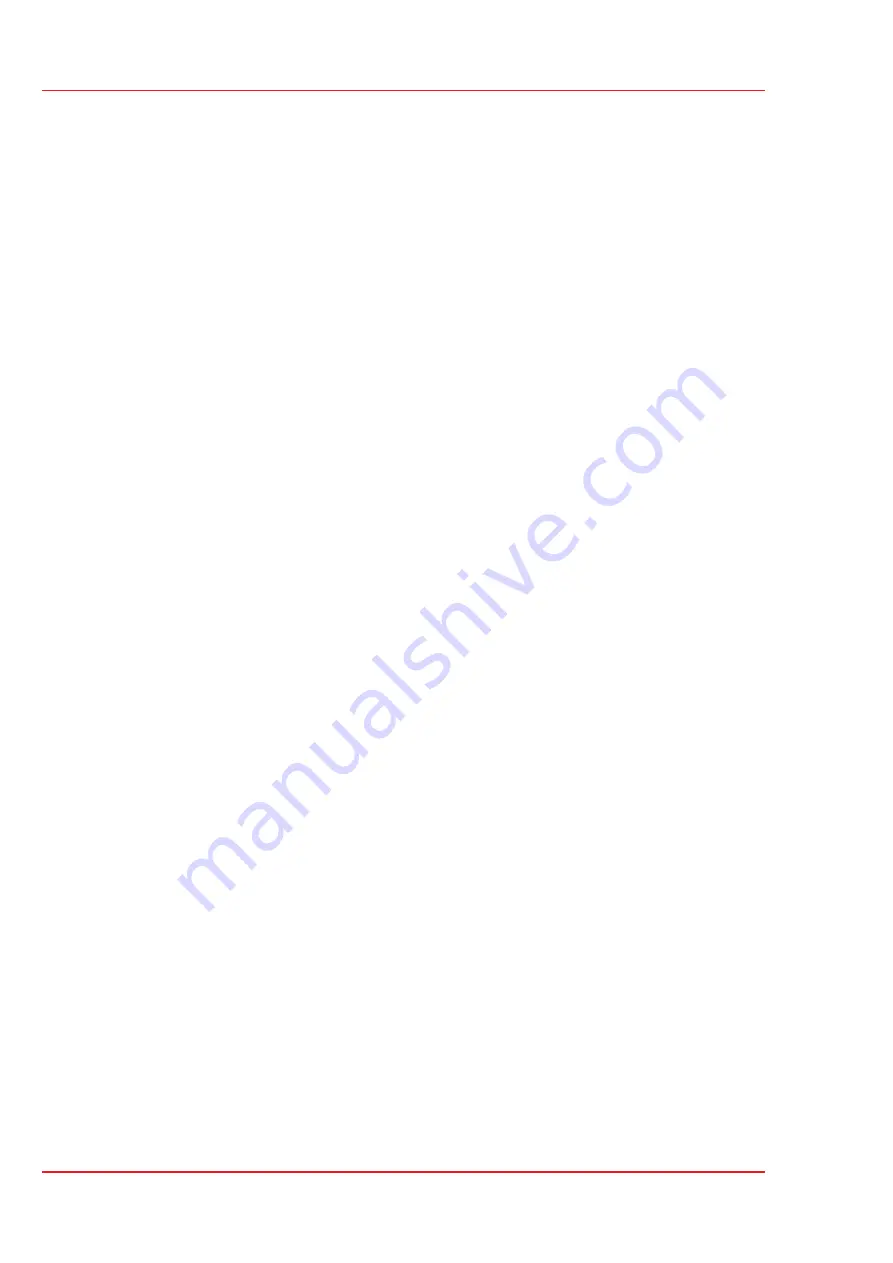
Electronic Noise
If the noise has been identified as electronic noise, then the ion counting threshold
level should be checked as follows:
Increase
Ion Counting Threshold
until the valleys of the peak-to-peak noise
are brought down to the zero line. A value of 30 is typical.
It is not possible to give absolute values for typical peak-to-peak electronic noise, as
this is dependent on detector gain and the dwell time used for the MRM experiment.
However, the electronic noise should be fairly constant for a particular instrument, so
a measurement made previously under the same MRM conditions (with ion energies
negative) should provide a meaningful comparison to see if the electronic noise level
has changed.
If, after checking the ion counting threshold as above, electronic noise is considered to
be the dominant source of noise and has become significantly worse since instrument
installation then further investigations should be carried out by a qualified Micromass
engineer.
High Back Pressure
For electrospray, a higher than normal back pressure readout on the HPLC pump,
together with a slowing of the actual solvent flow at the probe tip, can imply that there
is a blockage in the capillary transfer line or injection loop due to particulate matter
from the sample. To clear the blockage:
Remove the probe from the source and increase the solvent flow to 50 µl/min to
remove the blockage.
Often, injections of neat formic acid help to redissolve any solute which has
precipitated out of solution.
If the blockage cannot be cleared in this fashion:
Remove the finger-tight nut and tubing from the back of the probe.
If the back pressure remains high, replace the tubing with new tube (or first try
removing both ends of the tube).
If the back pressure falls, replace the stainless steel sample tube inside the probe
(or try reversing the tube to blow out any blockage).
Reconnect the tubing to the probe.
The solvent flow can be readjusted and the probe replaced into the source.
To check the flow rate from the solvent delivery system, fill a syringe barrel or a
graduated glass capillary with the liquid emerging from the probe tip, and time
a known volume, say 10µl.
Maintenance and Fault Finding
Page 208
Quattro Ultima
User's Guide
Содержание Quattro Ultima
Страница 2: ...Quattro Ultima User s Guide...
Страница 68: ......
Страница 100: ...Data Acquisition Page 100 Quattro Ultima User s Guide...
Страница 117: ...Mass Calibration Page 117 Quattro Ultima User s Guide...
Страница 140: ...Mass Calibration Page 140 Quattro Ultima User s Guide...
Страница 212: ...Maintenance and Fault Finding Page 212 Quattro Ultima User s Guide...
Страница 222: ...Reference Information Page 222 Quattro Ultima User s Guide...