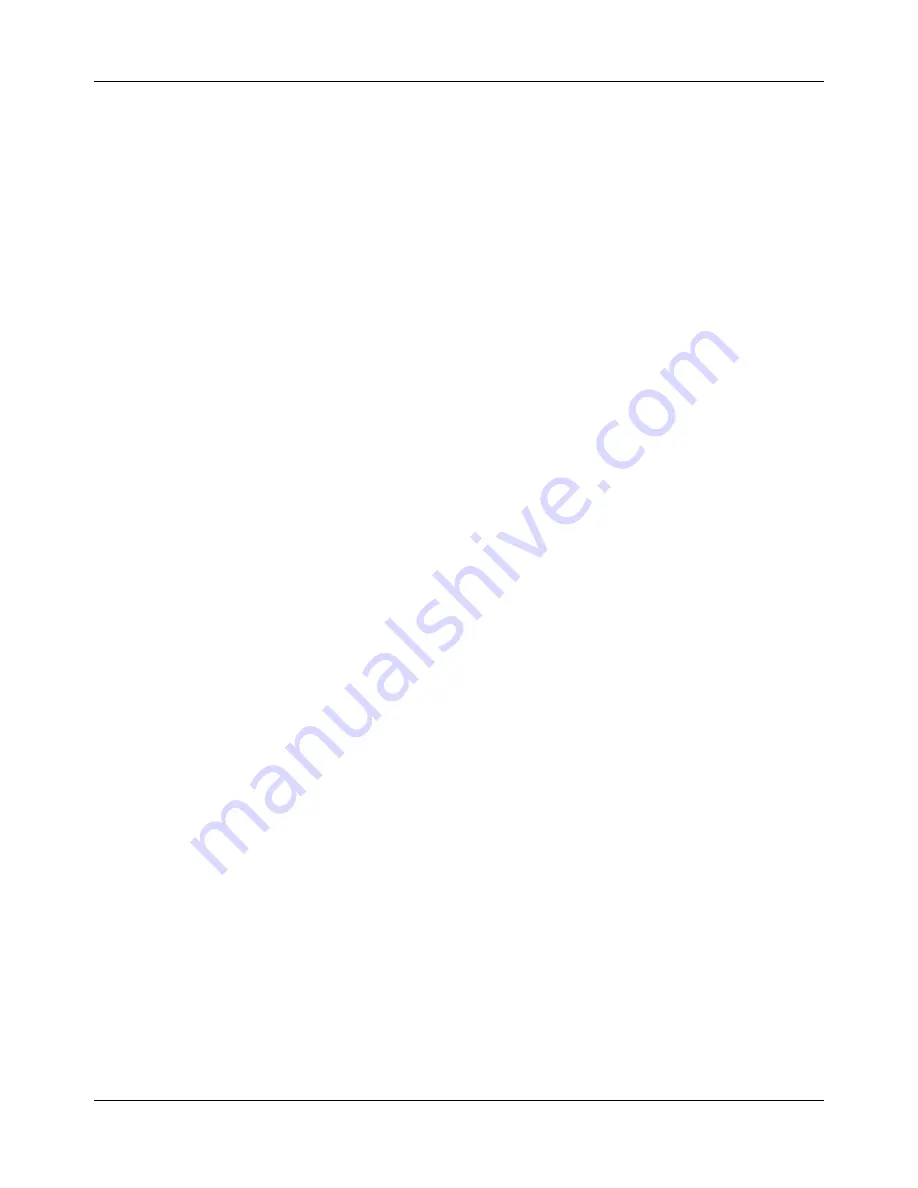
Operation
Theory of Operation
MagneMover LITE User Manual
5
Rockwell Automation Publication MMI-UM002E-EN-P - March 2016
•
The vehicle master will use the position of the most recently acquired block
farthest from the vehicle as an interim destination (target) to calculate the next
profile set point (Pset, Vset, Aset).
•
The vehicle master handles all collision avoidance ensuring brick-wall head-
way is maintained between vehicles.
5.
The vehicle master controls the vehicle based on the profile set points as inputs.
During the move, vehicle data such as actual position, velocity, and interim destination
are sent back to the Node Controller, typically every 100-200 ms, to provide the Host
Controller some level of feedback as to where the vehicle is located.
6.
The vehicle master continues to generate updated movement profiles based on the
order and continues to control the vehicle based on the new profile set points until the
vehicle is handed off to the next vehicle master or it reaches its destination.
The vehicle master hands-off vehicle control to the motor controller in the next motor
as the vehicle moves across motor boundaries. The new master ‘picks up’ where the
old one left off for profile generation. The new master is now responsible to continue
the closed-loop control of the vehicle.
7.
The movement order is finished when the vehicle position is equal to the ordered des-
tination.
Motor Cogging
Brushless Permanent Magnet (BPM) motors that are iron core based inherently exhibit cog-
ging forces. In traditional BPM motors, these are felt when turning the shaft of the motor and
are periodic in nature. The periodicity in this case would be expressed in degrees and the mag-
nitude and direction of this cogging force would vary as a function of shaft position.
Linear motors that utilize a iron core also exhibit cogging forces. The main difference
between rotary motors and linear motors is that in linear motors these forces are periodic as a
function of distance versus angle. In the linear motor these forces will tend to pull the vehicle
forward or backward at specified intervals along the motor.
MagneMotion’s MagneMover LITE linear motors do not utilize an iron core. As such, they do
not exhibit any cogging forces.
Motor Blocks
A motor block is a discrete motor section within each MagneMover LITE motor or switch as
shown in
. It is an independently controlled linear motor driven by
one inverter. This is the stator (motor primary) and consists of copper windings. There is no
iron core to the motor, which eliminates the attractive force between the magnet array and
motor.
Содержание MagneMover LITE
Страница 1: ...MagneMover LITE User Manual ...
Страница 284: ...Operation 28 MagneMotion Rockwell Automation Publication MMI UM002E EN P March 2016 This page intentionally left blank ...
Страница 381: ...MagneMover LITE User Manual 501 Rockwell Automation Publication MMI UM002E EN P March 2016 Notes ...