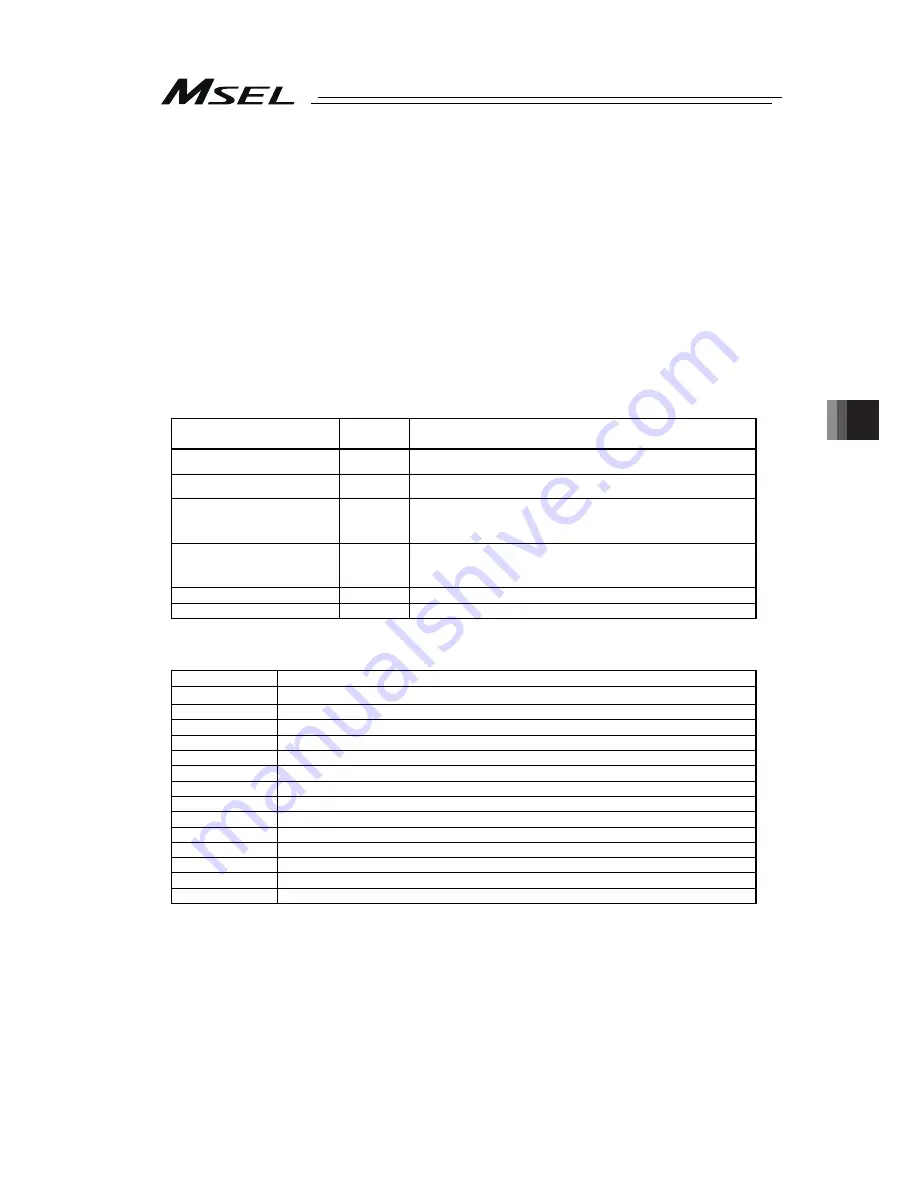
Chapter 7
Appendix
201
7.2 Stopping method and Recovery
7.2.1 Stopping method
Actuator operation can be stopped in two methods: normal operation stop and emergency
stop.
1) Normal operation stop
Normal position control is active: Set a deceleration operation plan and cause the
actuator to decelerate to a stop, according to the plan,
under normal position control
2) Emergency stop (stop with immediate servo-OFF)
Cancel the operation plan and immediately turn OFF the servo (power supply to the motor
is cut off).
How operation is stopped in each condition is explained below.
Stop command,
Condition
Stopping
method
Remarks
Pause
1)
Servo OFF
1)
Emergency stop
1)
Since the motor drive source is cut off by hardware means,
the deceleration operation plan may have to be forcibly
stopped beforehand.
SEL program command
1)
Stop is made when the following four commands are
issued.
HOLD, CANC, STOP, ABPG
Errors not described in list
1)
Errors in list
2)
Error of stop with immediate servo OFF in 2)
Error No.
Error name
614
Driver synchronizing communication LRC error
6BB
Deviation overflow error (home return not yet complete)
6BC
Stop deviation overflow error (home return not yet complete)
B05
Estimate stroke exceeded during home return
B11
Home position sensor escape timeout error
C6B
Deviation overflow error
C99
Home position undetected error
CA5
Stop deviation overflow error
CC6
Driver error initial detection
D0A
Driver overload error
D10
IPM error (POE0)
D15
Driver CPU down status error
D17
Main CPU alarm status error
F00 to FBF
All system-down level errors
Содержание MSEL
Страница 1: ...MSEL Controller Instruction Manual Fifth Edition ...
Страница 2: ......
Страница 4: ......
Страница 30: ...22 ...
Страница 44: ...Chapter 1 Specifications Check 36 ...
Страница 102: ...Chapter 4 Home Return Absolute Reset 94 ...
Страница 232: ......
Страница 233: ......