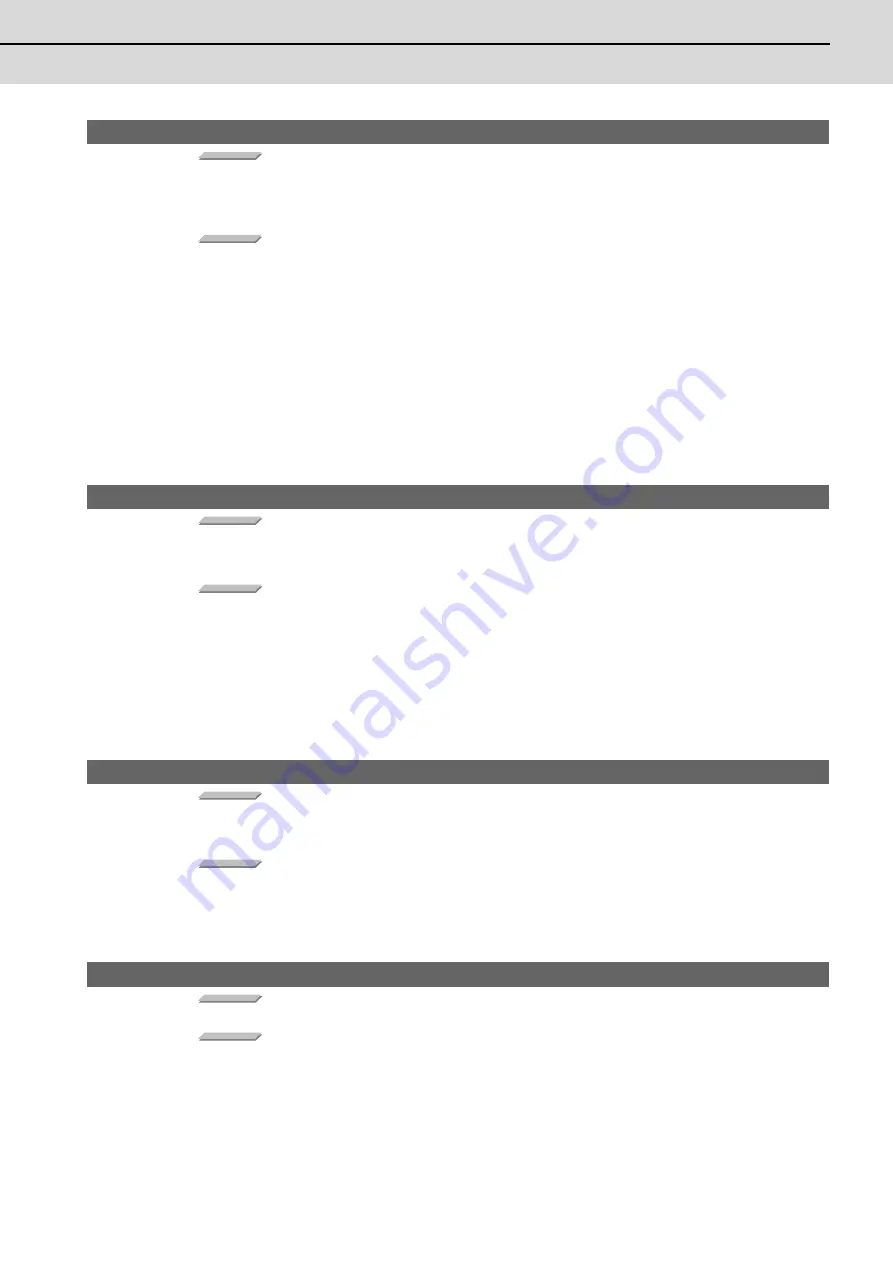
C70 Setup Manual
Appendix 2.4 MCP Alarms (Y)
459
Y07 Too many axes connected 000x
Details
The number of axes connected to each channel has exceeded the maximum number of connectable
axes.
The exceeded number of axes per channel is displayed as alarm No.
x: Exceeded number of axes at drive unit interface channel 1 (0 to F)
Remedy
- Correct the "#3024 sout (Spindle connection)" setting for the spindle to which the drive unit is
connected.
- Turn up the DIP switch for any unused axis in the multi-axes drive unit.
- Correct the "#1002 axisno (Number of axes)" and "#1039 spinno (Number of spindles)" settings.
- For the channel(s) with an alarm number other than "0", disconnect the connected axes as many as
shown in the alarm No. so that the number of connected axes will not exceed the maximum number
of connectable axes.
(Note 1) This alarm occurs when the number of the connected axes exceeded the maximum number of
the connectable axes assumed in the system.
(Note 2) This alarm indicates a communication timeout state of drive unit (with "AA" in the drive unit
LED display) as the initial communication is not executed.
(Note 3) If this alarm occurs, the alarm "Y03 Message: Drive unit unequipped" will not occur.
(Note 4) This alarm is displayed taking precedence over the alarm "Y02 System alarm" and "Y09 Too
many axisno connected".
Y09 Too many axisno connected Exceeded number of axes 000x
Details
The No. of the axis (drive unit's rotary switch No.) connected to each channel is bigger than the
maximum number of connectable axes.
x: "1" when the axis number at drive unit interface channel 1 is too big
Remedy
For the channel whose alarm number is "1", change the axis number (drive unit's rotary switch
number) to a number within the limit of the maximum number of connectable axes.
Be sure to turn down the rightmost DIP switch on each drive unit.
(Note 1) This alarm occurs when the number of the connected axes exceeded the maximum number of
the connectable axes assumed in the system.
(Note 2) If this alarm occurs, drive unit indicates a communication timeout (with "AA" in the LED
display) as the initial communication is not executed.
(Note 3) If this alarm occurs, the alarm "Y03 Message: Drive unit unequipped" will not occur.
(Note 4) This alarm is displayed taking precedence over the alarm "Y02 System alarm".
Y11 Node Detect Err 8002-8300 0x00
Details
Drive unit does not respond to the request from CNC when the CNC is turned ON.
Error No. shows the No. of communication phase at which the response stopped.
x: Station No. with the error (0 or later)
Remedy
The communication error may be caused by the drive unit software version that does not correspond to
the CNC software version. Check the drive unit software version.
This alarm is canceled after the CNC restarts.
When the alarm is not canceled, write down the alarm No. and the software version of each drive unit,
then contact service center.
Y14 VIR.AX AMP EQU. (Axis name)
Details
A drive unit is connected to a hypothetical axis (with "1" in "#2116 v_axis (Hypothetical axis)").
Remedy
- Disconnect the drive unit from the hypothetical axis.
- Correct the "#1021 mcp_no (Drive unit I/F channel No. (servo))" and servo drive unit rotary switch
settings.
Содержание C70
Страница 1: ......
Страница 3: ......
Страница 9: ......
Страница 11: ......
Страница 13: ......
Страница 18: ...1 1 Outline ...
Страница 21: ...1 Outline MITSUBISHI CNC 4 ...
Страница 22: ...5 2 GOT Initial Setup ...
Страница 73: ...2 GOT Initial Setup MITSUBISHI CNC 56 ...
Страница 74: ...57 3 PLC CPU Initial Setup ...
Страница 91: ...3 PLC CPU Initial Setup MITSUBISHI CNC 74 ...
Страница 92: ...75 4 CNC CPU Initial Setup ...
Страница 105: ...4 CNC CPU Initial Setup MITSUBISHI CNC 88 ...
Страница 106: ...89 5 Connecting and Setting up Multiple CNC CPU Modules ...
Страница 115: ...5 Connecting and Setting up Multiple CNC CPU Modules MITSUBISHI CNC 98 ...
Страница 116: ...99 6 Setting Machine Parameters ...
Страница 130: ...113 7 Setting the Position Detection System ...
Страница 153: ...7 Setting the Position Detection System MITSUBISHI CNC 136 ...
Страница 154: ...137 8 Deceleration Check ...
Страница 159: ...8 Deceleration Check MITSUBISHI CNC 142 ...
Страница 160: ...143 9 Setting the Tool Entry Prohibited Range ...
Страница 169: ...9 Setting the Tool Entry Prohibited Range MITSUBISHI CNC 152 ...
Страница 170: ...153 10 Data Backup and Restoration ...
Страница 184: ...167 Appendix 1 Explanation of Parameters ...
Страница 435: ...Appendix 1 Explanation of Parameters MITSUBISHI CNC 418 ...
Страница 436: ...419 Appendix 2 Explanation of Alarms ...
Страница 608: ...591 Appendix 3 Display on 7 segment LED ...
Страница 624: ......
Страница 628: ......