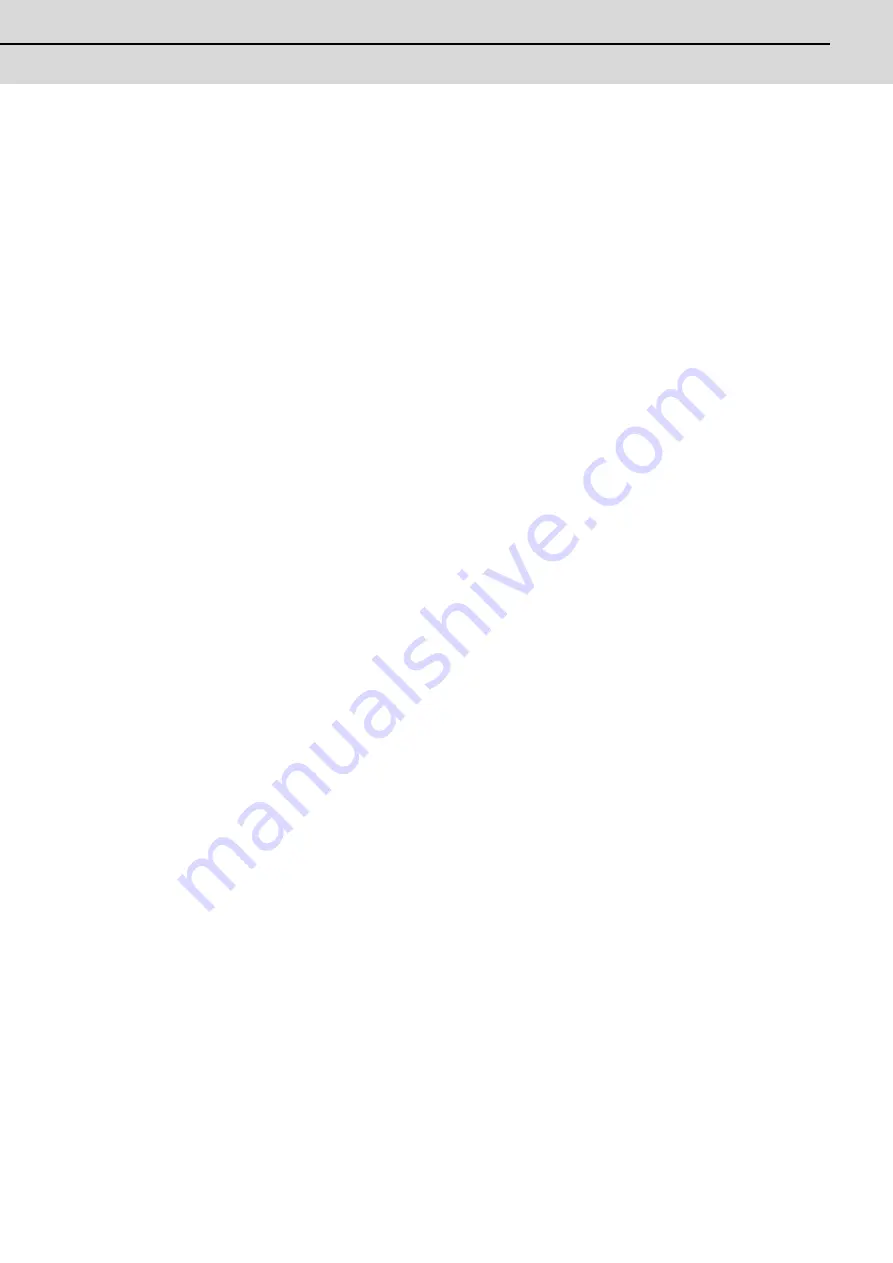
C70 Setup Manual
7.2 Adjustment of Reference Position Return in Relative Position Detection System
119
Grid point
The position detector has a Z-phase that generates one pulse per rotation. The 0-point position of this Z-phase is the grid
point.
Thus, there is a grid point per rotation of the position detector, and the machine has many grid points at a regular pitch.
The grid point can be set at intervals of grid space by setting the grid space (#2029 grspc). Thus, multiple grid points can
be set per detector rotation.
Grid amount
The grid amount is the distance from where the near-point detection limit switch leaves the near-point dog to the grid
point (electrical zero point) as the dog-type reference position return is executed.
The grid amount can be confirmed on the DRIVE MONITOR screen.
After setting the grid mask, the grid amount shows the distance from the grid mask OFF to the grid point.
G28 rapid traverse rate (#2025 G28rap)
Set the feedrate for dog-type reference position return in manual operation and the automatic operation.
The rapid traverse rate (#2001 rapid) is applied for the feedrate during the high-speed reference position return.
G28 approach speed (#2026 G28crp)
Set the approach speed to the reference position after decelerating to a stop by the near-dog detection. Since the
approach speed is accelerated and decelerated in steps (no-acceleration/deceleration), the mechanical shock, etc. could
occur if the speed is too large. The G28 approach speed should be set between 100 and 300 mm/min., or within 500
mm/min. at the fastest.
Reference position shift amount (#2027 G28sft)
When shifting the reference position from the electrical zero point, set the shift amount.
The shifting direction can be set only in the reference position return direction.
If the reference position shift amount is "0", the grid point (electrical zero point) will be the reference position.
Grid mask amount (#2028 grmask)
The first grid point after the dog OFF is regarded as the electrical zero point.
If the grid point is at the position where the near-point dog is kicked OFF, the position of electrical zero point may be at
the grid point where the dog is kicked OFF or at the next grid point because of the delay of the limit switch operation. This
causes a deviation of reference position by the amount of the grid space. Thus, the position that the dog is kicked OFF
needs to be at the approximate center of the grid space.
Adjustments are made by setting the grid mask amount or changing the near-point dog.
Setting the grid mask has the same effect as lengthening the near-point dog. Refer to the previous procedures for setting
the grid mask amount.
Grid space (#2029 grspc)
Set the distance between grids.
The normal grid space is the ball screw pitch value (#2218 PIT) or the movement amount per motor rotation set as a
millimeter measurement unit. To make the grid space smaller, set a divisor of the grid space.
<Calculation method for movement amount per motor rotation>
(1)
When linear feed mechanism is a ball screw:
The movement amount per motor rotation = the motor side gear ration / the machine side gear ratio x the ball
screw pitch
(2)
When linear feed mechanism is a rack and pinion:
The movement amount per motor rotation = the motor side gear ration / the machine side gear ratio x number
of pinion gear teeth x the rack pitch
(3)
For the rotary axis:
The movement angle per motor rotation = the motor side gear ration / the machine side gear ratio x 360
Содержание C70
Страница 1: ......
Страница 3: ......
Страница 9: ......
Страница 11: ......
Страница 13: ......
Страница 18: ...1 1 Outline ...
Страница 21: ...1 Outline MITSUBISHI CNC 4 ...
Страница 22: ...5 2 GOT Initial Setup ...
Страница 73: ...2 GOT Initial Setup MITSUBISHI CNC 56 ...
Страница 74: ...57 3 PLC CPU Initial Setup ...
Страница 91: ...3 PLC CPU Initial Setup MITSUBISHI CNC 74 ...
Страница 92: ...75 4 CNC CPU Initial Setup ...
Страница 105: ...4 CNC CPU Initial Setup MITSUBISHI CNC 88 ...
Страница 106: ...89 5 Connecting and Setting up Multiple CNC CPU Modules ...
Страница 115: ...5 Connecting and Setting up Multiple CNC CPU Modules MITSUBISHI CNC 98 ...
Страница 116: ...99 6 Setting Machine Parameters ...
Страница 130: ...113 7 Setting the Position Detection System ...
Страница 153: ...7 Setting the Position Detection System MITSUBISHI CNC 136 ...
Страница 154: ...137 8 Deceleration Check ...
Страница 159: ...8 Deceleration Check MITSUBISHI CNC 142 ...
Страница 160: ...143 9 Setting the Tool Entry Prohibited Range ...
Страница 169: ...9 Setting the Tool Entry Prohibited Range MITSUBISHI CNC 152 ...
Страница 170: ...153 10 Data Backup and Restoration ...
Страница 184: ...167 Appendix 1 Explanation of Parameters ...
Страница 435: ...Appendix 1 Explanation of Parameters MITSUBISHI CNC 418 ...
Страница 436: ...419 Appendix 2 Explanation of Alarms ...
Страница 608: ...591 Appendix 3 Display on 7 segment LED ...
Страница 624: ......
Страница 628: ......