digital inputs is installed, four may be
designated to select one of eight local setpoints (and associated
PID set, if desired) via a binary coded decimal (BCD) input.
SETPOINT SELECTION
A remote setpoint input is available. Signal is 0–20/4–20 mADC or
0–5/1–5 VDC (jumper selectable). Signal may be ratioed and
biased. Eight local setpoints may be stored in memory.
Setpoint selection is made via menu selection or digital
contact(s).
FAULT OUTPUT
One of the alarm outputs may be designated to also energize
if the input signal is lost.
SERIAL COMMUNICATIONS
Isolated serial communications is available using an RS-485
interface. Baud rates of up to 19,600 are selectable. The
protocol supports CRC data checking. If communications is
lost, a time-out feature will command the controller to a
particular control mode and specific setpoint or output if
desired. Outputs 2–4 and digital inputs can act as
“host-controlled” I/O independent of the controller’s function.
The PV may be sourced via this interface. May be installed in
the field.
Duplex control
is available if output modules are installed in the first
and second output sockets.
Position proportioning control
with feedback is available if mechani-
cal or solid state relay modules are installed in the first two output
sockets, and the slidewire feedback option is installed. Slidewire
feedback range is 0 to 1050ohms.
“Velocity” position proportioning control
is available by installing
mechanical or solid state relay modules in the first two output
sockets. A special algorithm controls an electric actuator without
the slidewire feedback signal.
Staged (split range) outputs
are available if analog modules are
installed in the first and second output sockets. This algorithm will
allow the output range to be split between the two outputs.
RETRANSMISSION OUTPUT
Based on available outputs (any socket not used for control), up
to two different variables can be simultaneously programmed for
retransmission. Each precise, 16-bit resolution output may be
scaled for any range. Variable selection includes: PV, SP, RAMP
SP, and OUTPUT.
ALARMS
The 535 controller has two software alarms. High and low alarms
may be sourced to the PV, SP, RAMP SP, DEVIATION and OUT-
PUT. If an alarm is tripped, the alarm message will show, the
ACK key will illuminate (if acknowledgeable) and the ALM icon
will light. If the alarm is tied to the first available non-control output,
the “1” below the ALM icon will light. Similarly, if the alarm is tied to
the second non-control output, the “2” below the ALM will light.
The availability of outputs determines how many alarms can be
tied to relays.
Up to two alarm outputs are available if an associated mechanical,
solid state relay or DC logic module is installed in any output
socket not used for control.
Global Alarm
feature allows one or more of the internal software
alarms to be tied to the same single, physical output. The
acknowledge key is active for alarms associated with either loop.