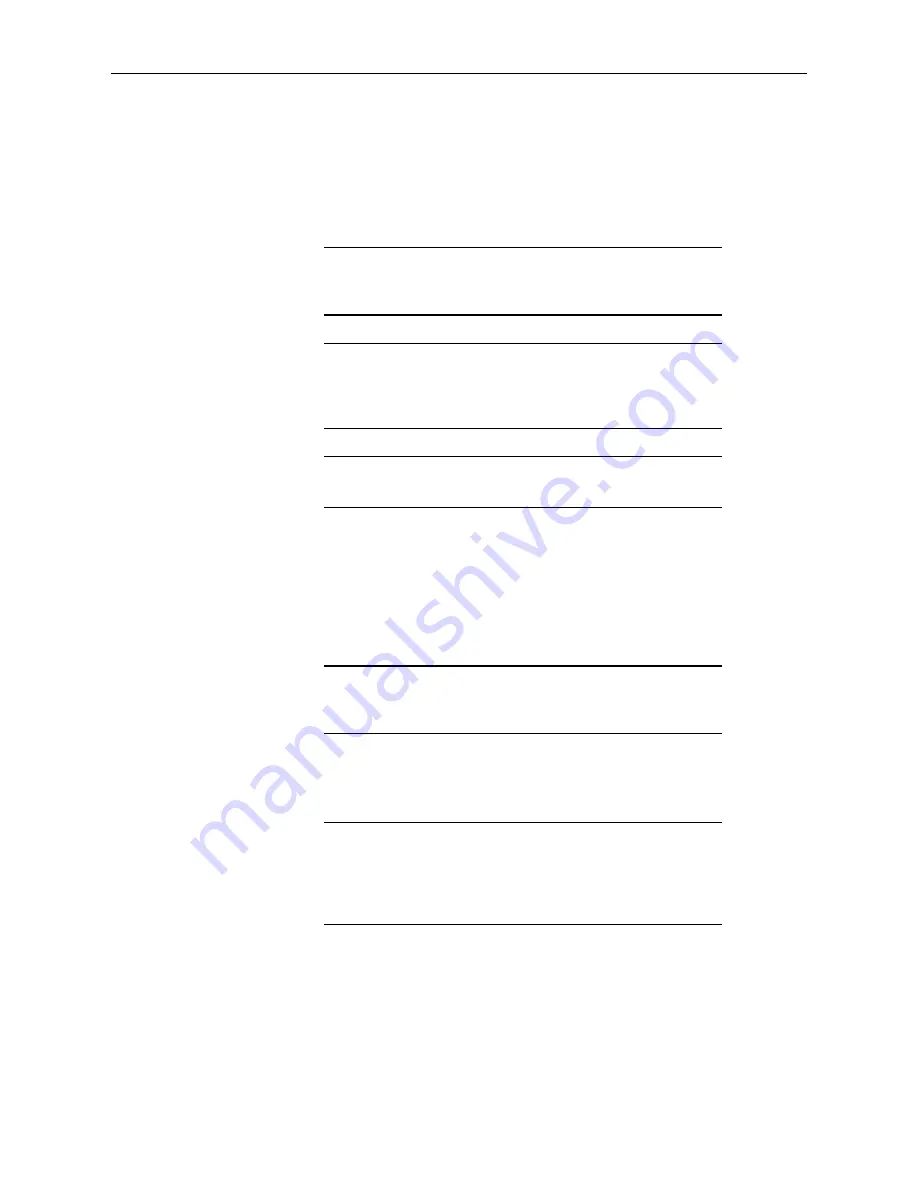
CPEC300/306/310 Closed-Path Eddy-Covariance Systems
29
Install cylinders in close proximity to the CPEC310 system enclosure. Each
cylinder must have a pressure regulator to control the outlet pressure at 10 psig
and must have a 1/4-in Swagelok fitting on the outlet. Connect regulators to the
valve module inlets using 1/4-in OD tubing or pre-swaged tube assemblies.
Minimize the length of these tubes to reduce the equilibration time after the
zero or CO
2
span cylinder is selected. Refer to Appendix
(p. J-1)
for information on installing and replacing Swagelok fittings.
Flow meters and needle valves are not needed because the
CPEC310 valve module has a proportional-control valve to
actively control the flow of zero and span gas to the EC155.
Make sure there are no leaks in the regulators or the connections
to the valve module. For automatic operation, the tank shutoff
valves are left continuously open. A plumbing leak could cause
the contents of the tank to be lost.
When inlets are not in use, replace the Swagelok plugs to keep the
system clean.
Connect the valve module’s
Analyzer
outlet
to the
Zero/Span
fitting on back
of the EC155 analyzer. Similar tubing or pre-swaged tube assembly is
recommended for this connection. The length of this tube should also be
minimized to reduce equilibration time.
Open the shutoff valves on the cylinders and set the pressure regulators for
10 ± 5 psig delivery pressure.
If the pressure is adjusted too high, slightly loosen the tube fitting
to bleed off the excess pressure. Retighten the fitting when the
proper setting is reached.
The
H2O Span
inlet is bypass equipped, allowing continuous flow. This inlet
can be connected directly to the output of a dewpoint generator. The bypass on
this inlet will avoid pressurizing the dewpoint generator.
Some systems, such as the AP200 CO
2
/H
2
O Atmospheric Profile
system, require a tee in the connection from the dewpoint
generator to bleed off excess flow and avoid pressurizing the
dewpoint generator. Do not use a tee to connect a dewpoint
generator to the CPEC310.
NOTE
NOTE
NOTE
NOTE
NOTE
Содержание CPEC300
Страница 1: ...CPEC300 306 310 Closed Path Eddy Covariance Systems 10 18 Copyright 2018 Campbell Scientific Inc ...
Страница 17: ...CPEC300 306 310 Closed Path Eddy Covariance Systems 8 FIGURE 4 8 CPEC306 system ...
Страница 54: ...CPEC300 306 310 Closed Path Eddy Covariance Systems 45 ...
Страница 55: ...CPEC300 306 310 Closed Path Eddy Covariance Systems 46 ...