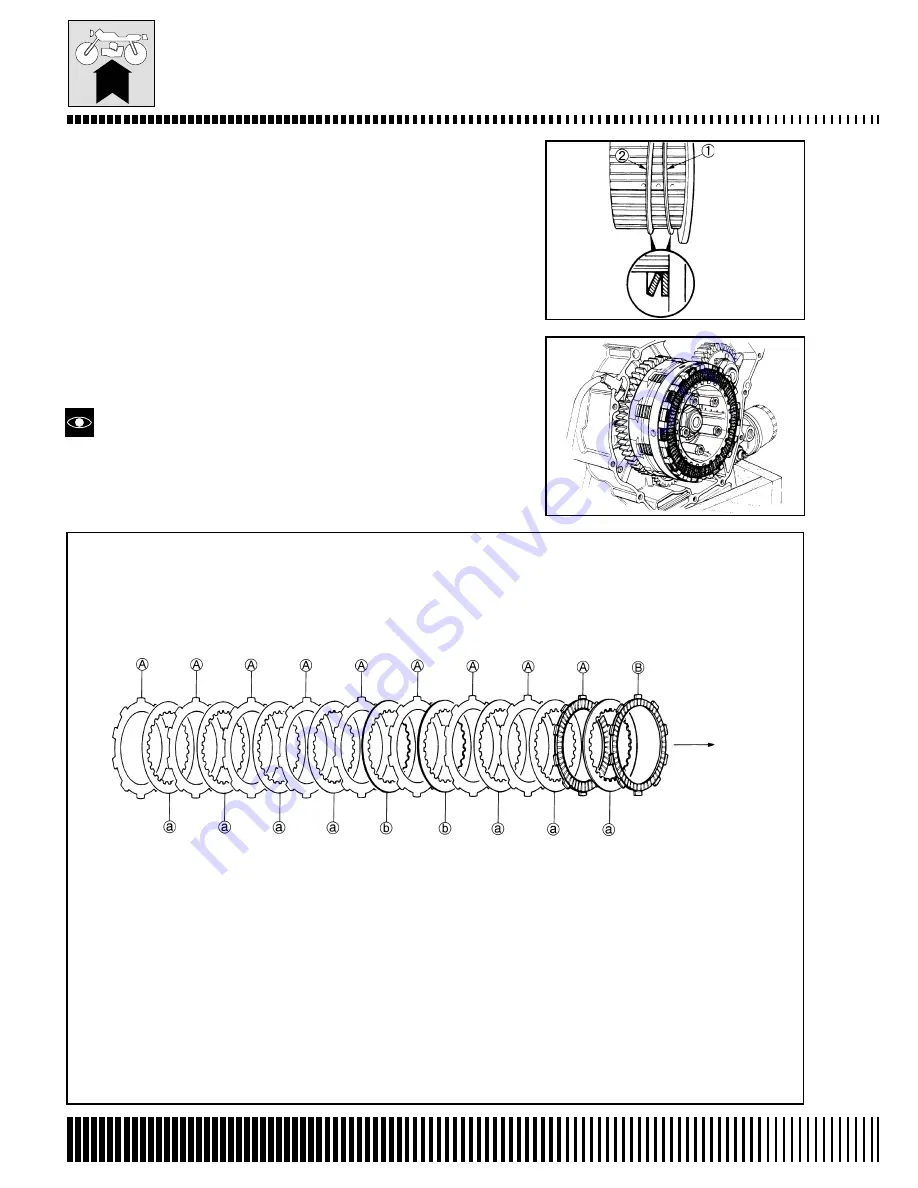
D.54
ENGINE
DRIVING PLATES
A No. 1 driving plate (inside diameter): 101 mm (3.976 in) 9 pcs
B No. 2 driving plate (inside diameter): 108 mm (4.252 in) 1 pcs
DRIVEN PLATES
Two types of driven plates, no. 1 and no. 2, are used in the clutch system. The two plate types differ in thick-
ness.
a No. 1 driven plate (thickness): 1,6 mm (0.063 in) 7 pcs
b No. 2 driven plate (thickness): 2,0 mm (0.079 in) 2 pcs
• Correctly fit spring washer seat 1 and spring washer 2 to the clutch
drum.
• Insert the clutch driving and driven plates one by one into the clutch
drum in the order shown in the figure. Insert no.2 driving plate B
first. (There are two types of driving plates, no. 1 and no. 2, differ-
ing in inside diameter.)
Insert the outermost no. 1 driving plate into the clutch bell housing
grooves as shown in the figure.
Inwards
Содержание Navigator
Страница 5: ...A 1 GENERAL INFORMATION A Section ...
Страница 9: ...B 1 MAINTENANCE B Section ...
Страница 10: ...B 2 MAINTENANCE Maintenance and tuning B 4 Compression check B 23 Oil pressure check B 24 Technical data B 25 ...
Страница 45: ...C 1 INJECTION AIR INTAKE SYSTEM C Section ...
Страница 118: ...C 74 INJECTION AIR INTAKE SYSTEM ...
Страница 119: ...D 1 ENGINE D Section ...
Страница 130: ...D 12 ENGINE Gradually lower the power plant When removing the engine from the frame take care not to damage either ...
Страница 199: ...D 81 ENGINE CAMSHAFT CYLINDER HEAD ...
Страница 204: ...D 86 ENGINE VALVE TIMING DIAGRAM FRONT FRONT CYLINDER TDC OF COMPRESSION STROKE ...
Страница 239: ...D 121 ENGINE Location of thicker 2 0 mm driven plate ...
Страница 269: ...D 151 ENGINE CRANKCASE GEARBOX CRANKSHAFT CONNECTING ROD ...
Страница 277: ...D 159 ENGINE ...
Страница 297: ...D 179 ENGINE ENGINE LUBRICATION SYSTEM ...
Страница 298: ...D 180 ENGINE ...
Страница 299: ...E 1 SUSPENSIONS AND WHEELS E Section ...
Страница 300: ...E 2 SUSPENSIONS AND WHEELS Front wheel E 3 Front suspension E 6 Rear wheel E 17 Rear suspension E 20 Frame E 24 ...
Страница 324: ...F 1 BRAKES F Section ...
Страница 326: ...F 3 BRAKES FRONT BRAKE Type Fixed twin discs Ø 296 mm Double piston pincers REAR BRAKE Type Fixed single disc Ø 240 mm ...
Страница 337: ...F 14 BRAKES ...
Страница 338: ...G 1 ELECTRICAL EQUIPMENT G Section ...
Страница 340: ...G 3 ELECTRICAL EQUIPMENT ...
Страница 375: ...G 38 ELECTRICAL EQUIPMENT ...
Страница 376: ...H 1 ENGINE COOLING H Section ...
Страница 390: ...I 1 SPECIFIC TOOLING I Section ...
Страница 391: ...I 2 SPECIFIC TOOLING ...
Страница 393: ...I 4 SPECIFIC TOOLING ...
Страница 394: ...L 1 TORQUE PRESSURES L Section ...
Страница 400: ...M 1 INDEX M Section ...
Страница 405: ...M 6 INDEX ...
Страница 406: ...M 7 INDEX ...
Страница 407: ...M 8 INDEX ...