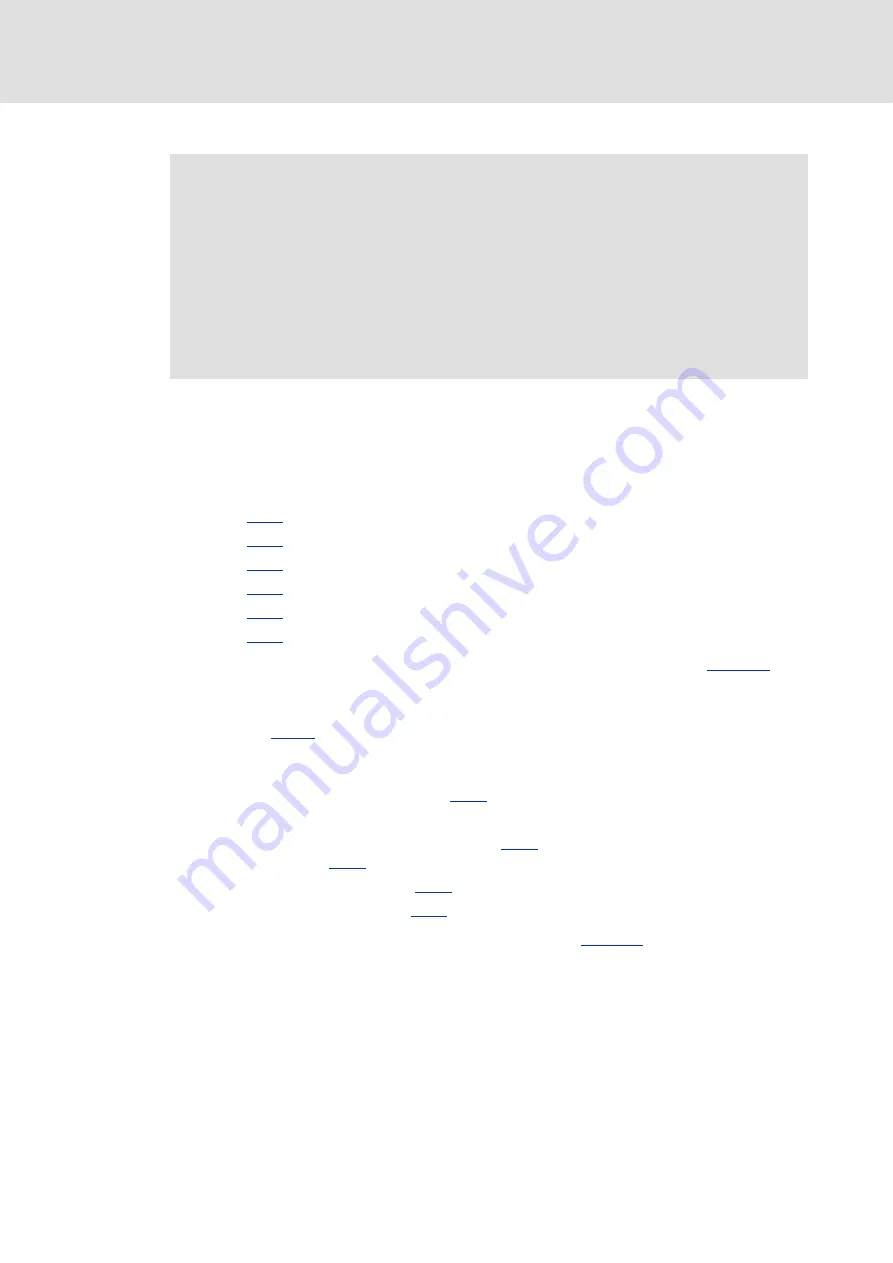
Firmware 03.00 - DMS EN 5.0 - 07/2009
L
91
8400 BaseLine D | Software Manual
Motor control (MCTRL)
Selection of the operating mode
How to carry out the automatic motor parameter identification:
1. Inhibit the controller (e.g. LOW signal at terminal X4/RFR).
Wait until the drive is at standstill.
2. Transfer the nameplate data to the following codes:
•
, rated motor power
•
, rated motor speed
•
, enter value according to the connection method (
/
)
•
, enter value according to the connection method (
/
)
•
, enter value according to the connection method (
/
)
•
, motor cos
ϕ
3. Start the motor parameter identification with the device command
4. Enable the controller (e.g. HIGH signal at terminal X4/RFR).
The identification process starts. The progress of the identification can be read out
.
The identification process takes about 30 s.
During this time the following steps are executed:
• The motor stator resistance
is measured.
• The inverter error characteristic is measured.
• The motor magnetising inductance
and the motor stator leakage
are calculated from the data entered.
• The V/f base frequency
is calculated.
• The slip compensation
is calculated.
5. The identification is completed when the value in
is back to "0".
6. Inhibit the controller (e.g. LOW signal at terminal X4/RFR).
Note!
• The motor parameter identification must be carried out when the motor is
cold!
• The load machine may remain connected. Holding brake, if present; may
remain in the braking position.
• With an idling motor, a small angular offset may occur at the motor shaft.
• The motor parameter identification may be aborted by unstable drive
behaviour (e.g. through a special motor or a great deviation between inverter
and motor power).