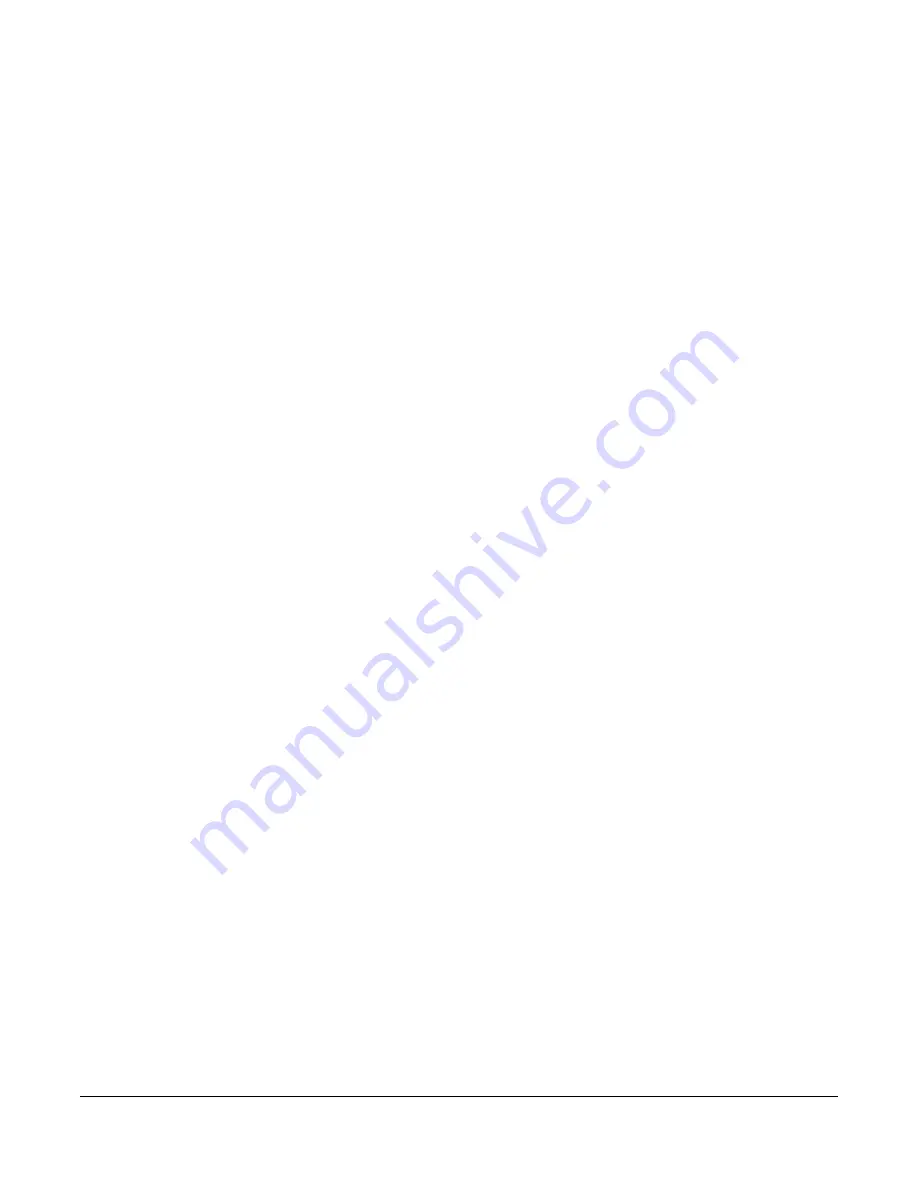
IMPULSE•G+/VG+ Series 4 Technical Manual
November 2022
Page 209
6.2.7 BE8–Brake Slipping Alarm
Definition
A BE8 alarm indicates that the VFD has detected that the brake is slipping after the brake is set. A BE8 alarm will
occur if the load is moving greater than the Brake Slip Detection Speed (C08-23) when the brake is set. When this
occurs, the VFD will go into load float while the brake is set.
NOTE:
This alarm typically indicates a failed brake. Power should NOT be removed while this alarm is active and
the load should be moved to a safe location and lowered before proceeding with any corrective action.
Corrective Action
1. Check the brake for proper operation and adjustment. If the brake does not set, is improperly adjusted or is
excessively worn, it may not be able to hold the load and encoder pulses will be received.
2. Check the encoder cable for damage and proper grounding. Replace it if a problem is found.
•
Each of the encoder signals should be checked for excessive noise.
•
The shielded encoder cable should be properly grounded.
•
Visually inspect the cable for damage.
3. Check the alignment of the encoder pulse wheel and sensor head, or the encoder shaft coupling. If the pulse
wheel is misaligned or the shaft coupling is loose the VFD may get erratic pulse signals and cause a BE8
alarm. Make repairs before attempting to operate the hoist.
4. If none of the above steps has identified a valid problem(s), the brake may need to be replaced.
NOTE:
It is desirable to have as fast an alarm reaction time as possible without causing nuisance alarms.
6.2.8 OC–Over Current Fault
Definition
An over current fault is caused if the output current exceeds 200% of the VFD rated output current. This fault can
be caused by short circuits in the wiring or in the motor, or caused by parameters that are not adjusted properly.
Another cause of this fault could be erratic or no encoder feedback. In the last instance, the VFD is trying to
command the motor to hold a position, but due to the encoder problem, is unable to find the correct position. This
would cause the VFD to increase current output to the motor in an attempt to correct the position.
Corrective Action
1. Check the motor wiring and the motor itself for a short between phases.
2. Check the alignment of the encoder pulse wheel and sensor head, or the encoder shaft coupling. If the pulse
wheel is misaligned or the shaft coupling is loose the VFD may get erratic pulse signals or no signals at all.
Make repairs before attempting to operate the hoist.
3. If the encoder has no mechanical problems, the encoder cable should be checked for damage.
•
Each of the encoder wires should be checked for continuity.
•
The wires should be checked for shorts between any two wires.
•
The shield should be checked for proper grounding.
•
The wires should be checked for shorts to the shield or ground.
•
Visually inspect the cable for damage.
4. If none of the above steps has identified a valid problem(s), check the torque limit parameters (C07-01 to C07-04).
If these parameters have been changed to allow a higher torque value, it could cause OC faults.
NOTE:
Changing these parameters may cause DEV or OL faults. Only a trained technician should make
modifications. It is desirable to have a fast fault reaction time without causing nuisance faults.
Содержание Impulse G+ series 4
Страница 20: ...IMPULSE G VG Series 4 Technical Manual November 2022 Page 20 Figure 2 1 Capacitor Reform Diagrams...
Страница 30: ...IMPULSE G VG Series 4 Technical Manual November 2022 Page 30 Figure 3 1 Typical Connection Diagram...
Страница 53: ...IMPULSE G VG Series 4 Technical Manual November 2022 Page 53 4 3 2 Menu Structure Figure 4 1 Menu Structure...
Страница 243: ...IMPULSE G VG Series 4 Technical Manual November 2022 Page 243 Figure B 5 Figure B 6 Figure B 7...
Страница 246: ...IMPULSE G VG Series 4 Technical Manual November 2022 Page 246 Figure B 8 Figure B 9 Figure B 10 Figure B 11...
Страница 248: ...IMPULSE G VG Series 4 Adjustable Frequency Vector Crane Controls Technical Manual November 2022...