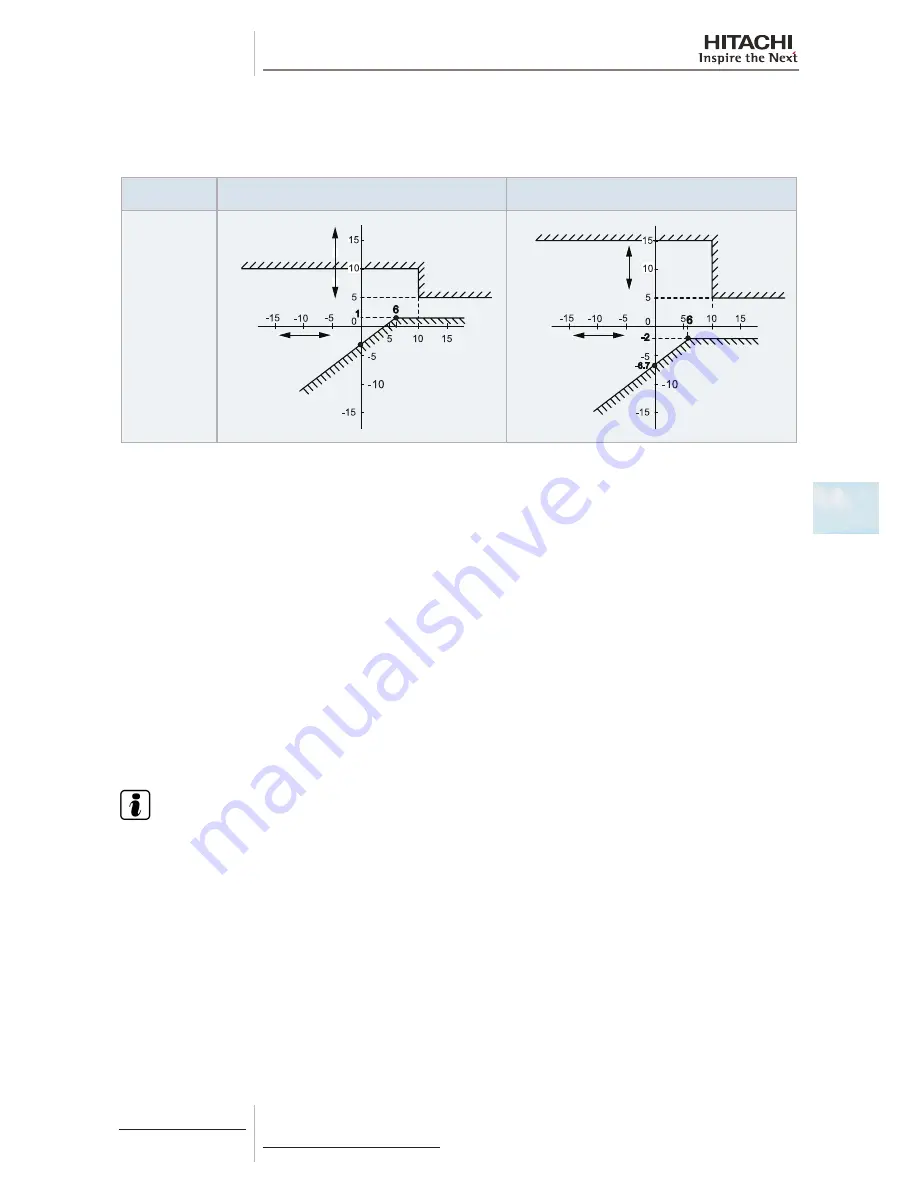
5 Control System
153
SMGB0087 rev.0 - 12/2013
5
Condition for Starting Defrost
1
Standard defrost
a.
Temperature condition
Model
RAS-(2-2.5)HVNP1
RAS-3HVNC1
RAS-3HVNP1E
RAS-(4-12)H(V)N(P/C)(1)(E)
Temperature
condition under
defosting
operation
-4.6
Defrosting
operation
start area
Defrosting
operation
stop area
Outdoor
temperature
(ºC)
Outdoor evaporating
temperature (ºC)
(pipe)
Defrosting
operation
start area
Defrosting
operation
stop area
Outdoor
temperature
(ºC)
Outdoor evaporating
temperature (ºC)
(pipe)
b.
Condition for Operating Time of Defrost Operation Start
The defrosting operation is started when the temperature condition is met “(a) Temperature Condition” after the heating
operation is performed for 40 to 120 minutes. The heating operation time is determined by estimating the amount of fros-
ting on the heat exchanger.
2
Forced Defrost
Condition for Starting
The forced defrosting operation is started when all the following conditions are met.
a.
120 minutes are passed after the reversing valve is “ON”.
b.
The outdoor temperature is lower than 10ºC.
c.
The accumulated heating operation time is more than 60 minutes. (*1)
(The accumulated time is reset when the operation is stopped or the defrosting operation is performed.)
d.
The compressor is operated continuously for more than 1 and half minutes. (*2)
e.
The outdoor evaporating temperature is lower than 5ºC (*3) right before starting the operation.
f.
The pressure switch for control is “OFF”.
N O T E
For RAS-(2-2.5)HVNP1 / RAS-3HVNC1:
• (*1) More than 39 minutes.
• (*2) If outdoor temperature is less than -6ºC then the compressor is operated continuously for more than 2 minutes. If
outdoor temperature is more than -6ºC then the compressor is operated continuously for more than 9 minutes.
• (*3) Less than 6ºC.
Содержание RAS-(2-6)HVNP1(E)
Страница 2: ......
Страница 4: ... II ...
Страница 28: ......
Страница 134: ...4 Electrical wiring 120 SMGB0087 rev 0 12 2013 4 7 3 RAS 3HVNP1E 1 230V 50Hz XEK01261_0 ...
Страница 136: ...4 Electrical wiring 122 SMGB0087 rev 0 12 2013 4 7 4 RAS 4 6 HVNP1E 1 230V 50Hz XEK01262_1 ...
Страница 138: ...4 Electrical wiring 124 SMGB0087 rev 0 12 2013 4 7 6 RAS 4 6 HNP1E 3N 400V 50Hz XEK01263_2 ...
Страница 140: ...4 Electrical wiring 126 SMGB0087 rev 0 12 2013 4 7 7 RAS 4 6 HVNC1E 1 230V 50Hz XEK01264_4 ...
Страница 142: ...4 Electrical wiring 128 SMGB0087 rev 0 12 2013 4 7 8 RAS 4 6 HNC1E 3N 400V 50Hz XEK01265_4 ...
Страница 144: ...4 Electrical wiring 130 SMGB0087 rev 0 12 2013 4 7 10 RAS 8 10 HN P C E 3N 400V 50Hz XEK01288_3 ...
Страница 146: ...4 Electrical wiring 132 SMGB0087 rev 0 12 2013 4 7 12 RAS 12HN P C 3N 400V 50Hz 7T146440 ...
Страница 148: ......
Страница 204: ......
Страница 220: ......
Страница 332: ......
Страница 353: ...9 Spare parts 339 SMGB0087 rev 0 12 2013 9 RAS 8 10 HNCE Spare Parts Document EPN 201211D ...
Страница 354: ...9 Spare parts 340 SMGB0087 rev 0 12 2013 9 6 2 Electrical parts View from P Spare Parts Document EPN 201211D ...
Страница 362: ......
Страница 484: ......
Страница 496: ......
Страница 497: ......